It is not done yet, but the end is in sight. If I would have known it would be this much work, I don't think I would have started in the first place.
I had always looked at the tops out there and thought I could do better (famous last words). All of the others out there have too many flat areas with no curves for my taste, so this one is all curves and no flat areas.
Sorry for the lighting in the pictures (white on a bright day). I will take more later if there is any interest.
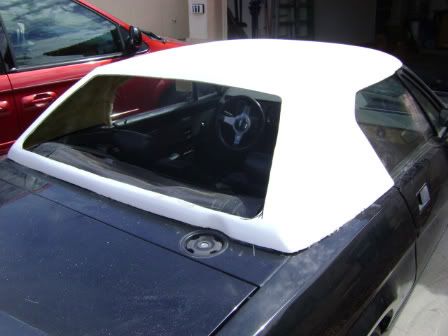
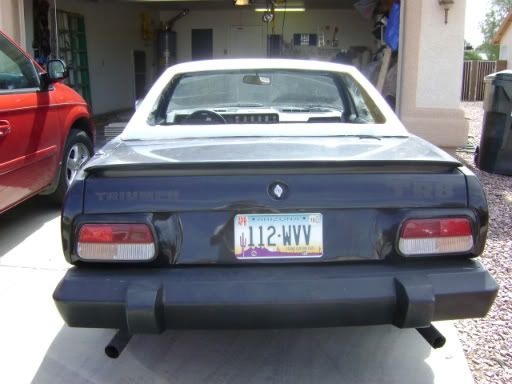
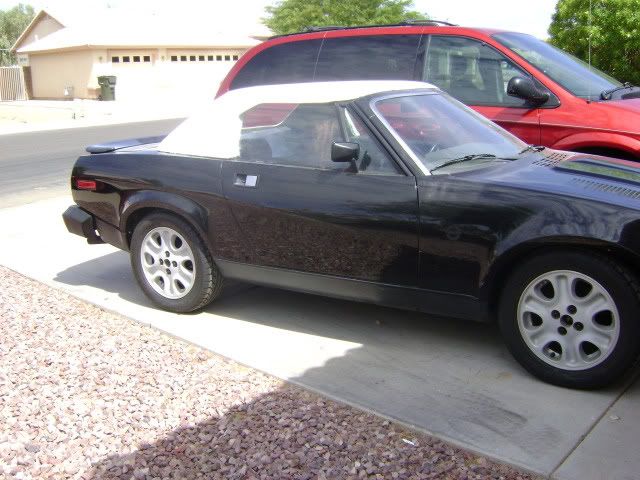
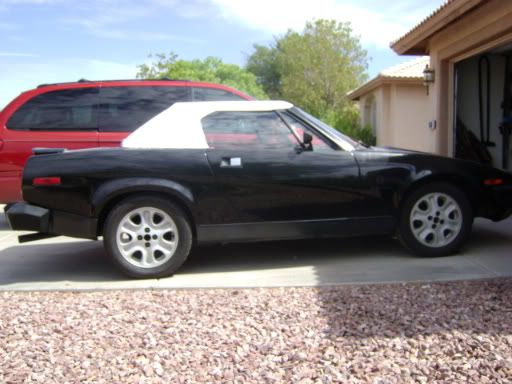

Rob