Well I decided to fit some other shocks, spings and polybushes to one of my 7s - to the rear end.
Anyway, as I was taking bits off I kept painting them, and decided that the rear axle looked scruffy, so I would change that too whilst I was on, and give the replacement one a lick of paint. Well, once I'd started, I thought I might as well change the rear axle seals (prevention rather than cure), along with the wheel bearings.
So as it's a topic that gets discussed from time to time on here I thought I'd take few snaps of the process for anyone who's thinking of doing it in the future.
Here goes......
Drain diff oil.
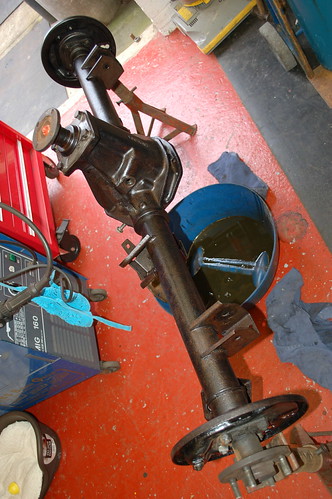
Undo the four 10mm set screws holding the half shaf into the axle casing.
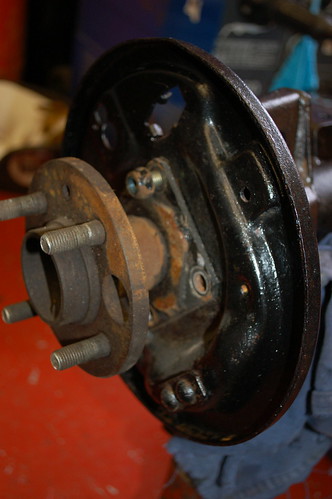
Now withdraw the halfshaft. There's a couple of was to do this. You could reverse the drum and hold it on with the wheel nuts and bash it out with a hammer, or bolt the wheel on and tug at it until it comes out.
I didin't want to do it this way (much easier to use either of these methods with the axle still in the car) as I like making stuff to help me do jobs, so I would make an adapter to fit onto my slide hammer. I decided to use an old halfshaft to save a bit of time.
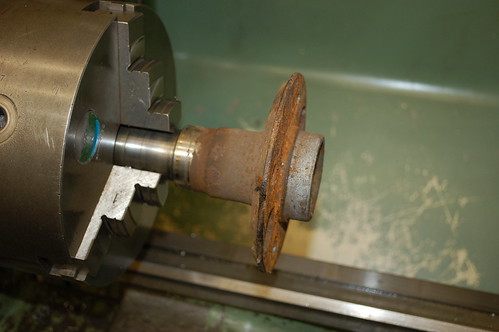
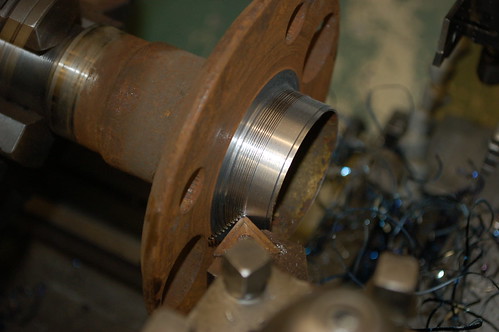
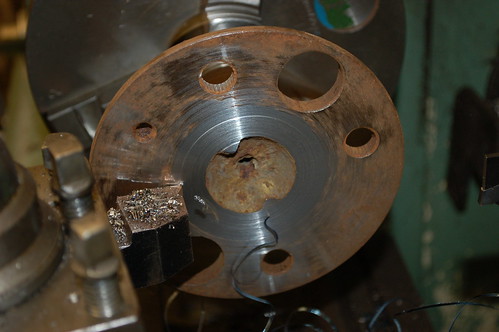
Once faced drill tapping size for my slide hammer - which is 5/8" UNF
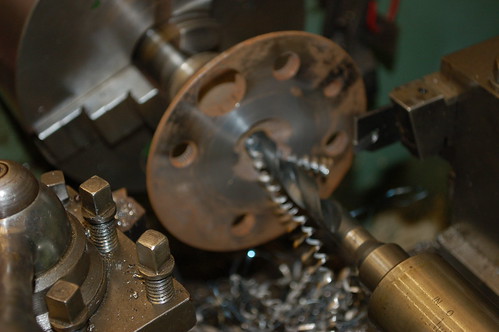
Then counter bore to locate square on end of shaft to be pulled.
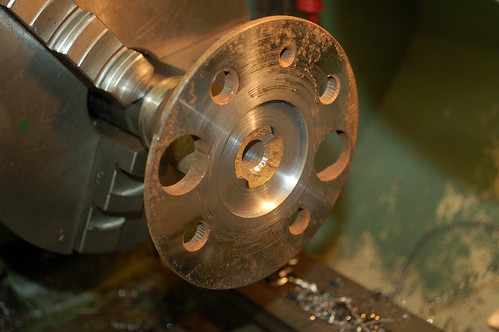
Part off
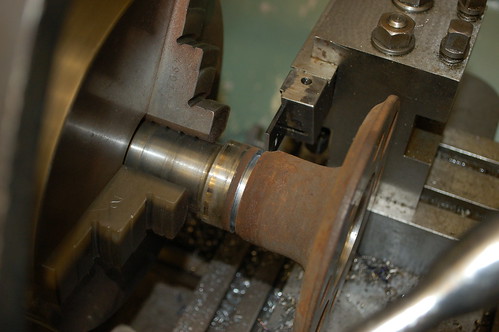
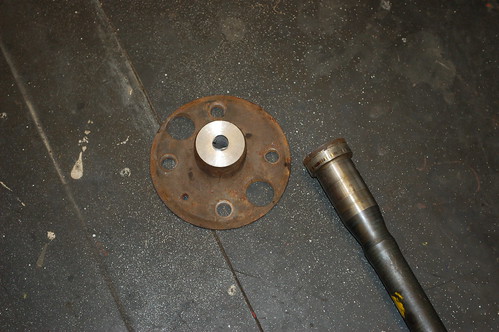
Tap out centre hole and then drill out stud holes for wheel nuts.
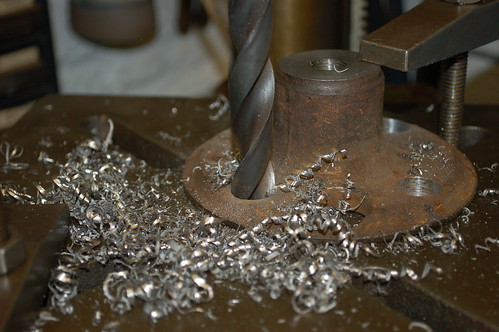
Bolt onto end of shaft to be pulled.
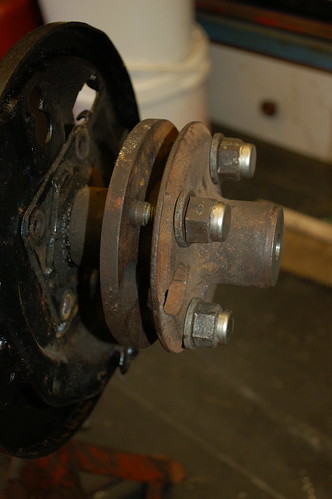
Attach slide hammer.
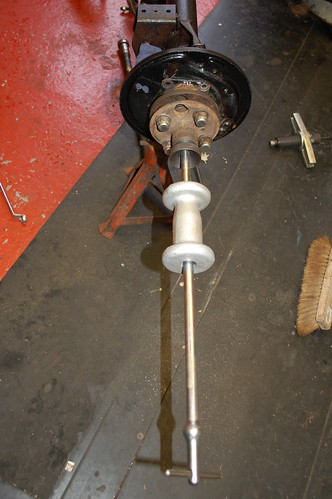
And out it comes - nice and squarely.
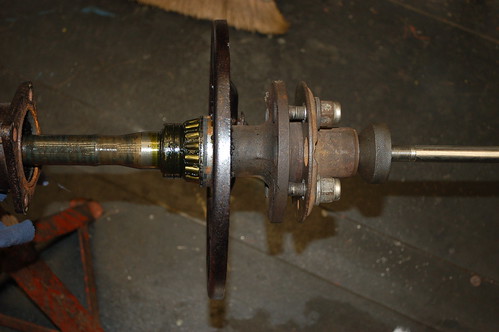
Hold shaft in vice.
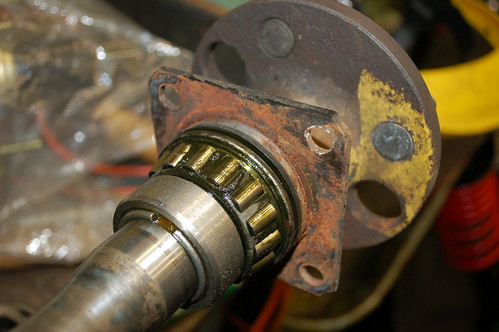
Remove circlip (circlip pliers).
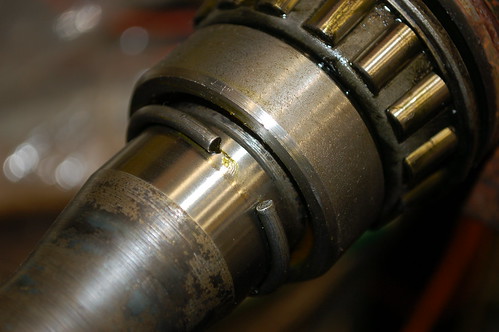
Drill hole in retaining collar to weaken.
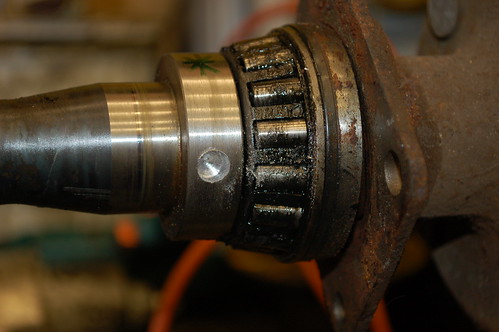
Support the collar (I used an old V block) and with a couple of hammer blows the chisel will split the collar. Which is then loose.
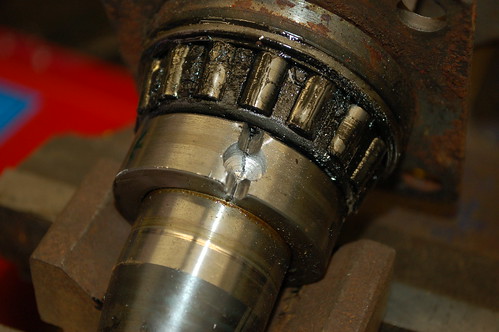
Attach puller. If you don't have the cast bearing puller, you can make a strongback out of a piece of heavyish plate and attach the screwed rod to that. Equally if you don't have a hydraulic puller a piece of bar with a HT bolt to locate onto the end of the shaft has the same effect.
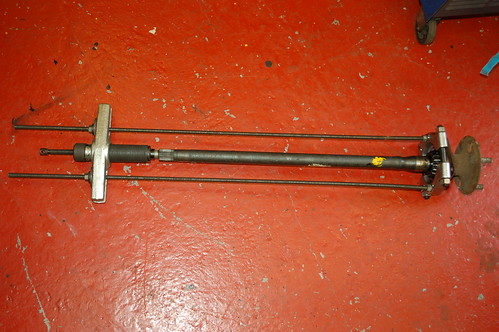
The bearing will be tight, so a fair amount of pressure is required. It will move with an initial crack!
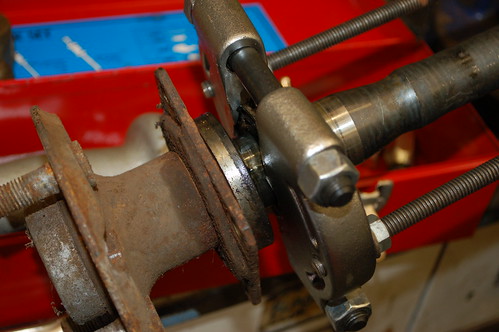
Remove seal and retainer plate.
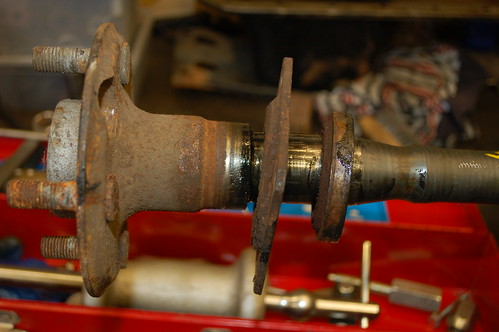
Clean shaft.
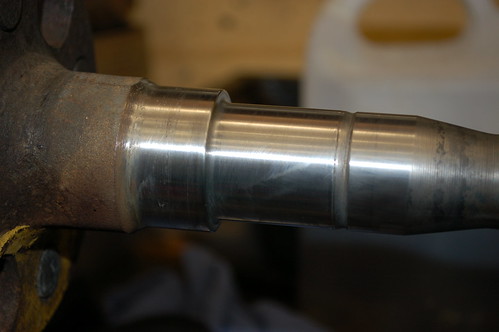
Remove outer race from axle. You don't need the slide hammer here, it just makes life easier.
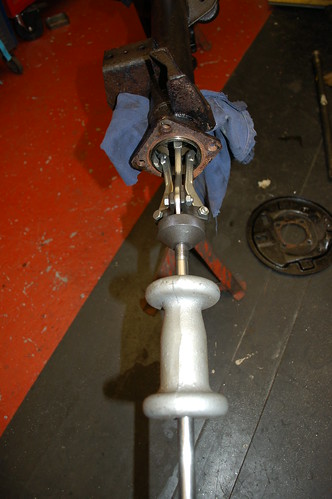
Then the inner seal.
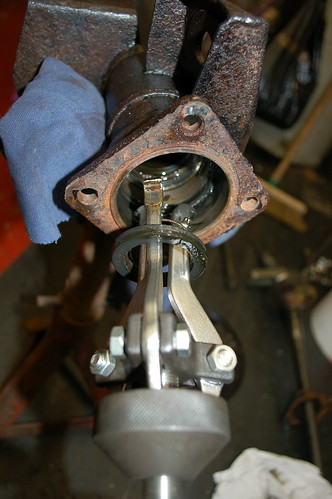
Replace inner seal - use large socket or similar to fit squarely. All pressure to the outer edge of the seal.
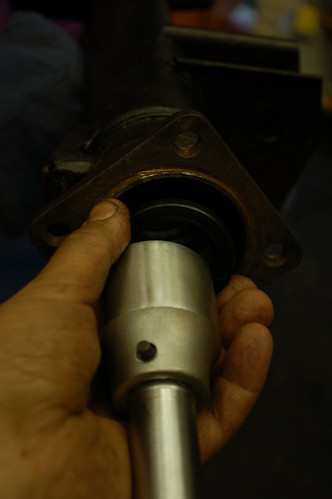
And outer race - this slides in freely by hand.
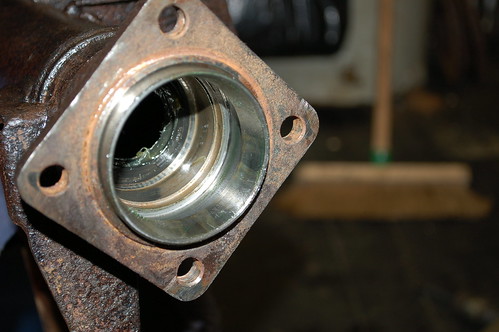
To press the new bearing onto the shaft I used the split collar and machined the end to fit into a length of steel pipe I use for this type of thing.
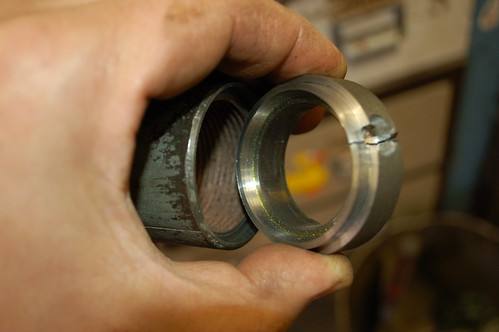
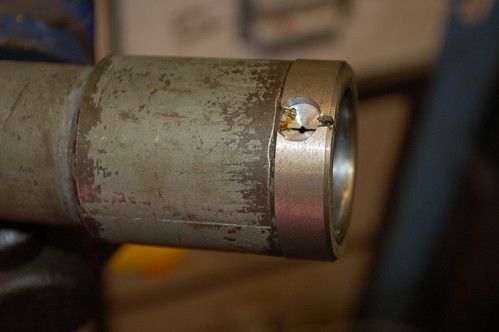
Tool ready
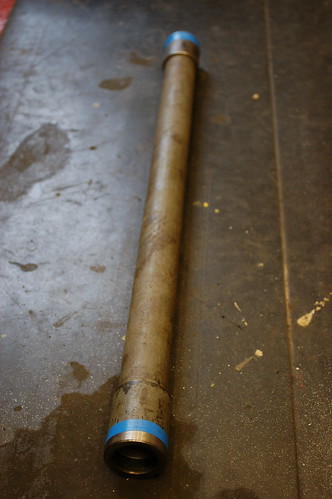
Oh - bit out of sequence here, but I drilled and tapped a hole in the casing to accept a grease nipple.
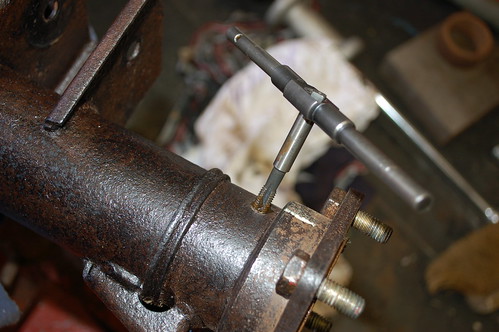
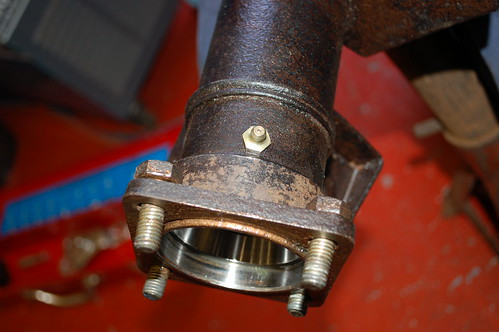
Now, there's only a thou or so interference between the bearing and the shaft, but about 6 thou on the collar. So I decided to chill the shaft and heat the bearing and collar.

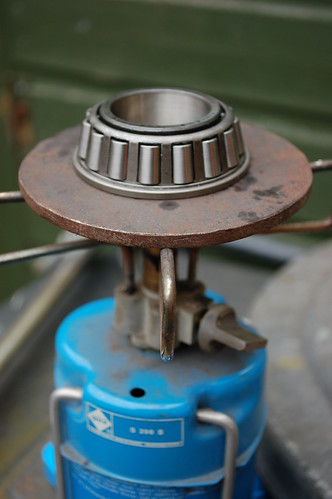
Bearing fell on. No need for the basher on tool - but used it just to check the bearing was home.
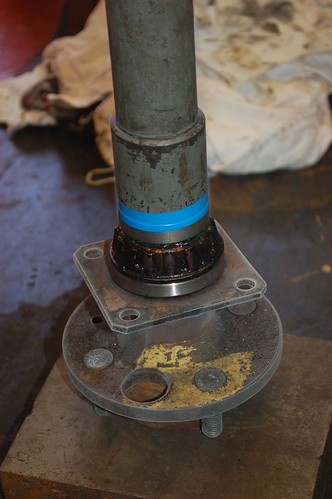
Bytheway - if you are going to press or bash either of these on make sure you support the shaft on the centre and not on it's studs. I used a pipe collar to support the shaft, and placed that on a steel block.

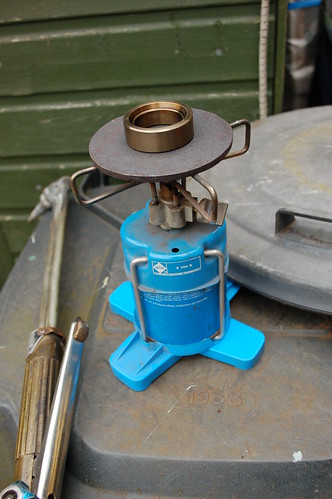
Collar also went on very easy - again tool not necessary really.
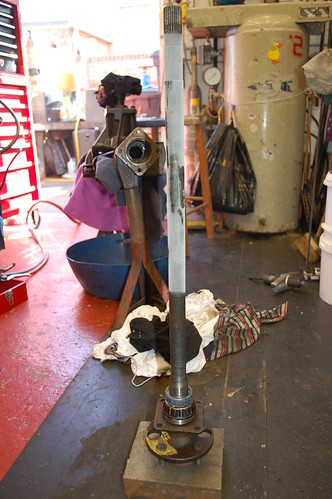
Tool was really useful for pushing the circlip on though.
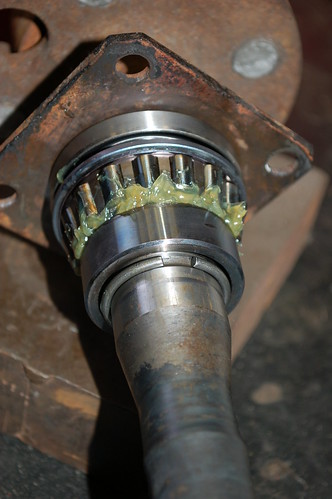
When I did the other side, I didn't bother chilling the shaft, and just warmed the bearing and collar - again they fell on really easily.
It's then just a matter of putting the brake backplate back on (in the right place), entering the shaft and drawing itinto the casing gradually and squarely with the four set screws. I loctited these, and torqued up to 50Nm (from memory).
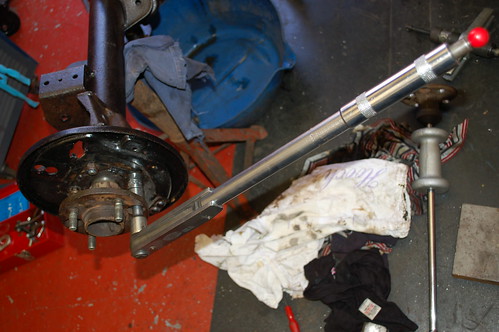
On this replacement axle I noticed one of the welds was leaking, so I ground that back and welded it up whilst I was on.
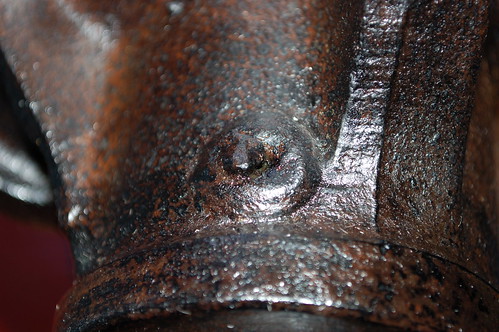
You can see the porosity in the weld clearer here once ground back.
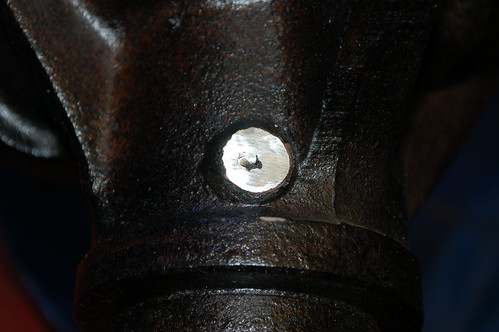
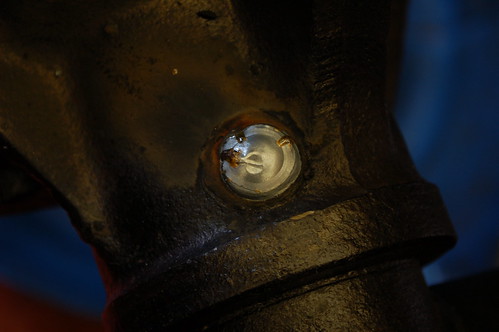
Cheers,
Shaun.
http://www.flickr.com/photos/12691409@N08/