Hiya.
I bought another Land Rover last summer. I got it for a good price, as it had a messy oil leak from the engine/gearbox area. It was hard to tell where exactly it was coming from, as there was oil all over the place.
Anyhow, I ran it for a while, but the dripping really started to get on my nerves, so I decided to take the engine out . . . .
Motor came out no problem (left the gearbox in the car). Cutting to the chase, there were a few oil leaks, but the main problem was that on this Land Rover reconditioned engine (only done 15K ish), the rear crankshaft oil seal had been put in the wrong way round! Shocking. I had the sump, ladder, oil pump and front case all off. New gaskets and seals, timing belt etc.
So the engine was all washed off, and nice and clean – but the gearbox looked filthy. So I decided to drop the box out too, and give it a good clean. Bloody awkward thing to remove due to the very unbalanced nature of it.
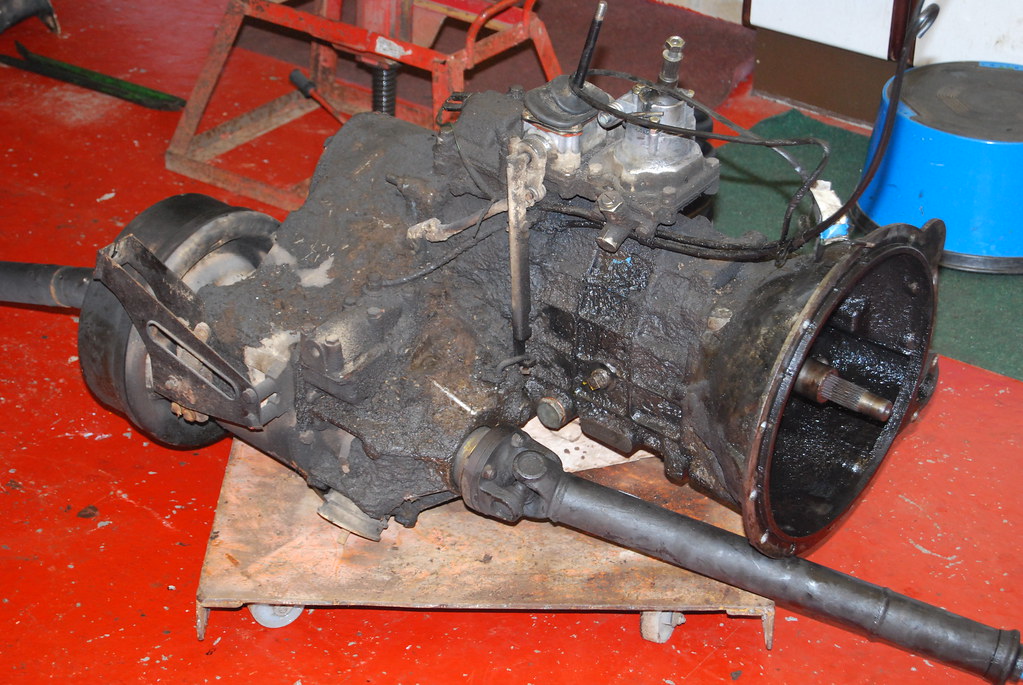
I spent the best part of a day cleaning the gearbox and transfer box off – but the results were worth it.
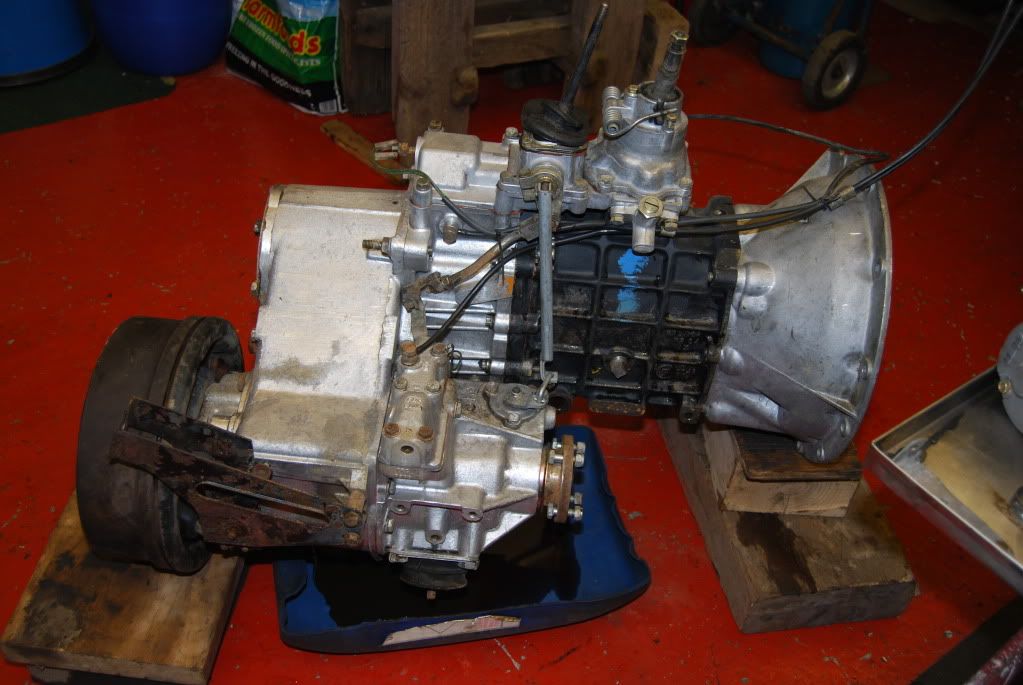
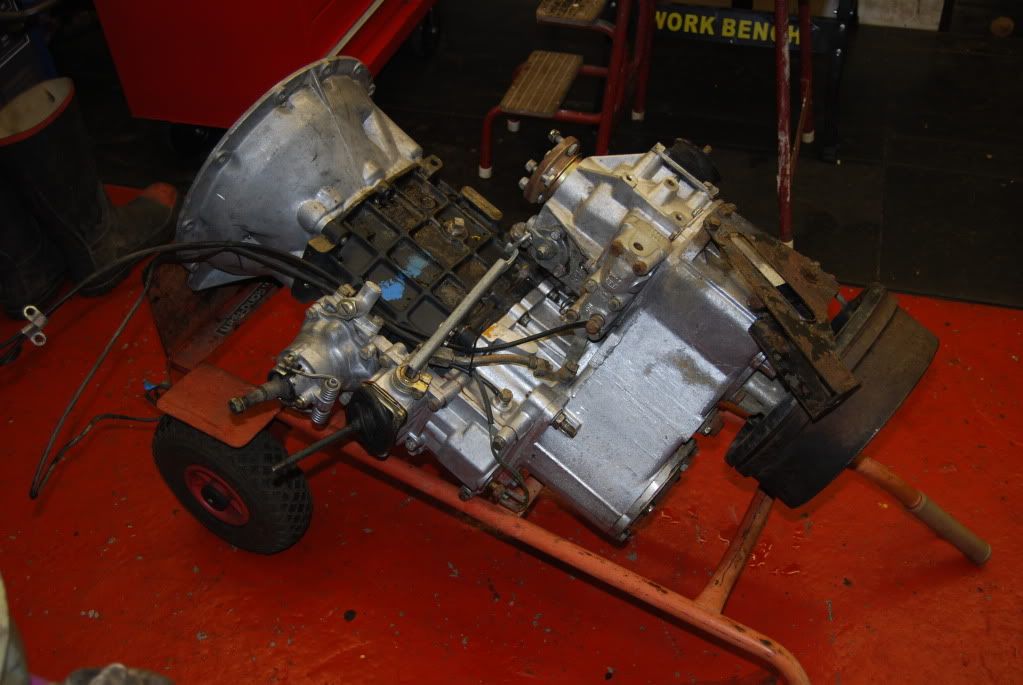
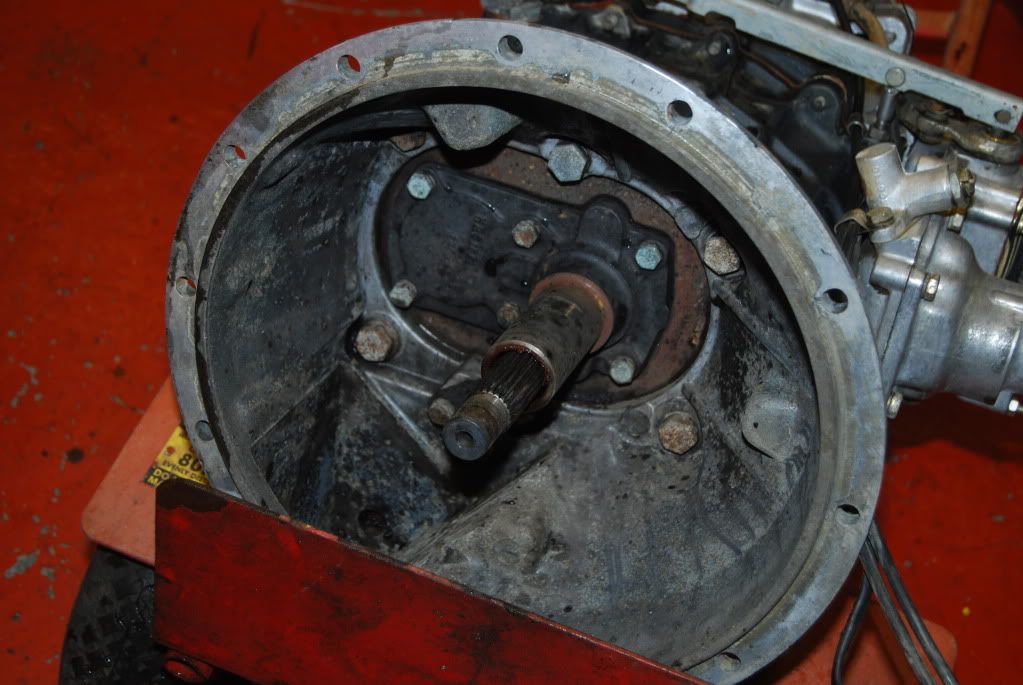
On inspection, I could see that there was a little oil leaking here and there. So I thought – “What the hell. I’ll split it and treat it to a few new oil seals and gaskets whilst I’ve got it out.†And boy, was I pleased that I decided to do this!
When I got the transfer box parted from the gearbox I found that the mainshaft splines were about worn through (ready to lose drive), and the transfer box input gear splines were also worn out. I’d have no sooner got this all back together, and the bloody thing would have sheared the final bits of the splines off, and left me with no drive. And of course, it would all have to come out again.
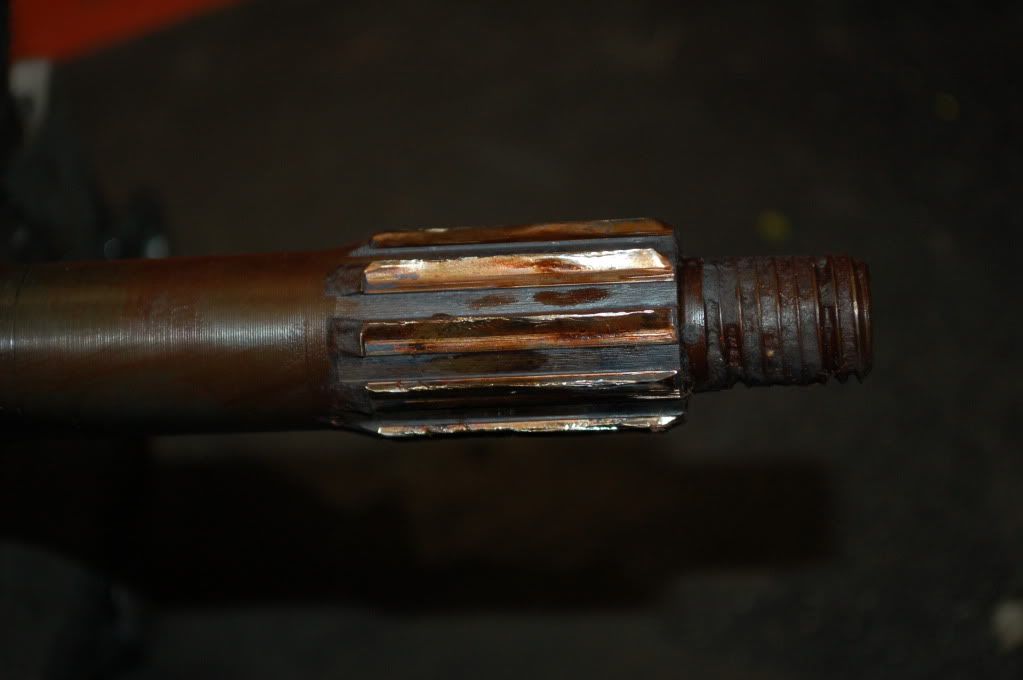
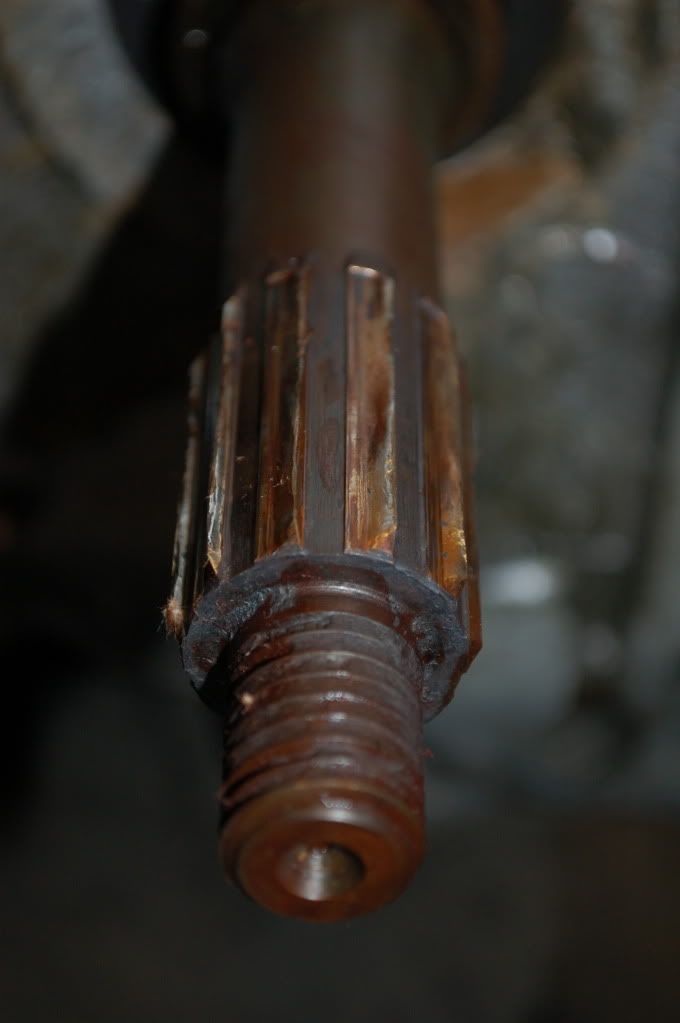
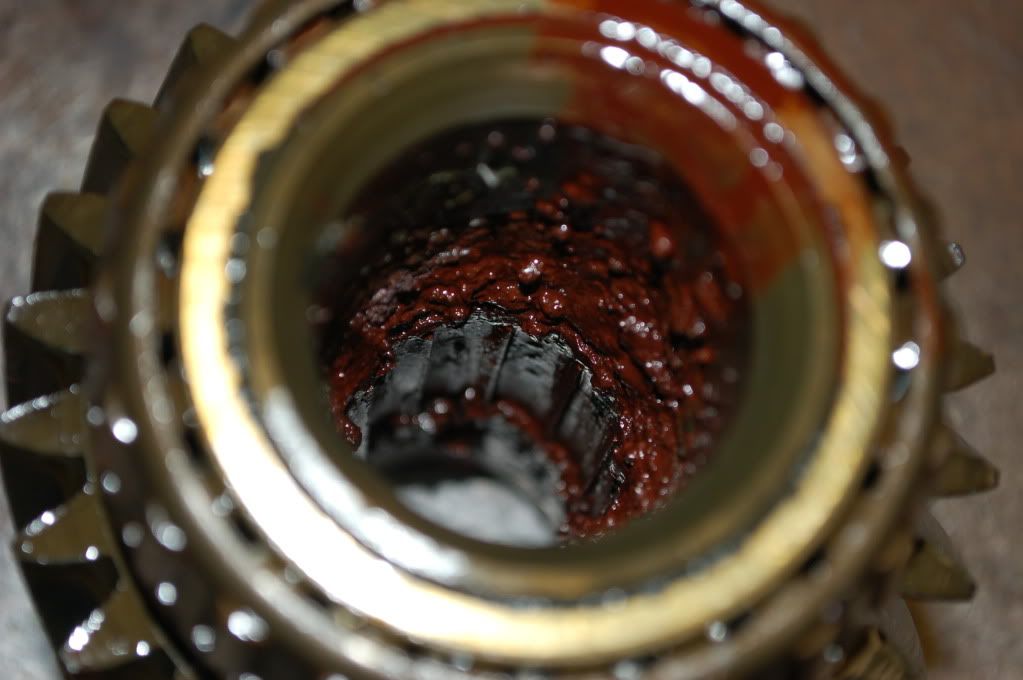
This was a known fault bytheway on Defenders/Discoverys of this age. The later input gears were modified with lubrication holes to stop the wear.
Essentially this gearbox is the same as found in our 5 speed TR7s – it’s an LT77. There are a few minor differences here and there – but not much. So I thought it would make an interesting topic.
Here goes…
As you can see, the selector housing is different to the TR7.
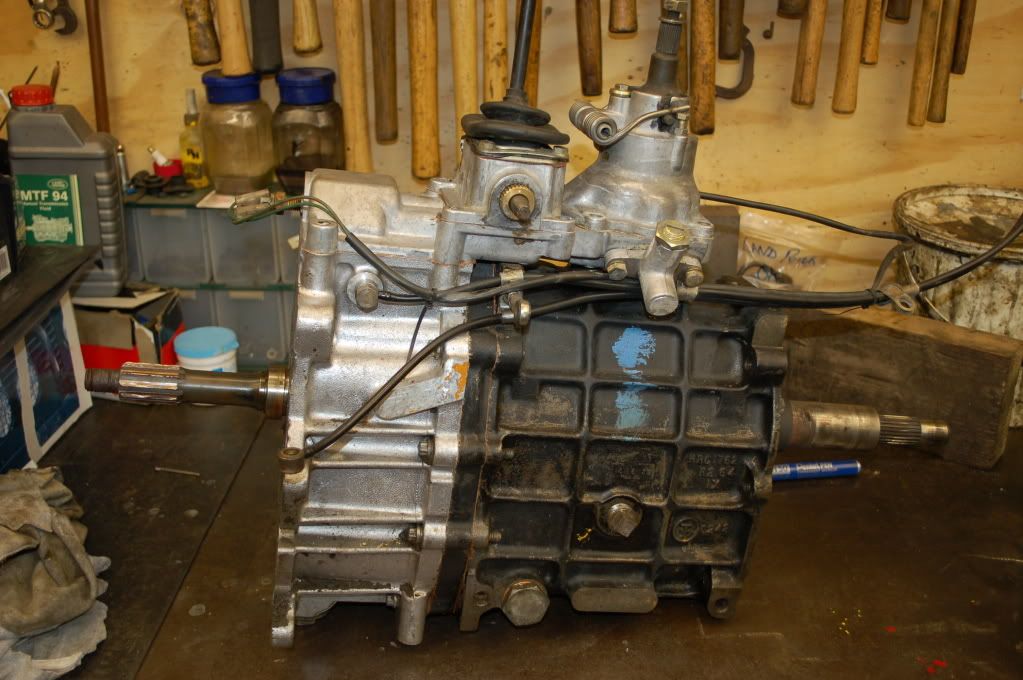
Remove it
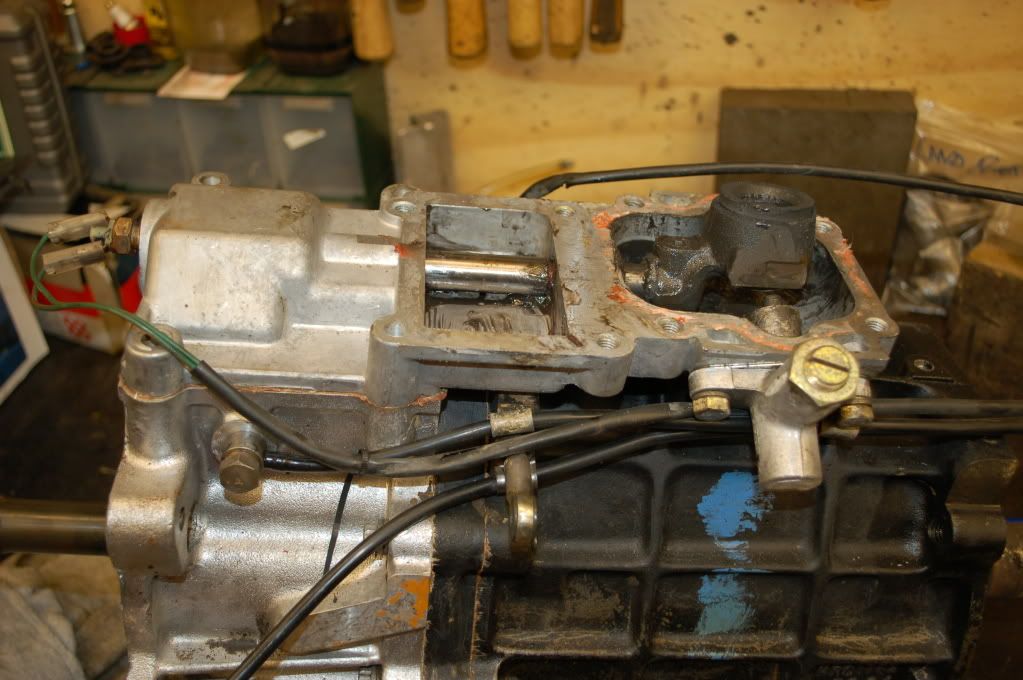
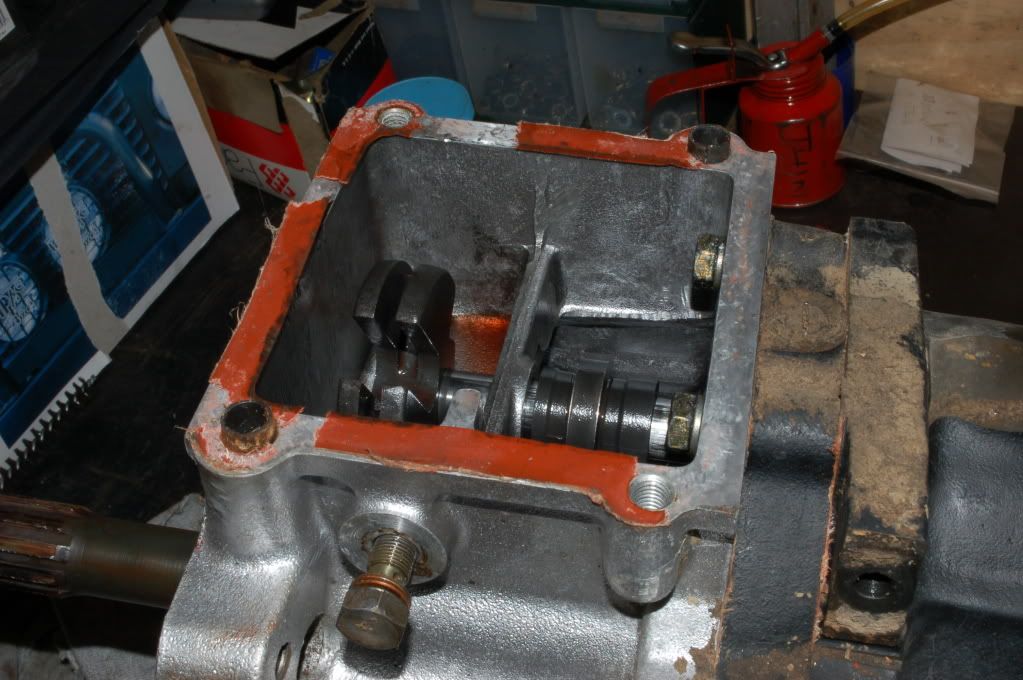
Again, not on TR7, but you have to do it! Remove snap ring.
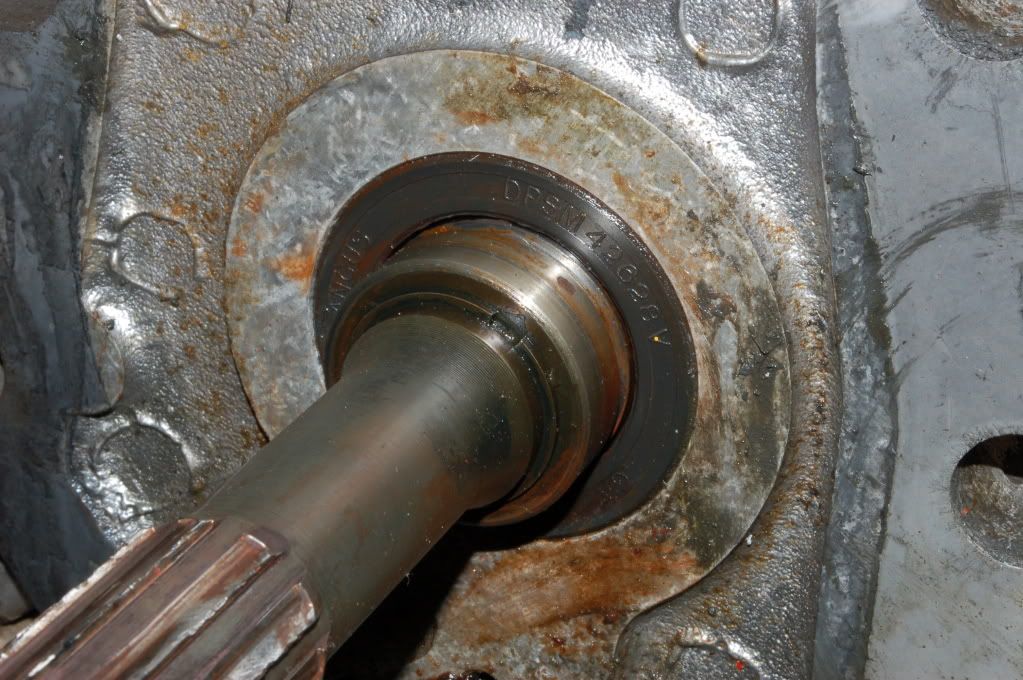
Remove oil seal collar. It has a groove machined in it to pick up on it for pulling – it’s tight!
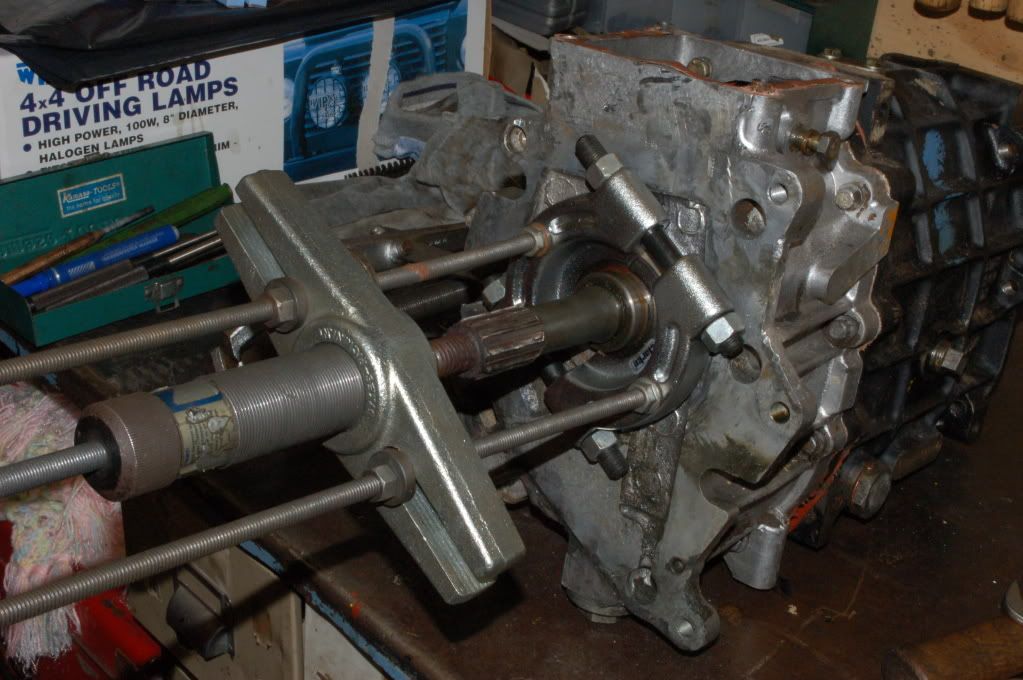
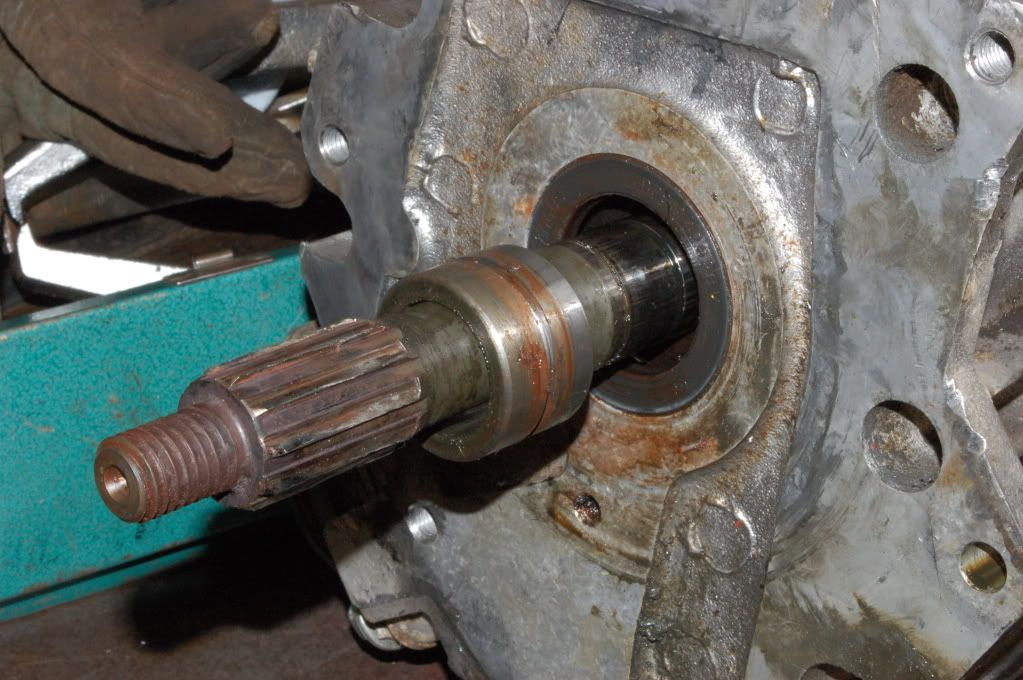
Remove bolts and slide off aluminium housing.
You can see the oil pump square drive in the end of the layshaft (2nd motion shaft).
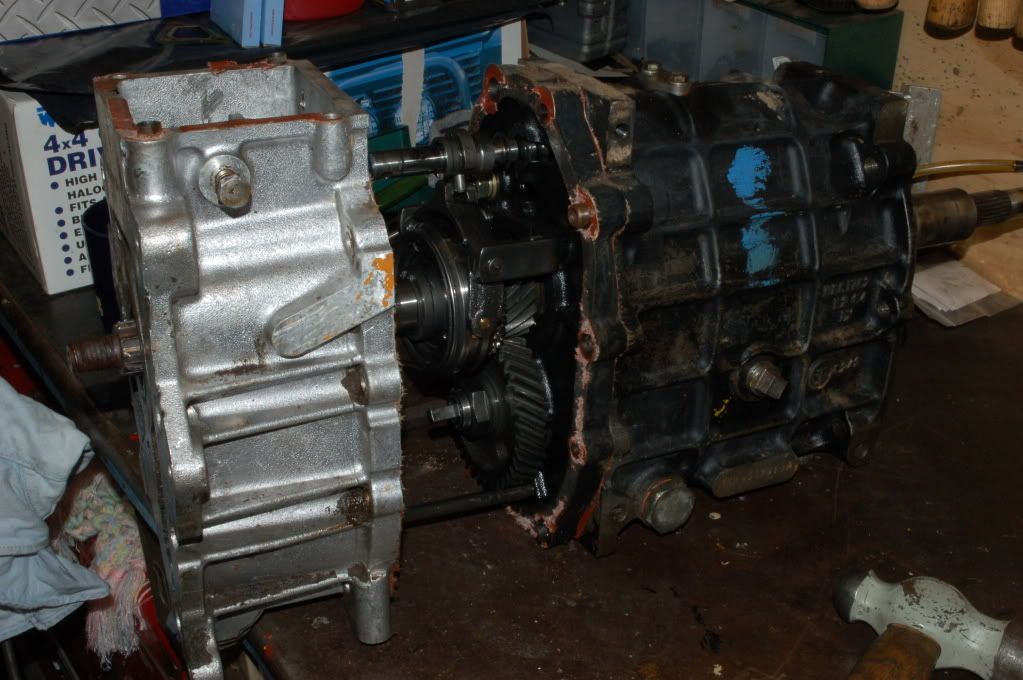
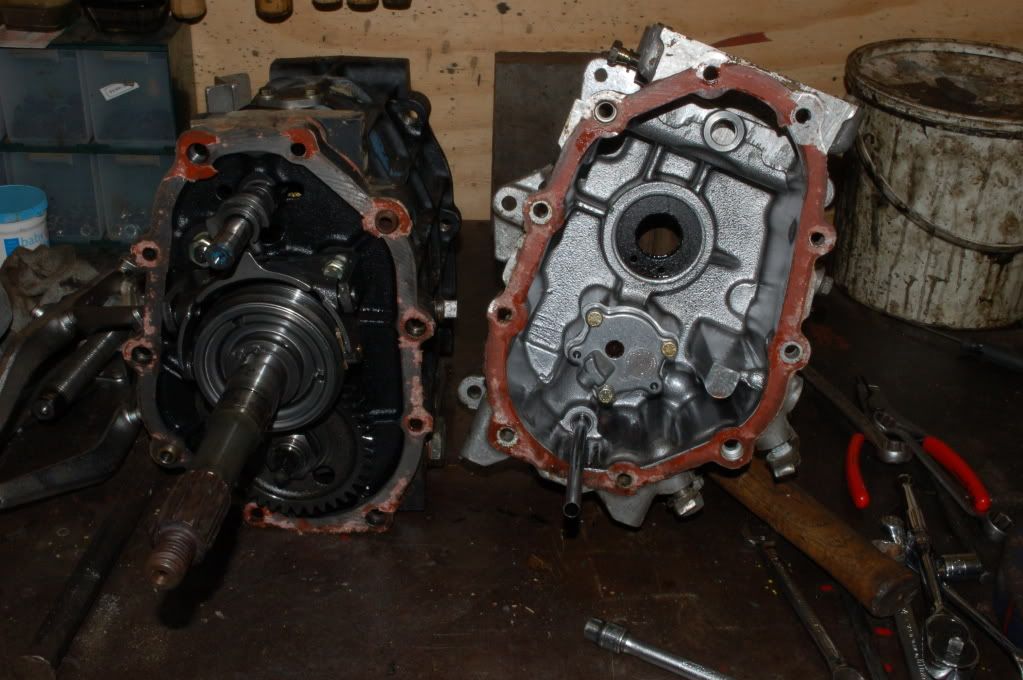
Remove oil pump gears – they were worn, but very good for 115,000mls. Much better than most TR7 gearboxes I’ve split.
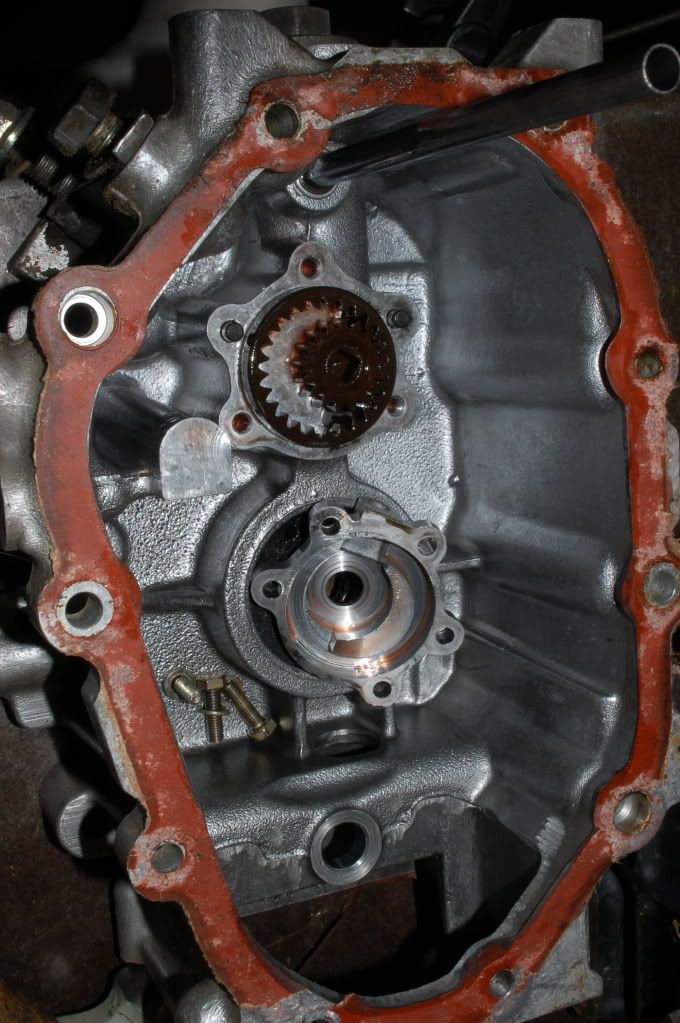
Upend the gearbox.
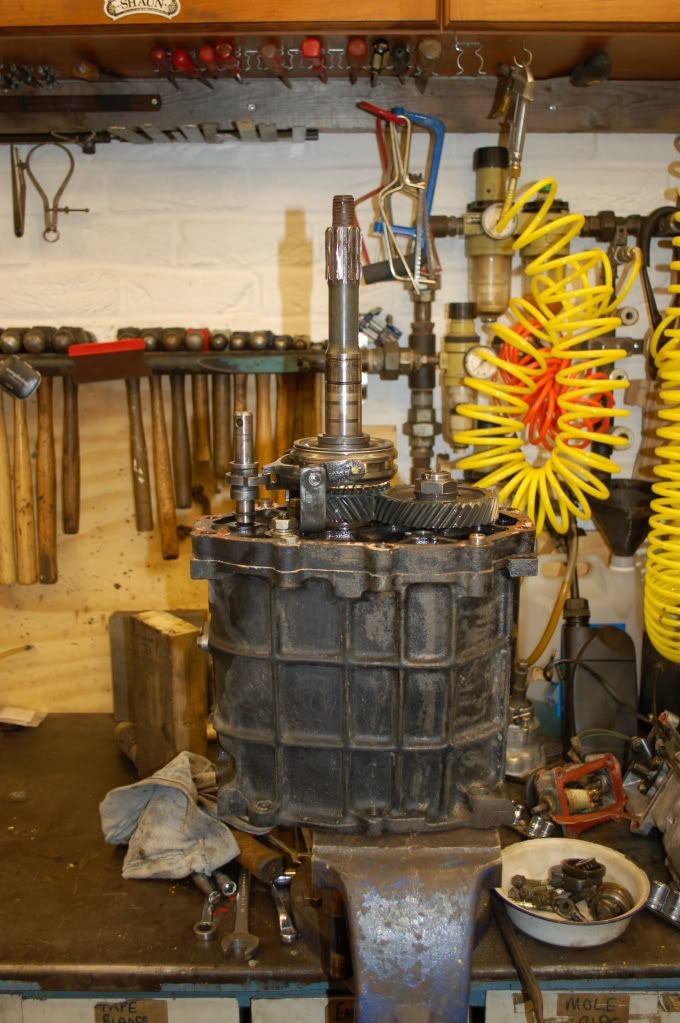
Picking up on one of the centre plate bolt holes, lock the 5th gear – I used a bit of scrap. As the nut is staked, it’s quite tight. This isn’t a nut on the TR7 box – it’s a press on collar that you have to pull off - if I remember correctly.
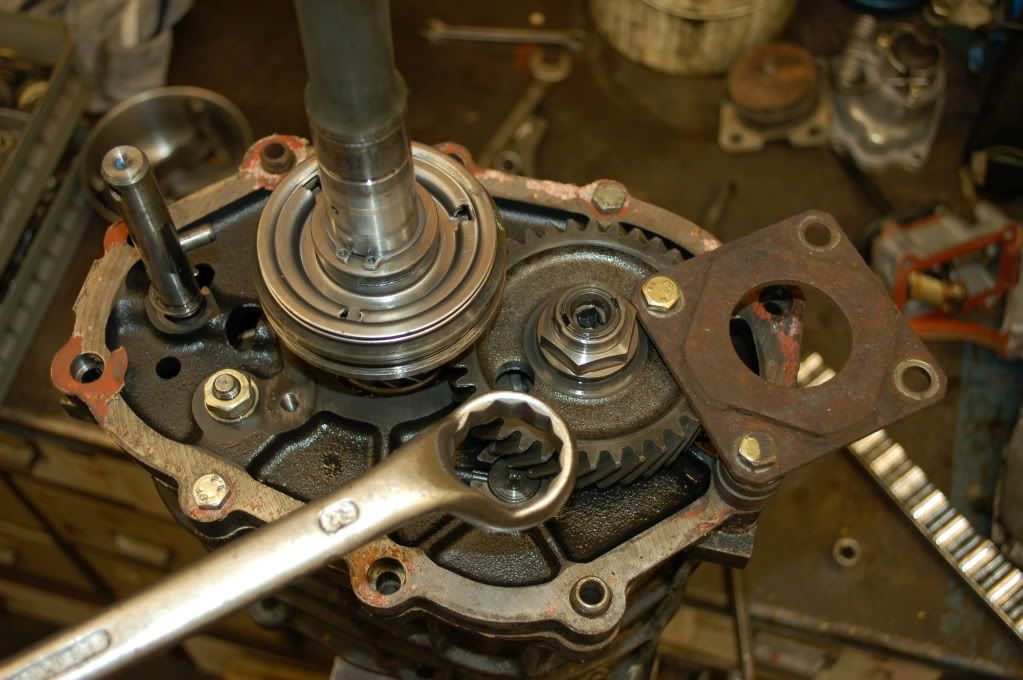
Remove selector and then 5th gear circlip.
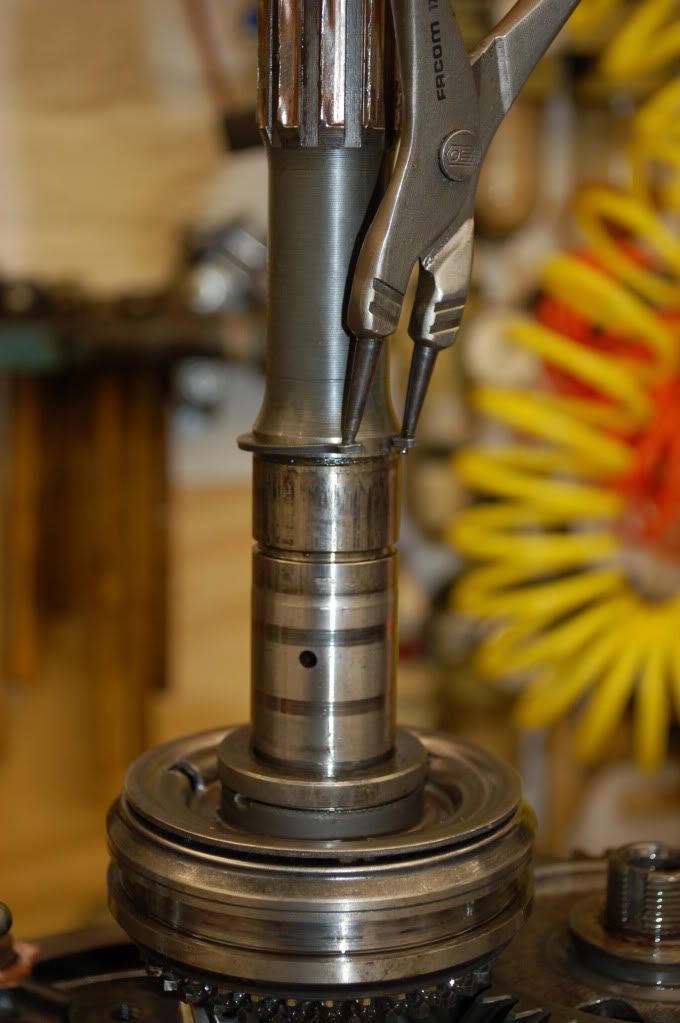
Remove selective spacer and 5th gear from mainshaft (3rd motion shaft).
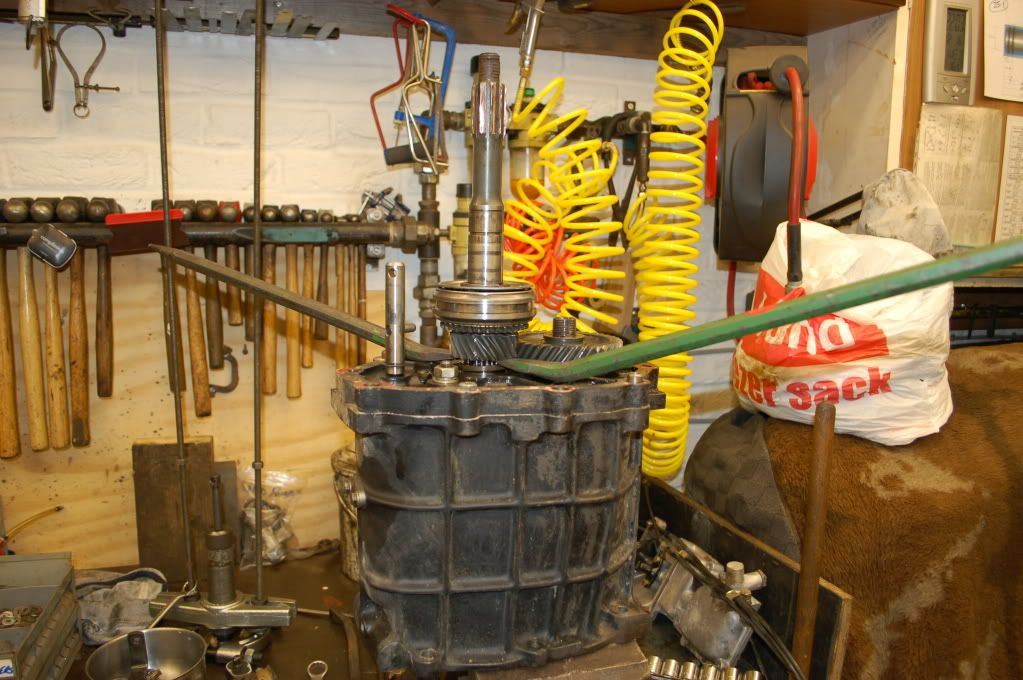
This is different to TR7 – 5th gear has a split caged bearing. Open up cage and remove.
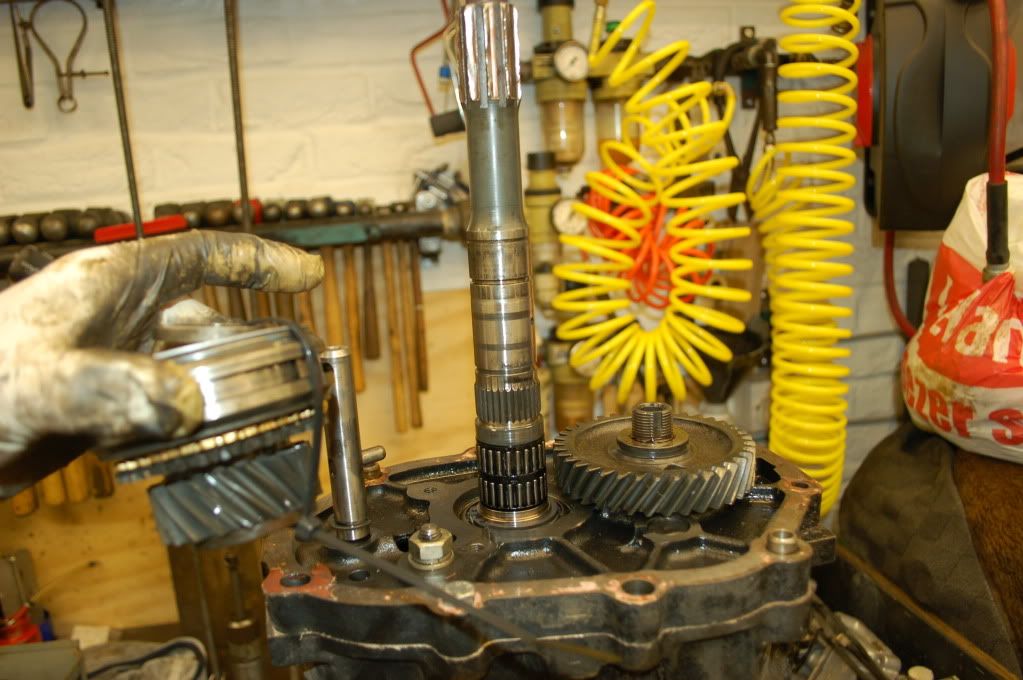
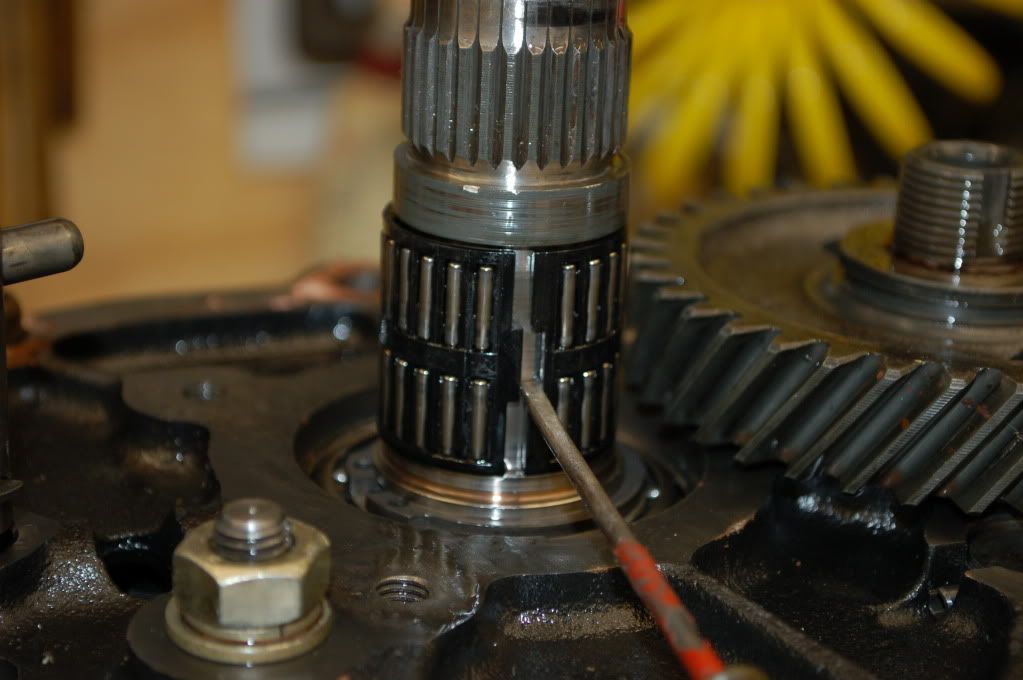
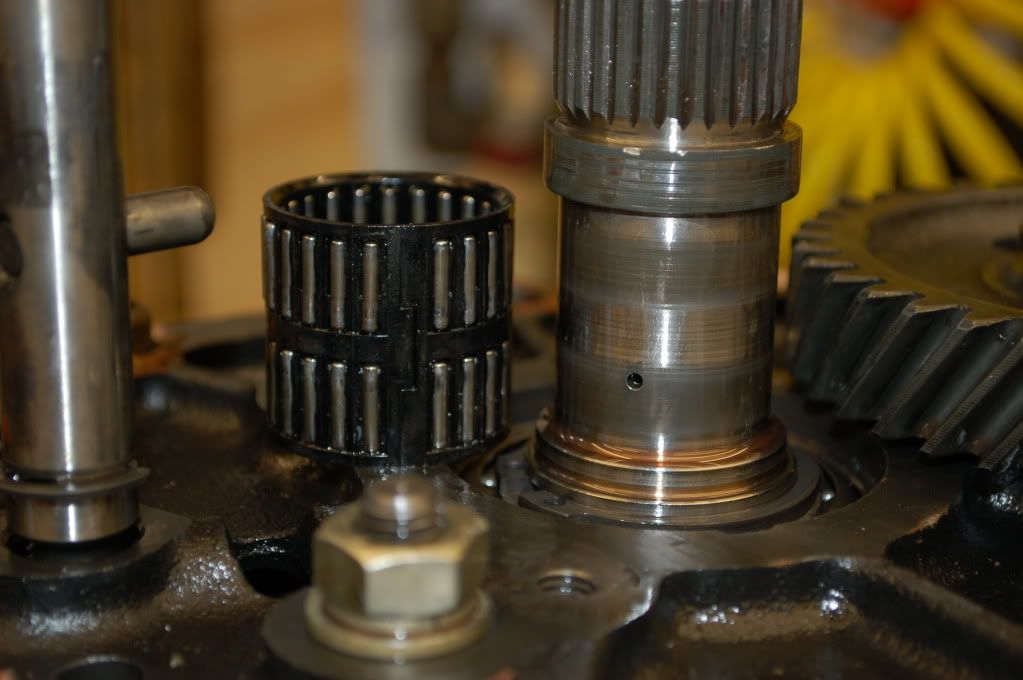
Lift off 5th gear from layshaft Can't remember if I needed a puller to do this. Or whether employed the two pry bars again - sorry, no photo.
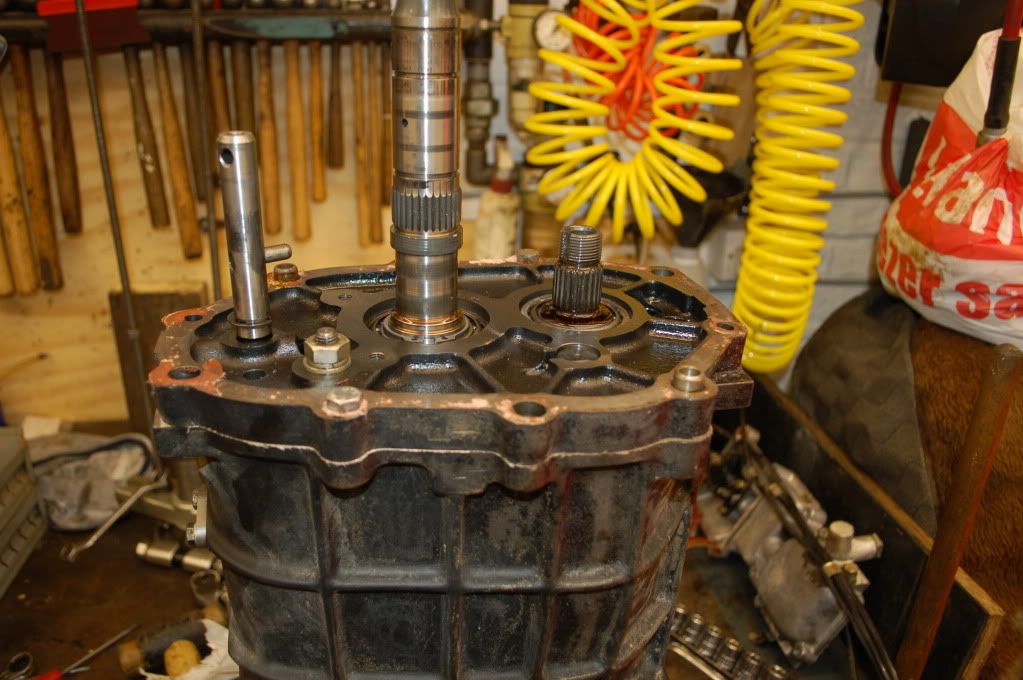
Invert casing and remove front cover, selective washers and gasket.
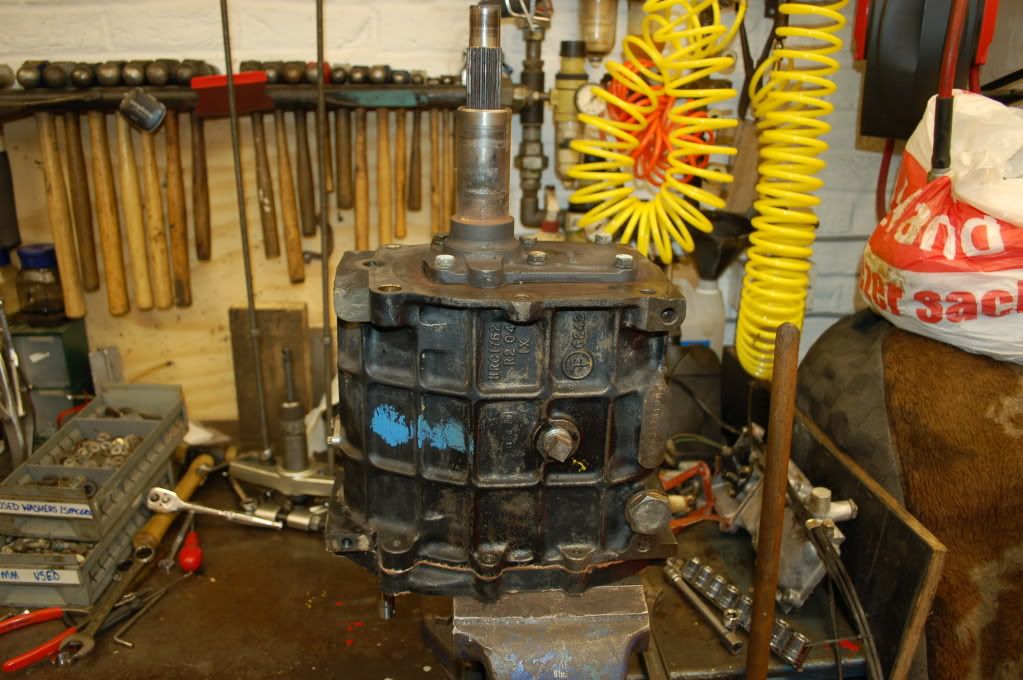
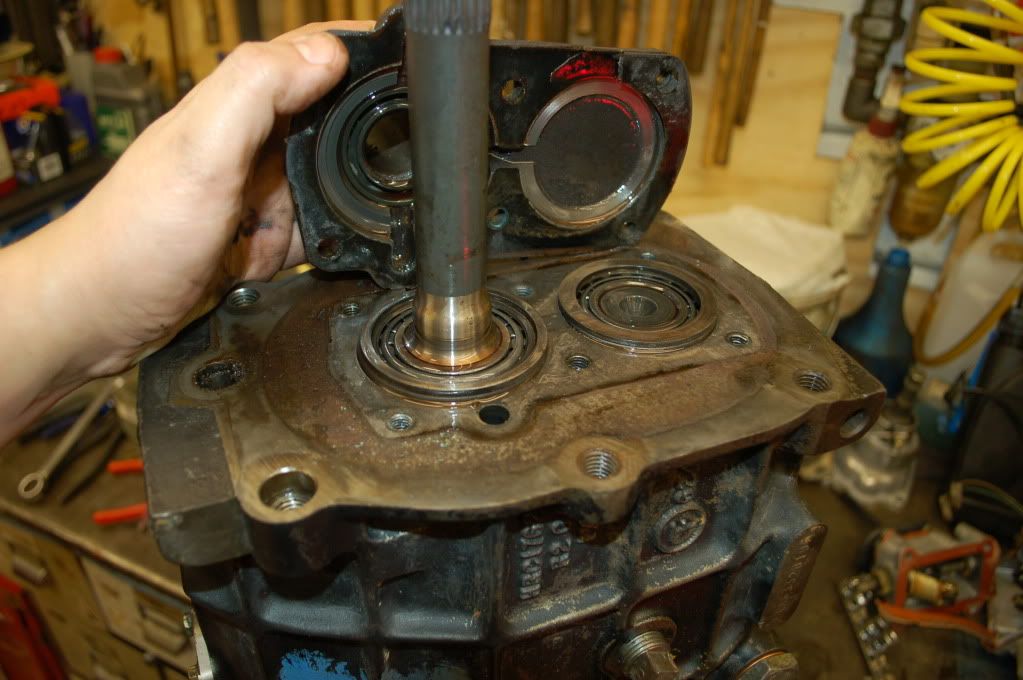
Remove selector shaft spool retainer.
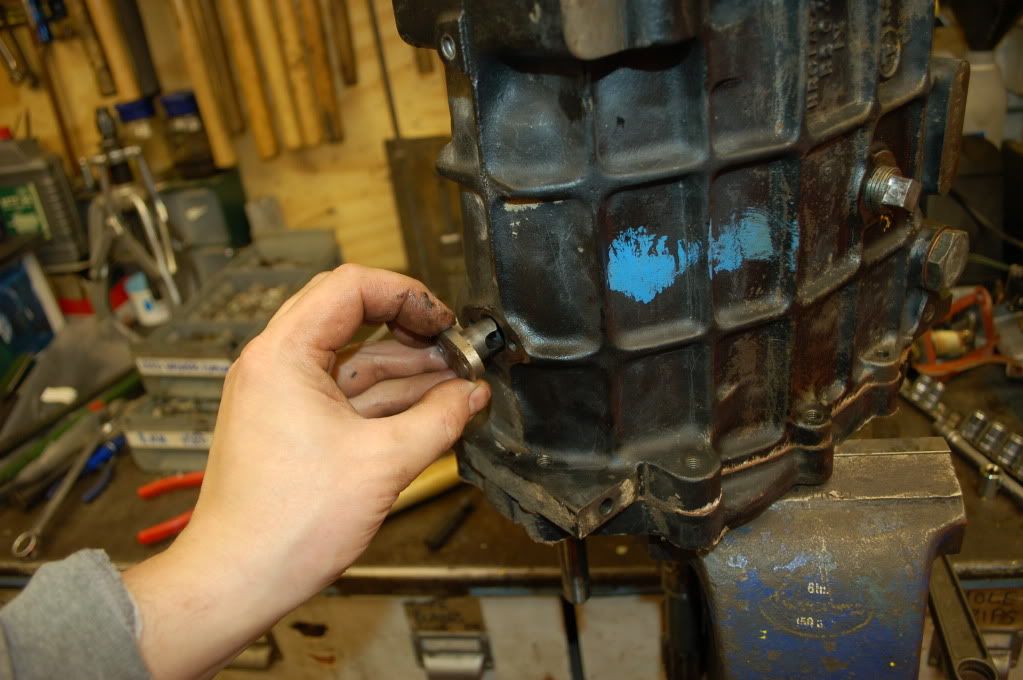
Lift off casing.
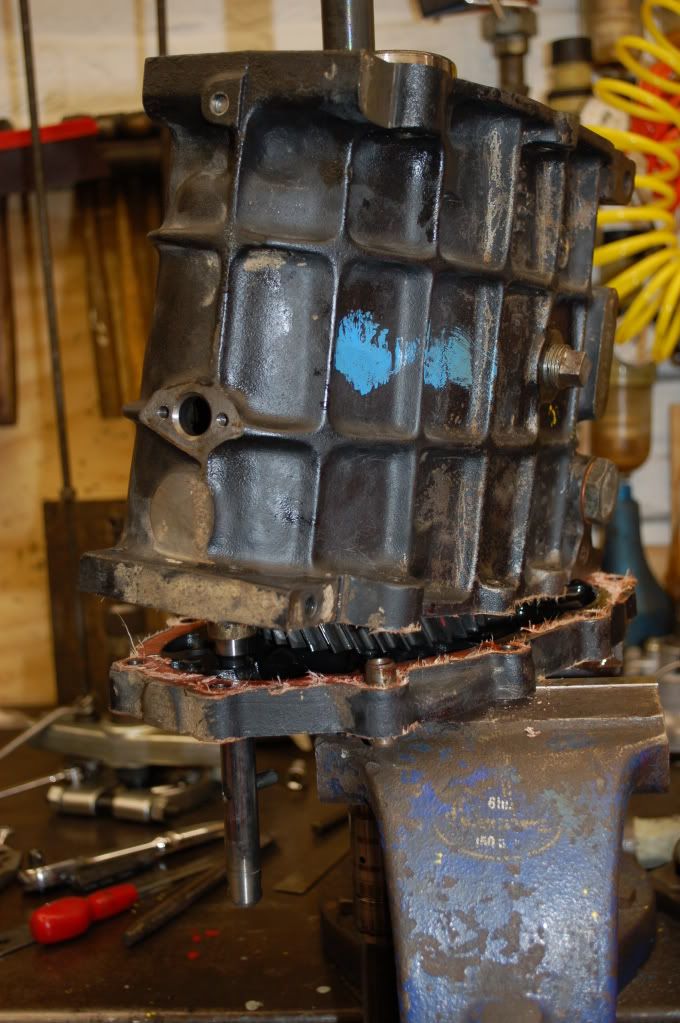
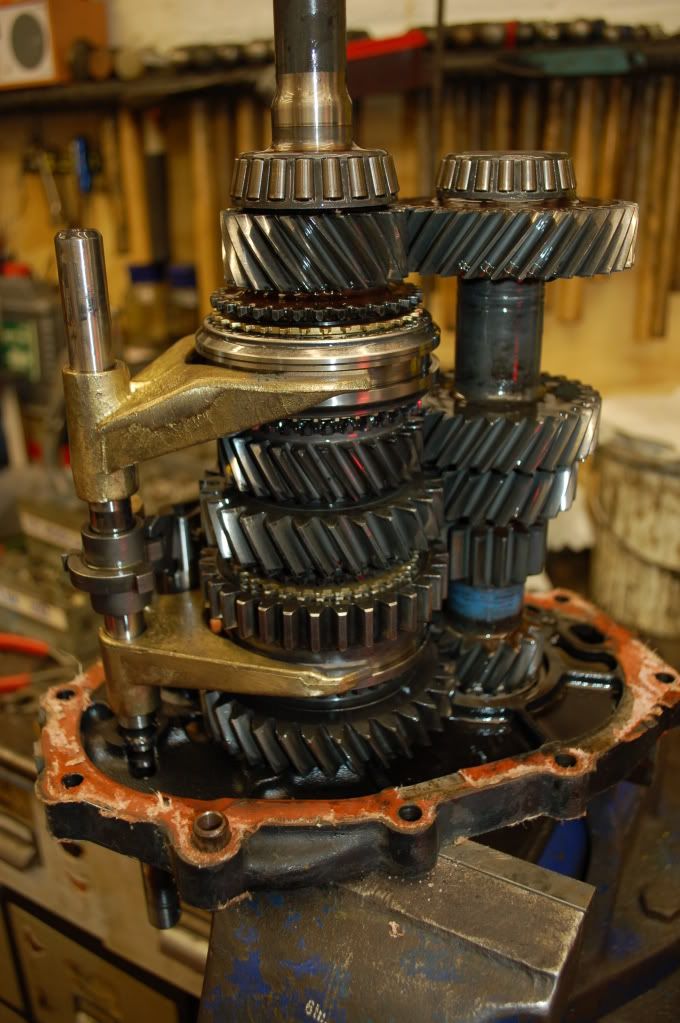
Remove reverse shaft, thrust washer, reverse gear and spacer. Reverse lever pin, lever and slipper pad.
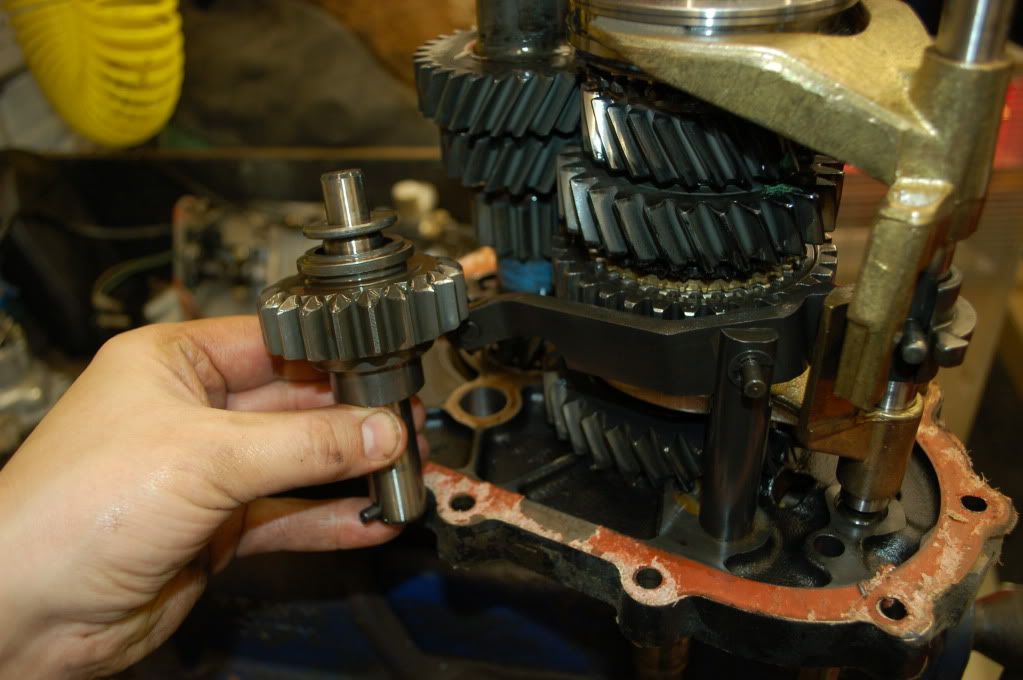
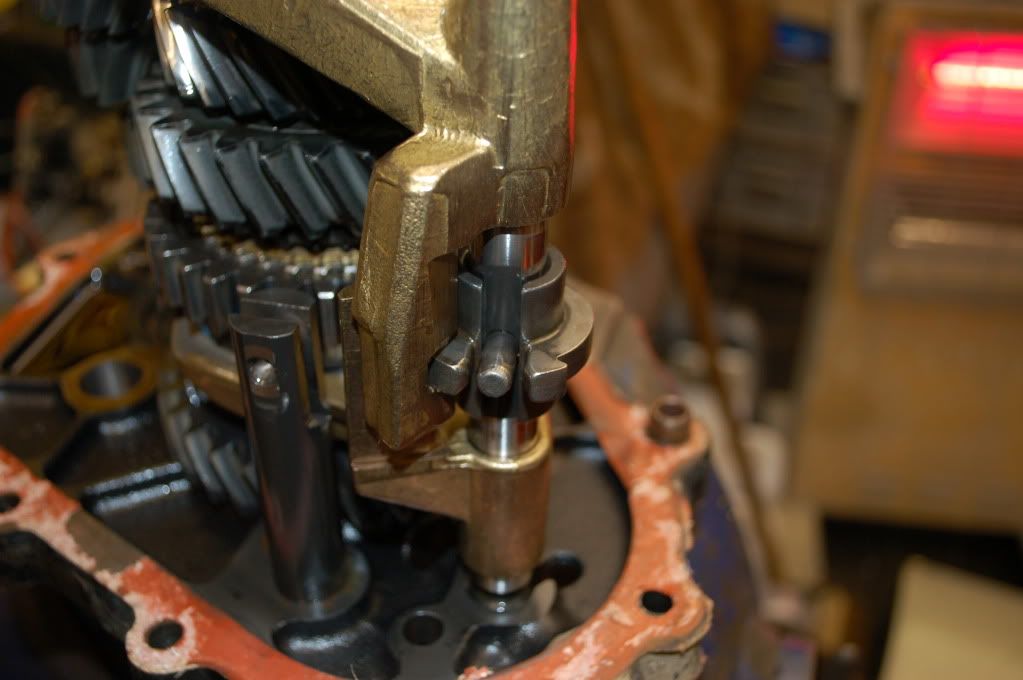
Lift off constant pinion shaft (1st motion shaft).
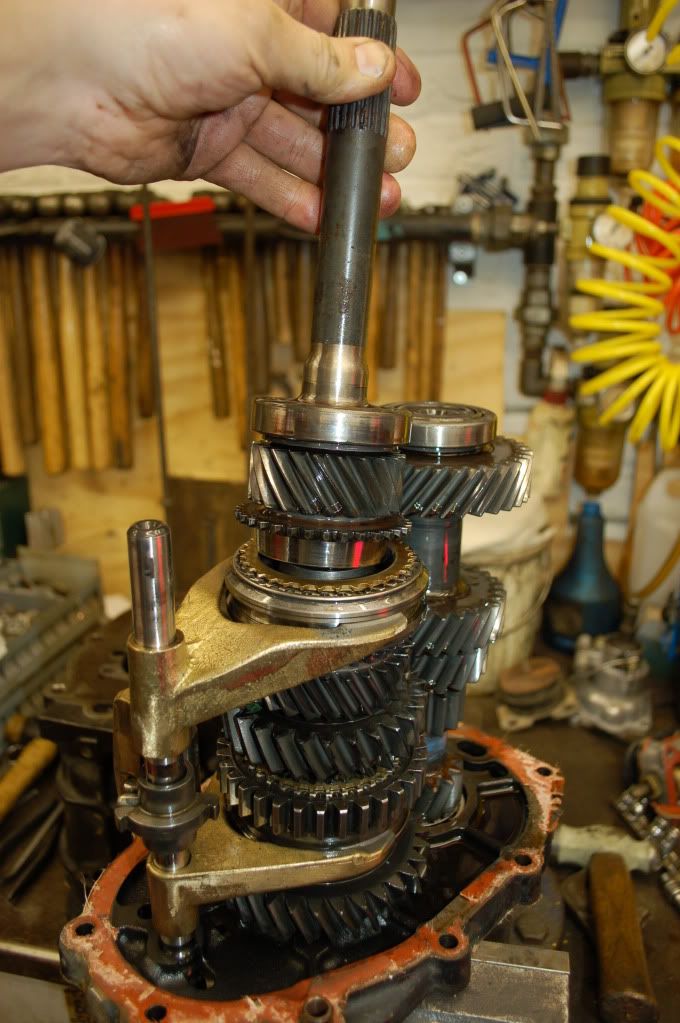
Remove layshaft.
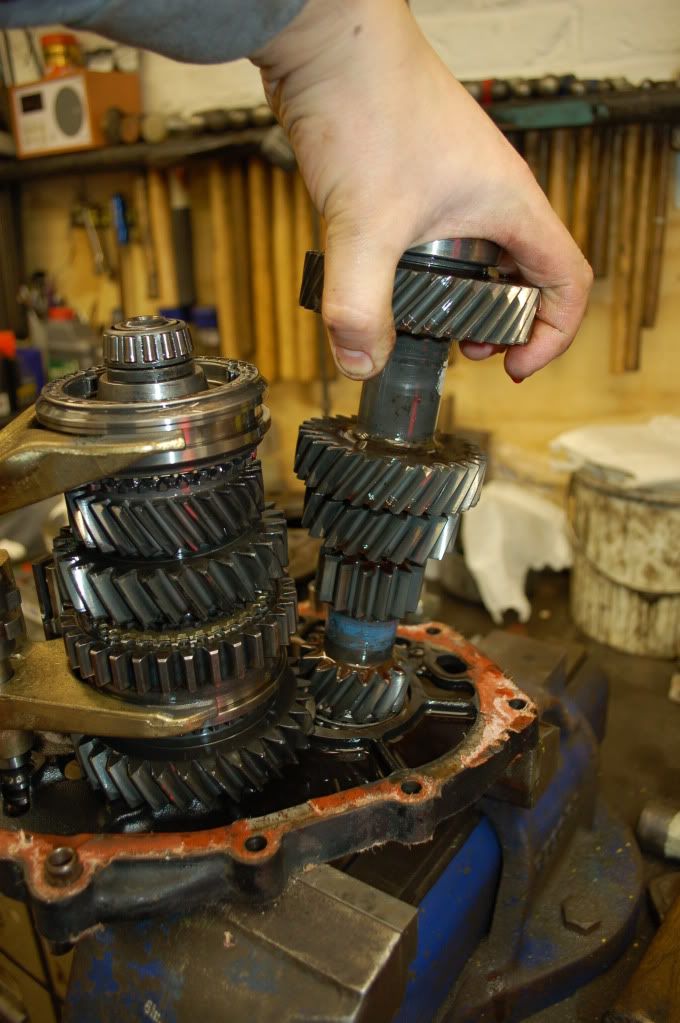
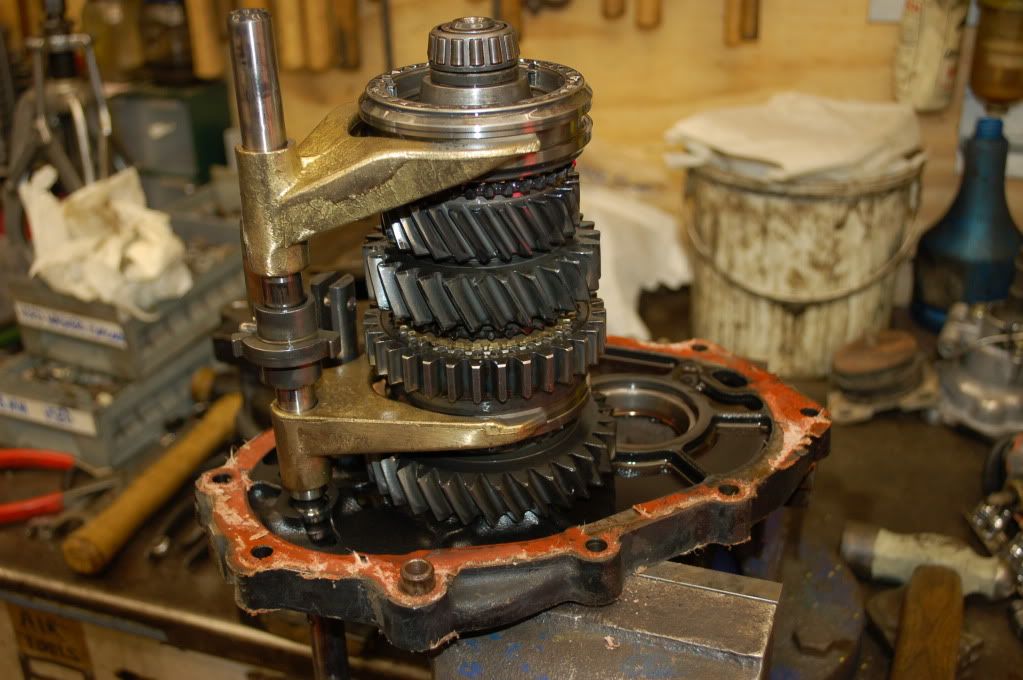
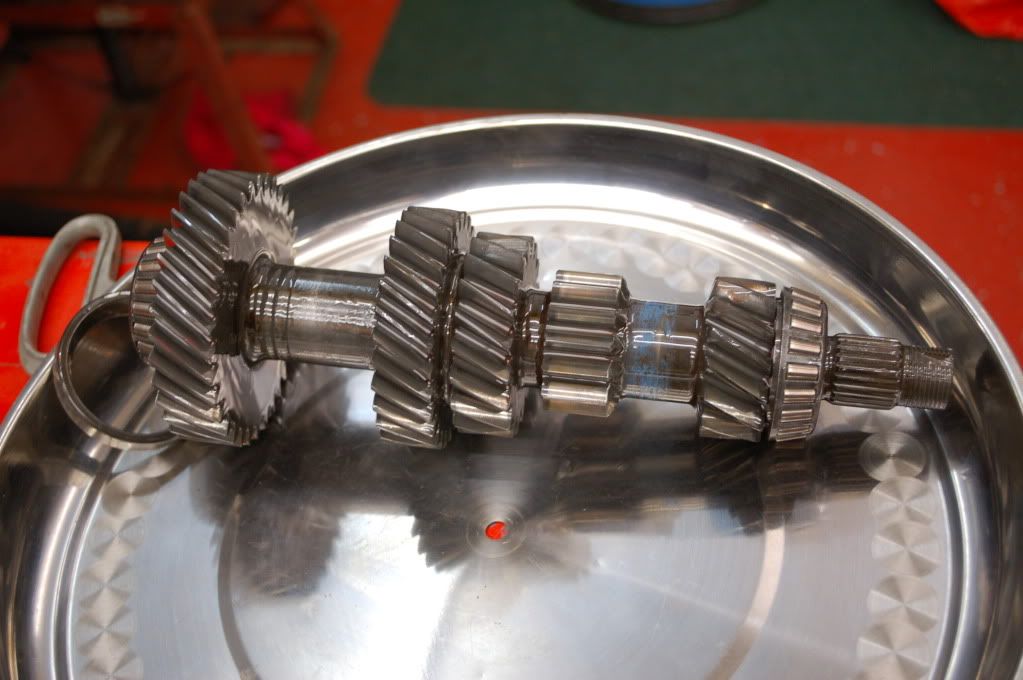

Unscrew plug and remove detent ball.
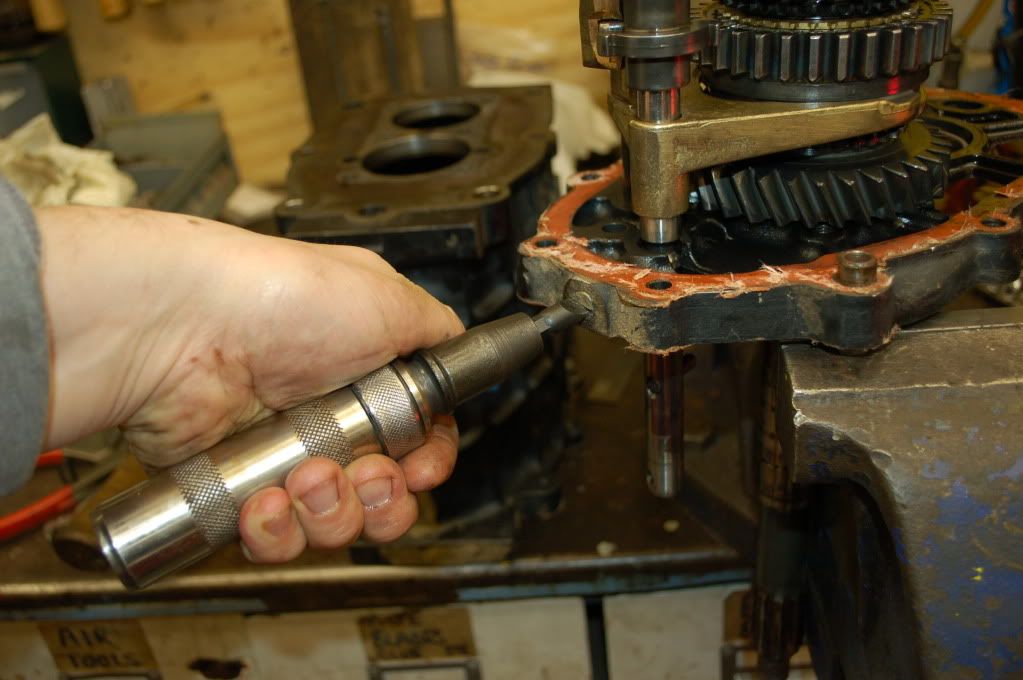
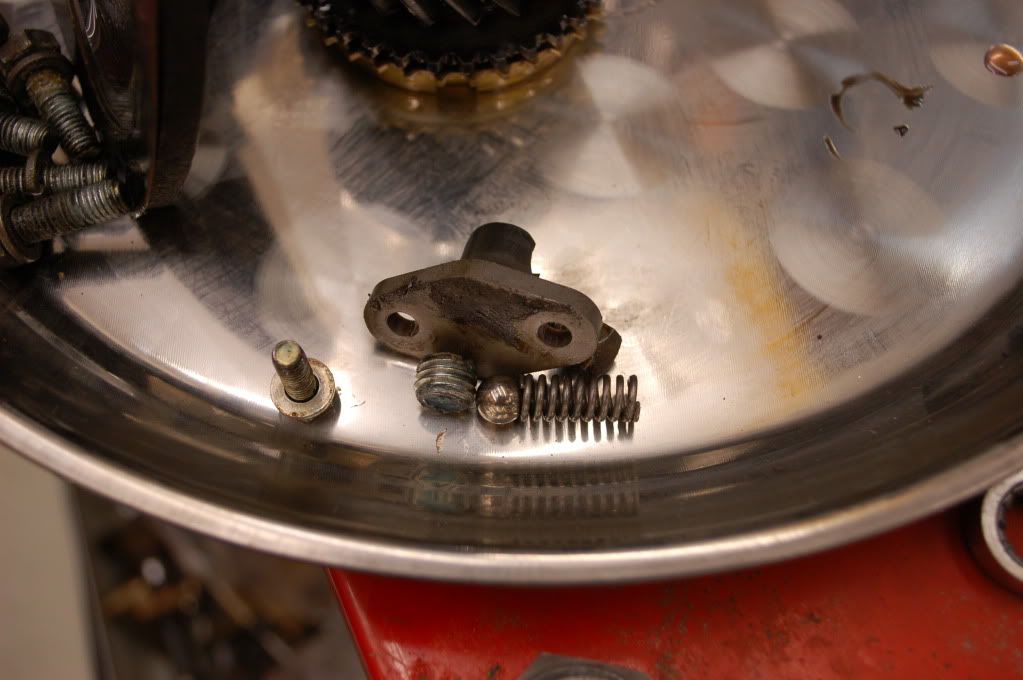
Remove mainshaft gear cluster complete with selectors.
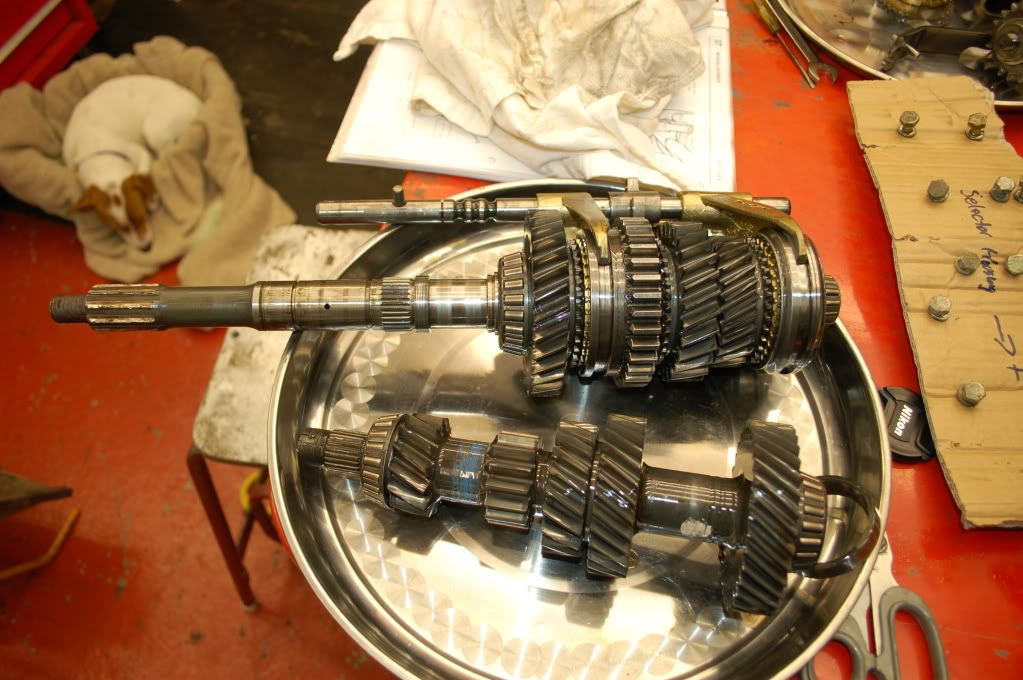
Centre plate – push out bearing races (push fit only).
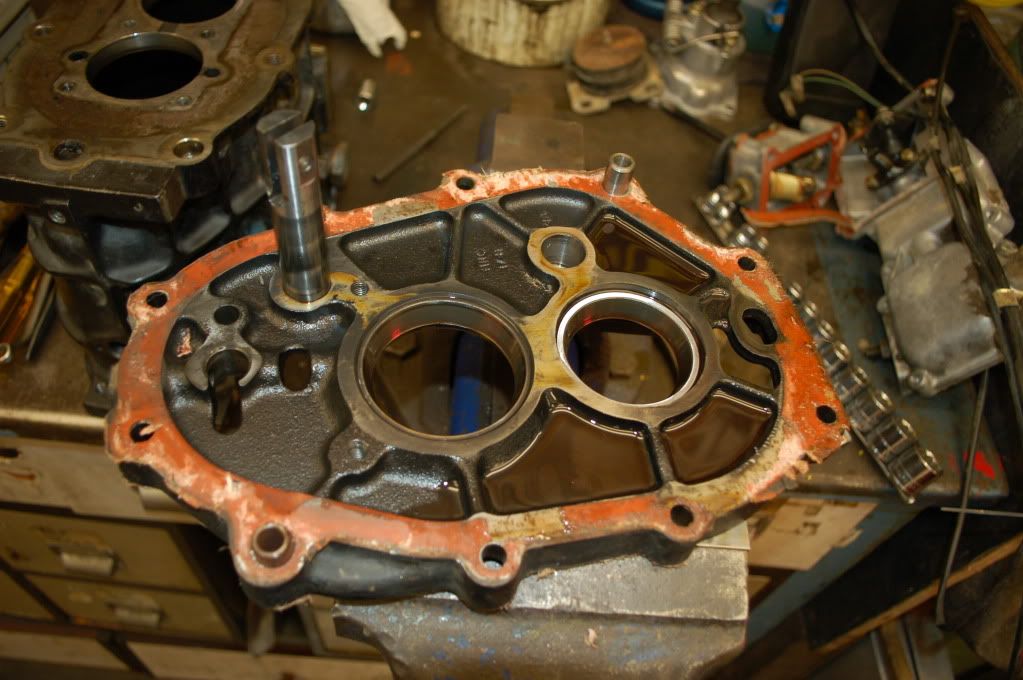
Hold CPS in vice and pull out outer bearing race. I used my slide hammer as I don’t have an internal bearing puller.
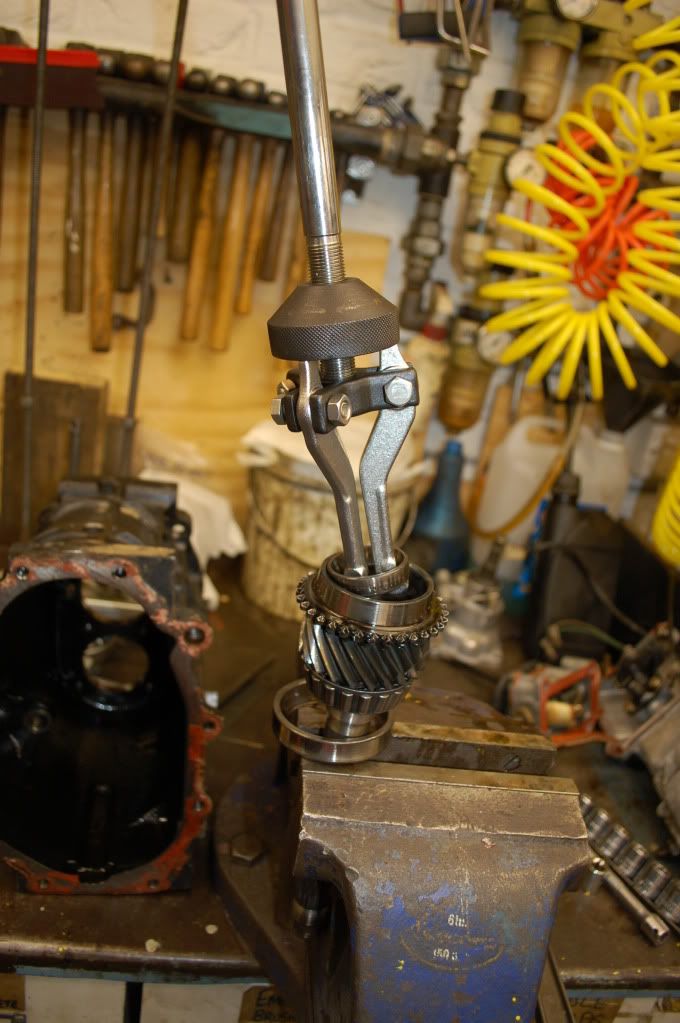
Flip over and pull other bearing race.
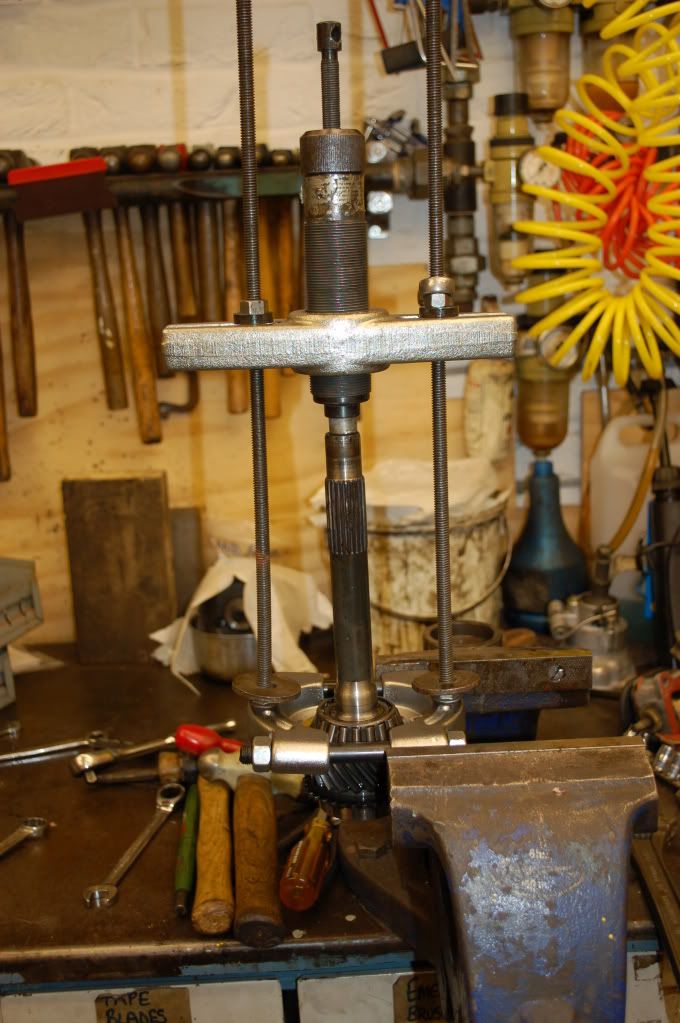
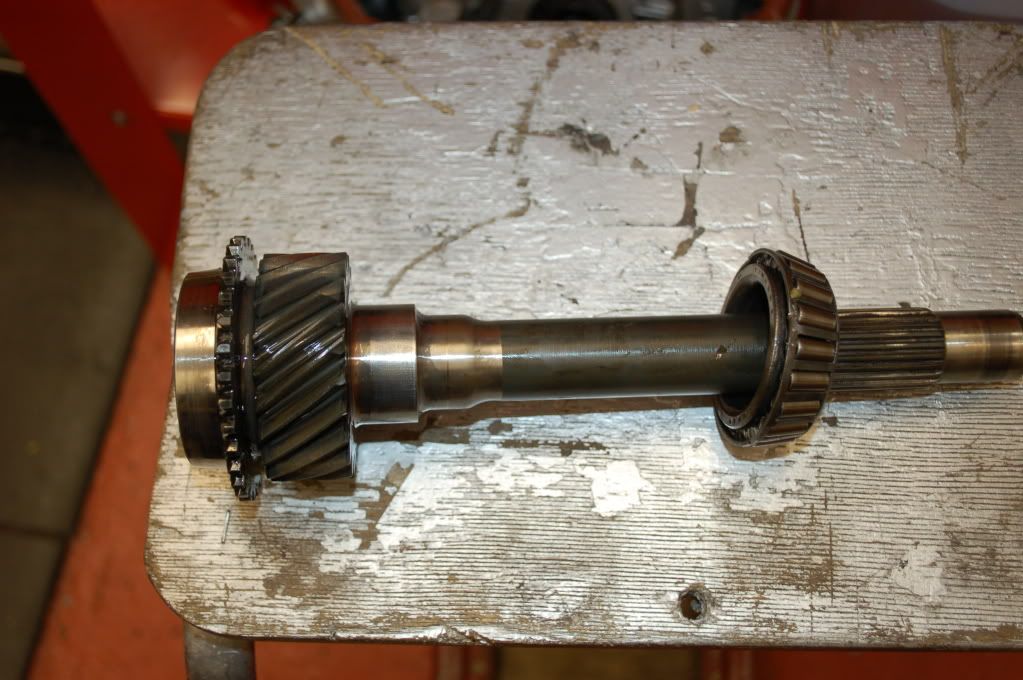
Fitting new bearing – heat CPS to expand.
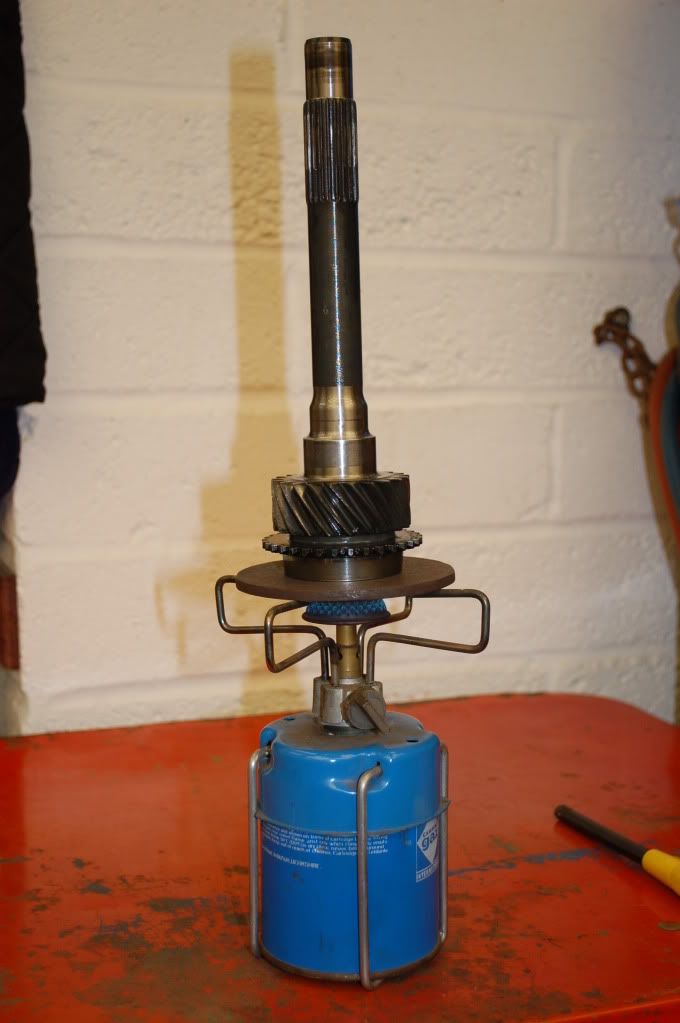
Drop in new bearing outer, making sure it’s seated by tapping it home using old bearing as a sized drift/tool.
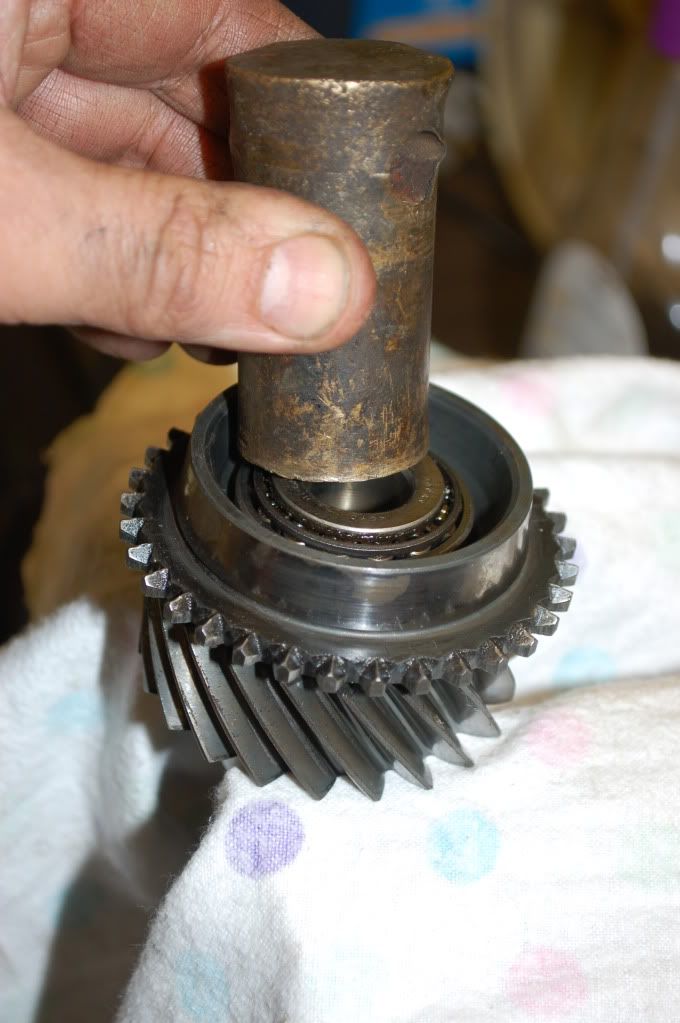
I used the old bearing inner to go into the end of my ‘bearing fitting tube†(a piece of pipe). Ready to use to tap new bearing home.
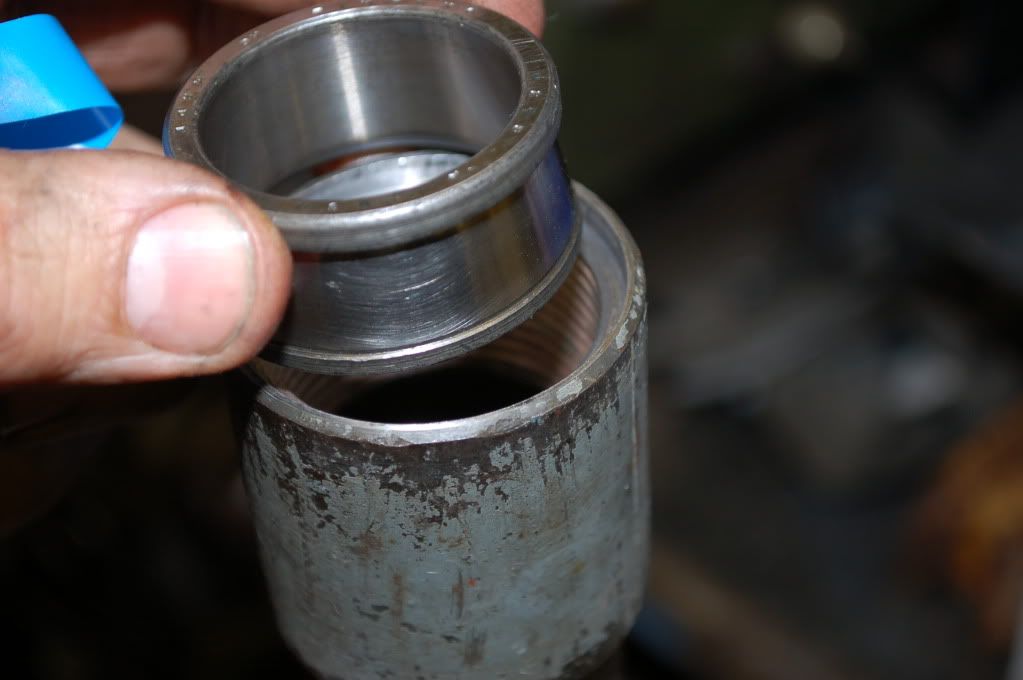
Once CPS has cooled, warm new bearing.
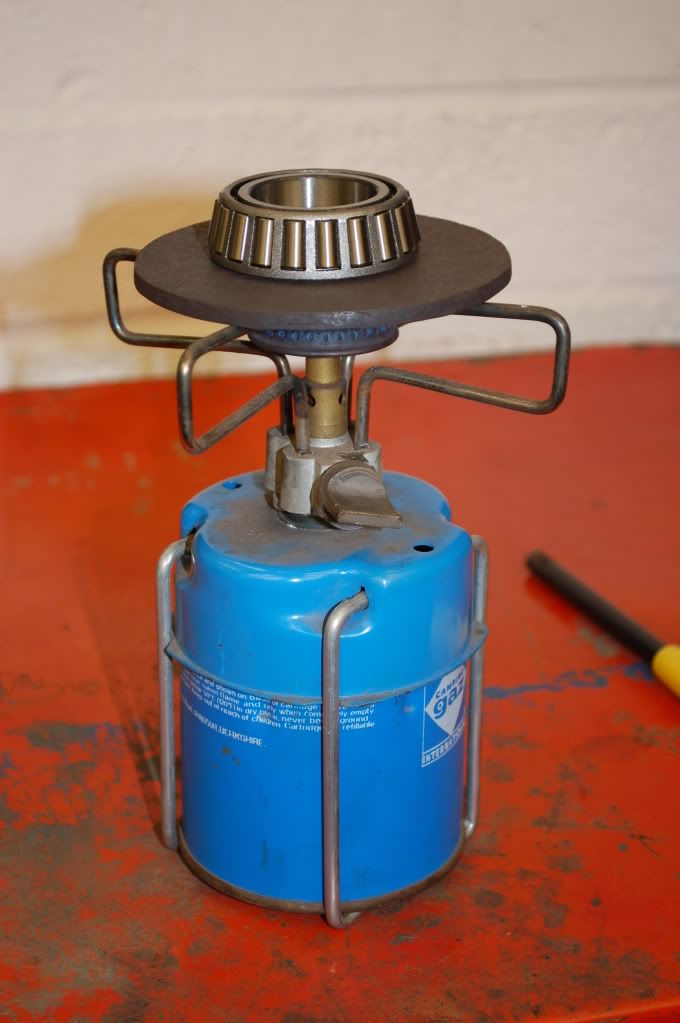
Once warmed, drop onto CPS. Use tool to make sure bearing has seated properly. You find that these bearings simply fall on once heated as they expand a fair bit. But I like to be able to check that they have gone all the way home. I usually use the old bearing races as part of the tool as they are the correct size.
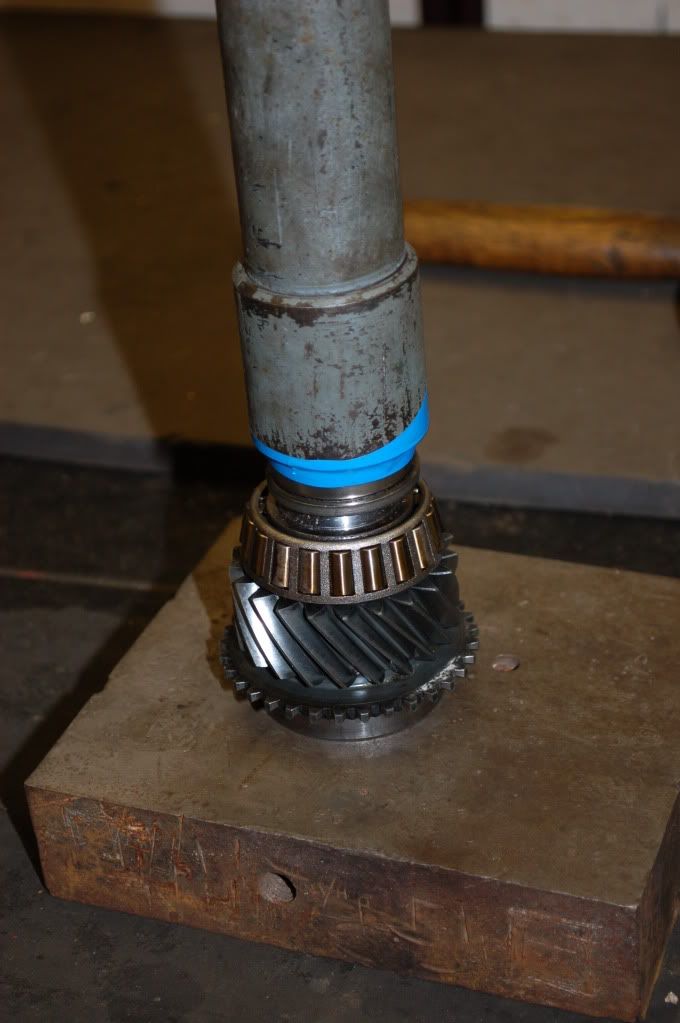
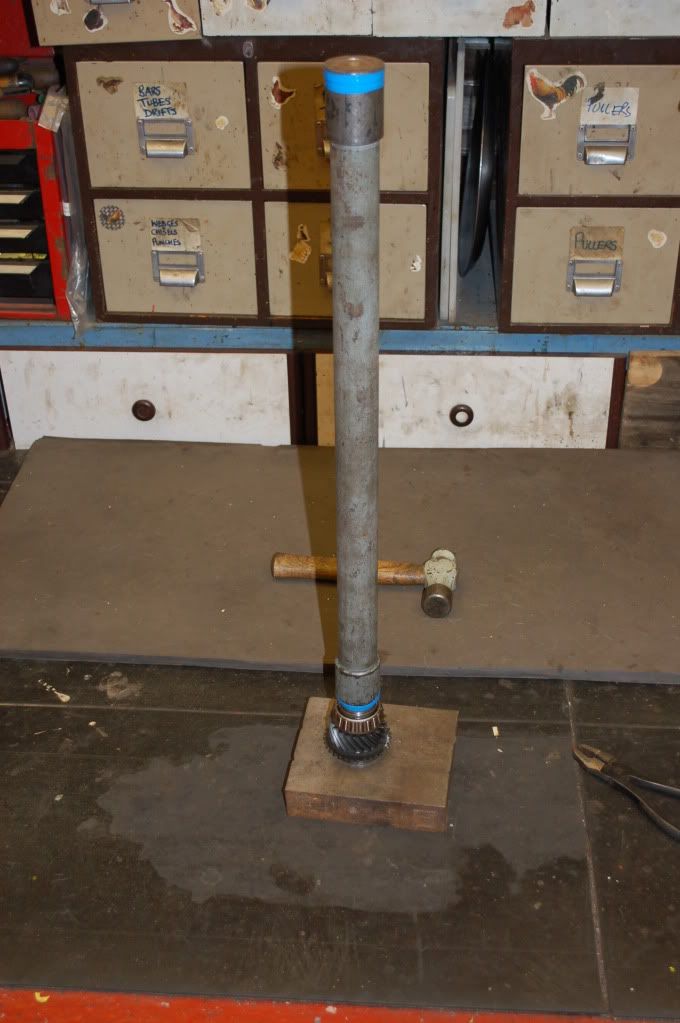
Ok. Onto the mainshaft now. Support in vice.
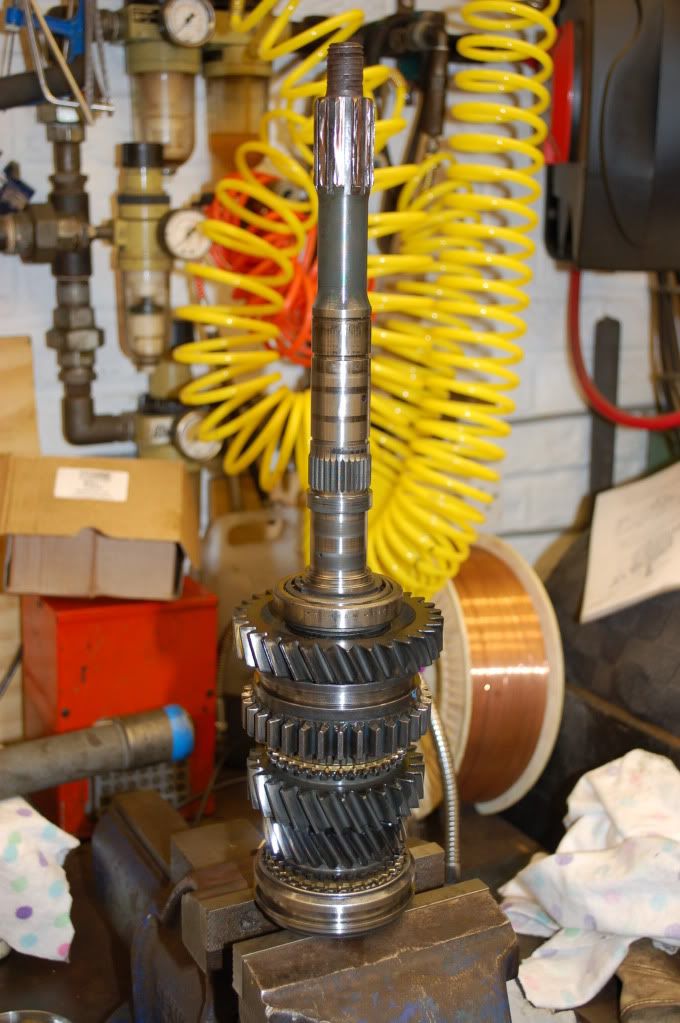
Remove circlip.
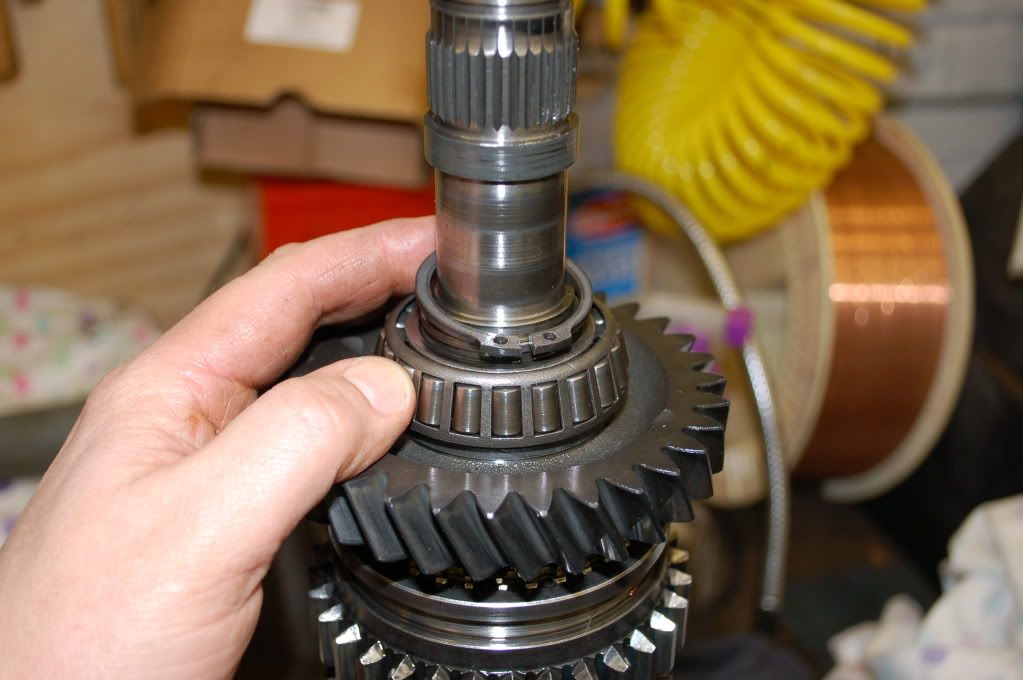
Pull off bearing.
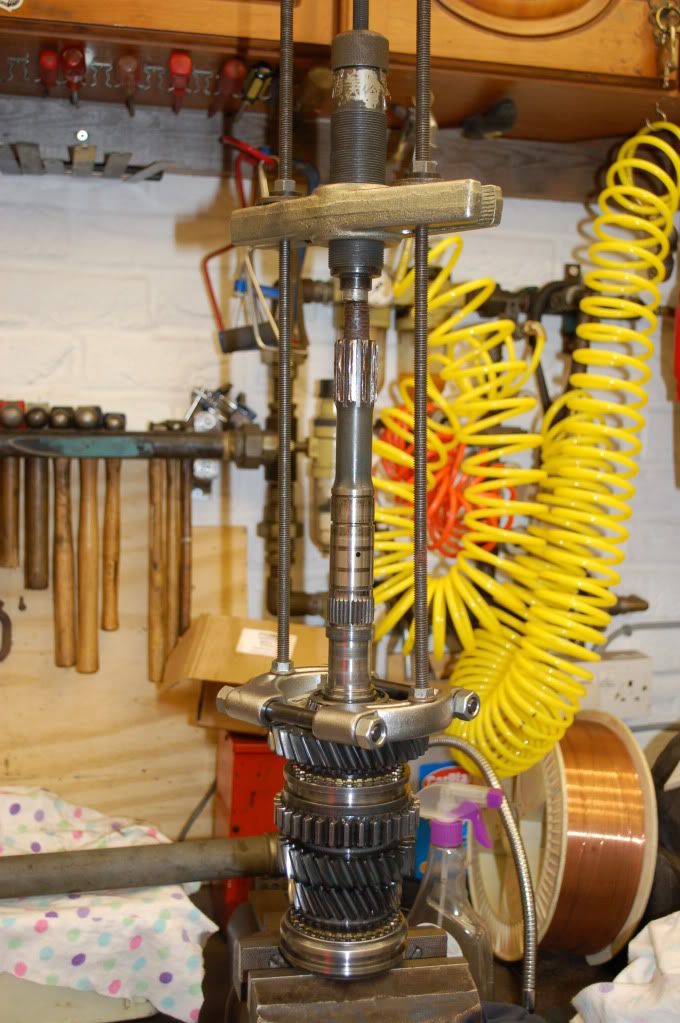
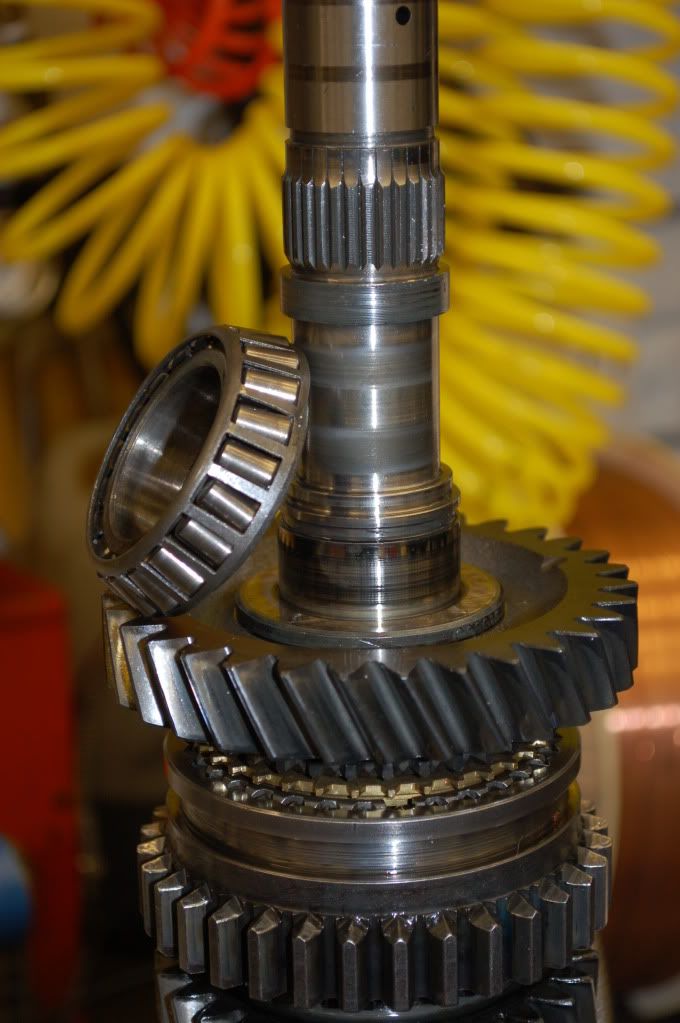
Slide off gear bush, spacer, cone, inner and outer baulk rings. I put a tie wrap around them to keep them all together.
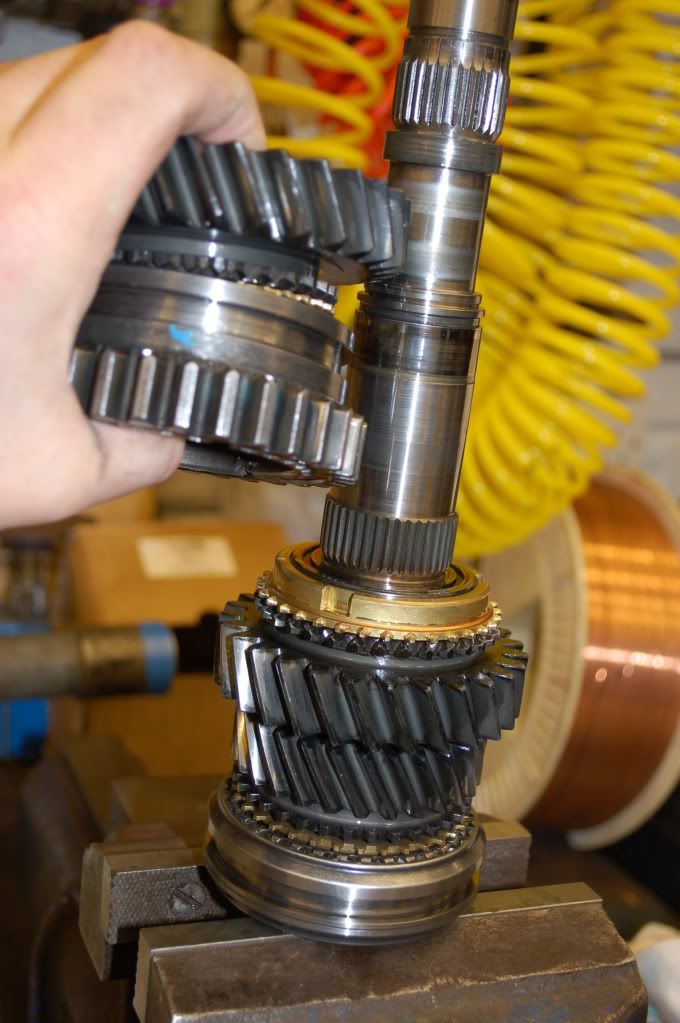
This is where/how you check the synchro for overall wear. You need to be able to get a minimum of a 15 thou (0.015â€) feeler gauge in the gap when the synchro is properly seated. Obviously, check visually for wear, chunks missing etc.
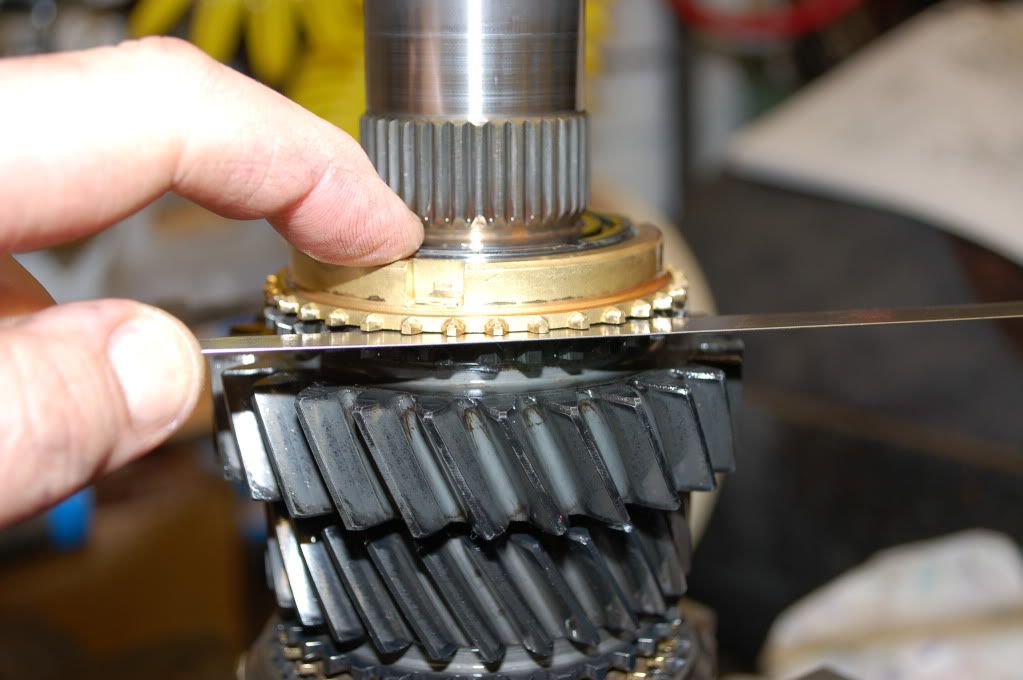
Slide off gear and bearing.
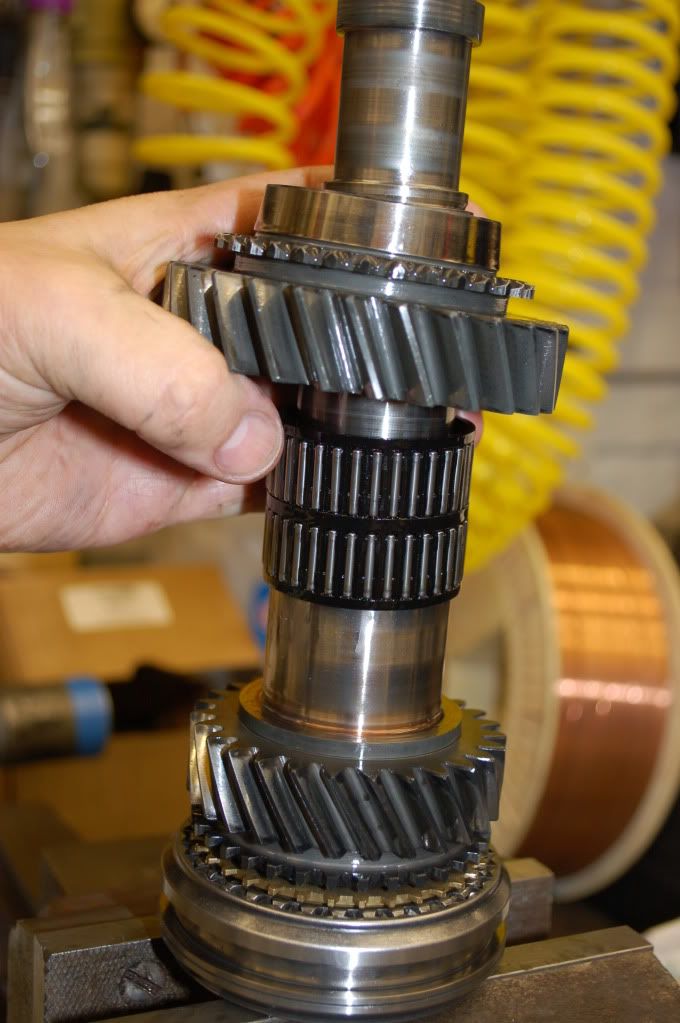
Turn mainshaft round and pull off small CPS end bearing.
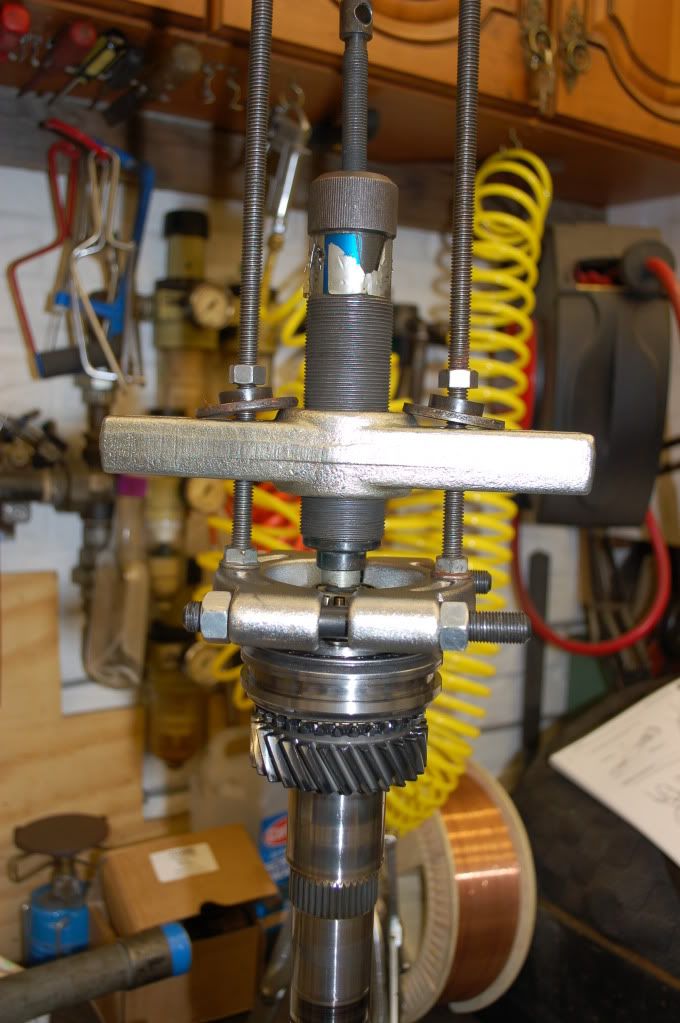
Remove gear assembly. Tie wrap together.
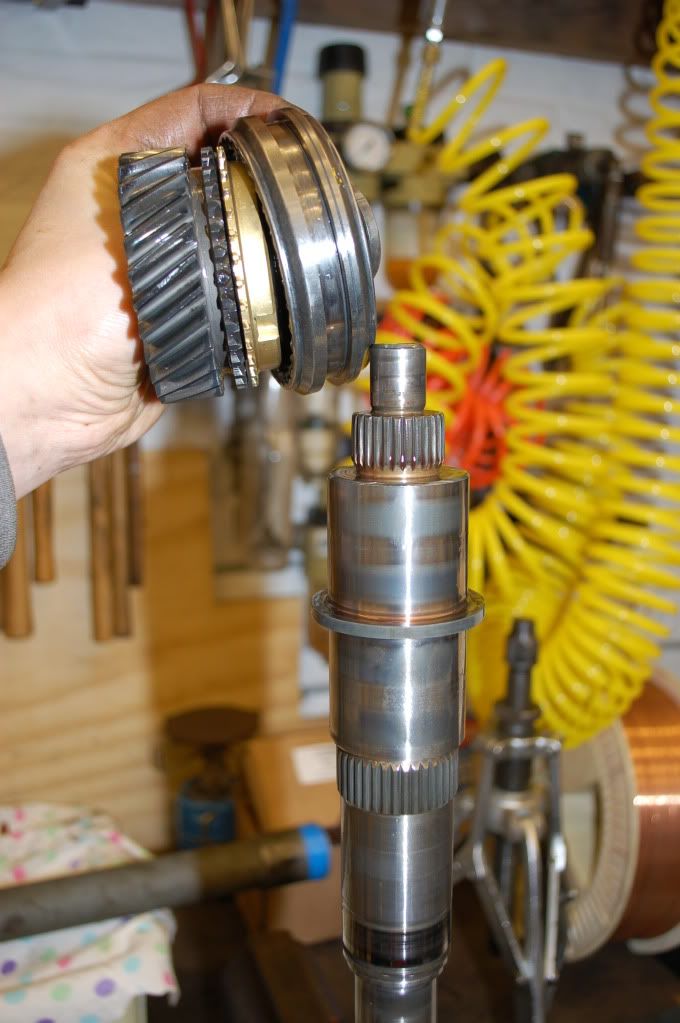
That’s the shaft bare now. Here’s my replacement mainshaft and transfer input gear next to the old ones. You can see one of the 4 drillings in the ‘modified’ input gear here. Clean off new shaft and blow out all oil galleries with compressed airmready for re-assembly.
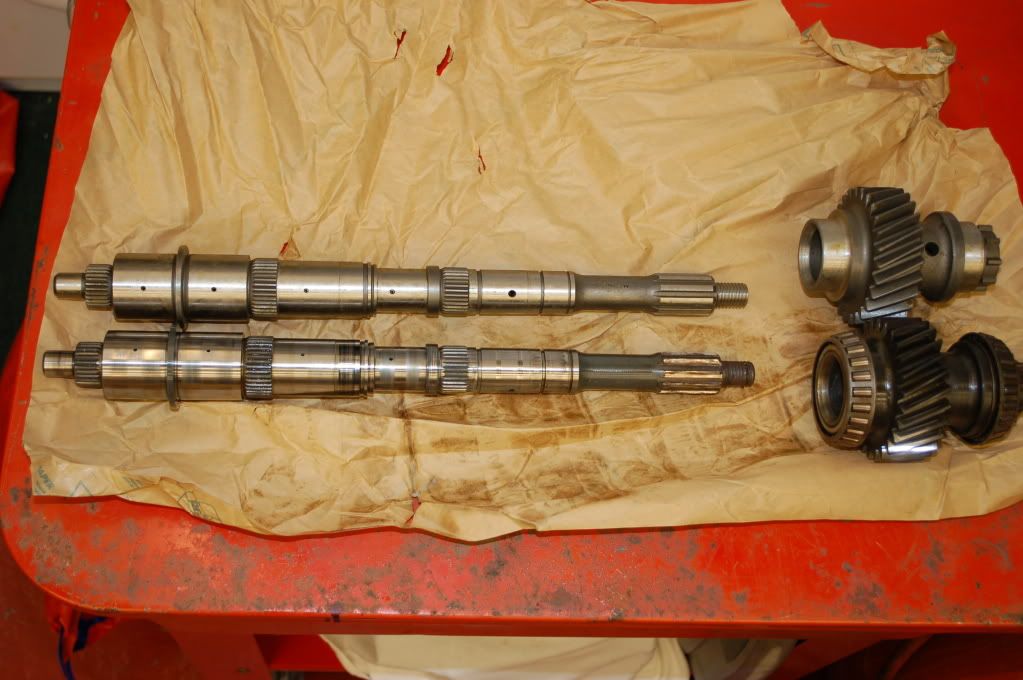
Here’s the layshaft.
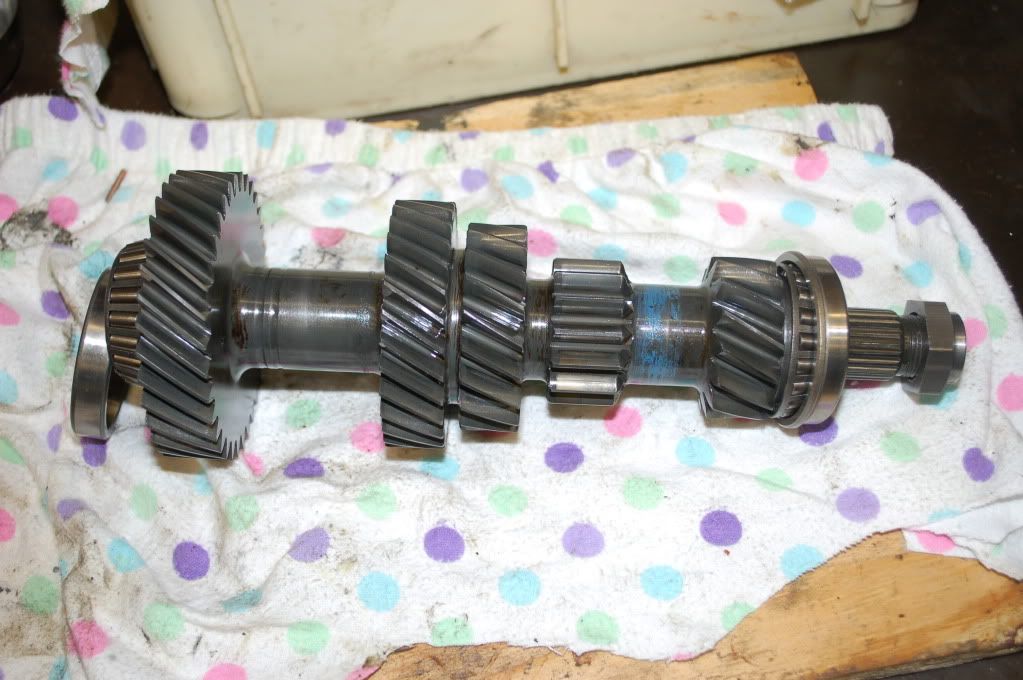
Pull the bearings off as per all the others.
Here’s the Land Rover shaft next to a TR7 one. TR7 in the foreground with smaller straight cut reverse gear.
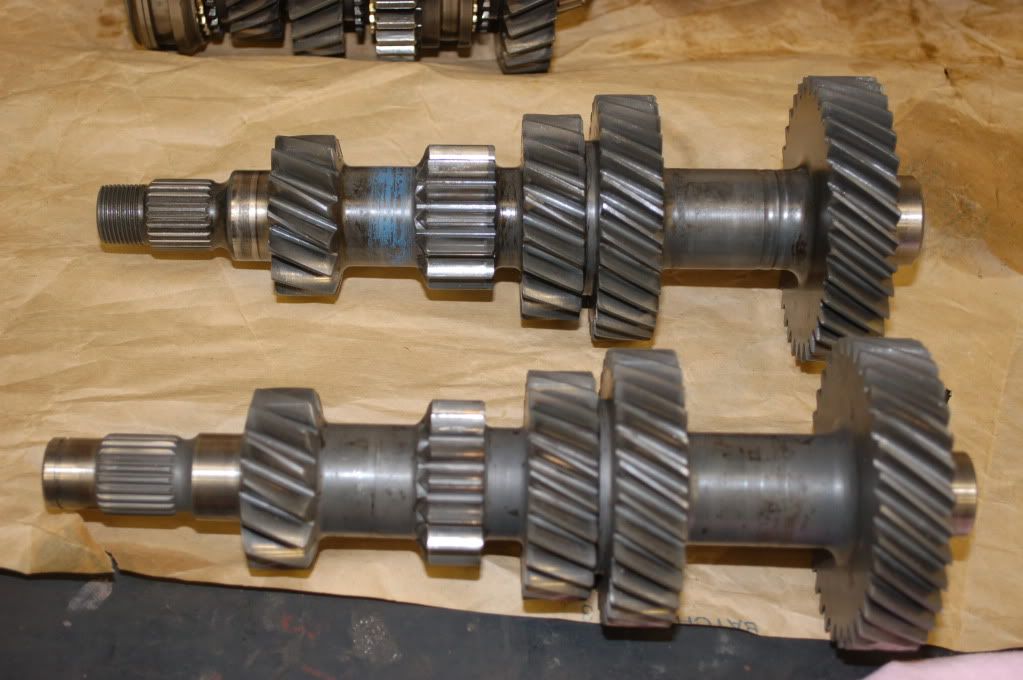
Heat new bearings and fit to mainshaft. Slide hammer to check bearings seated.
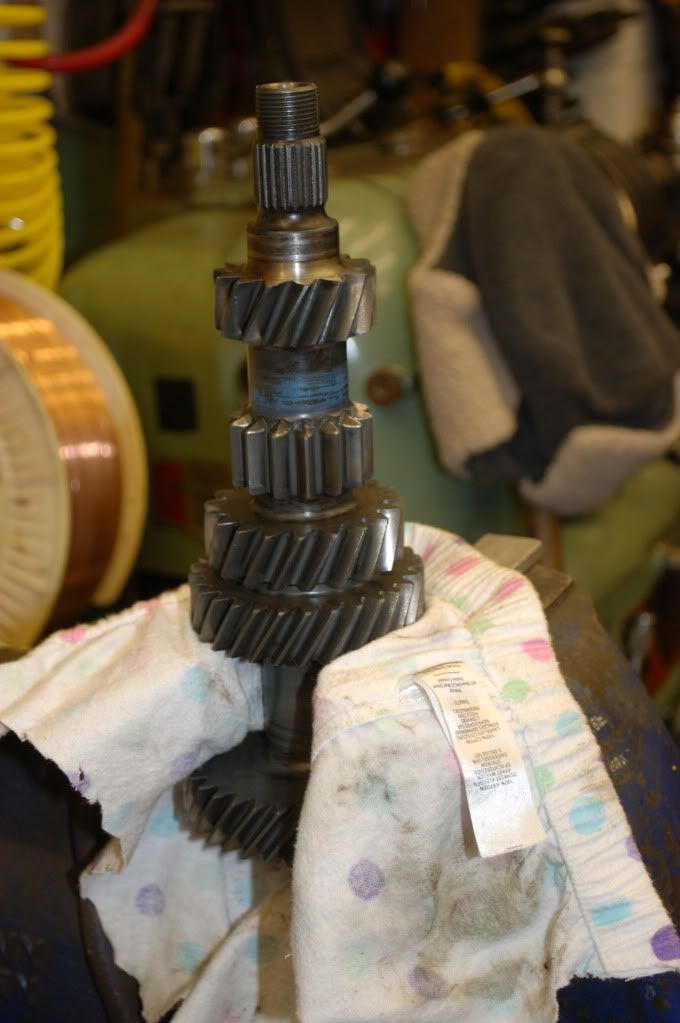
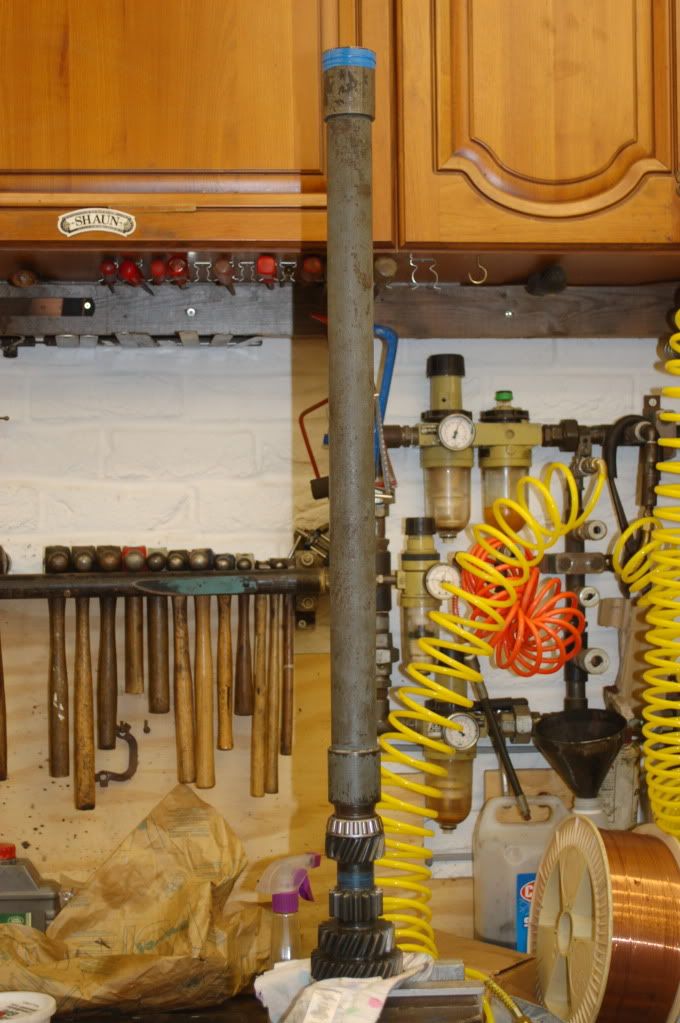
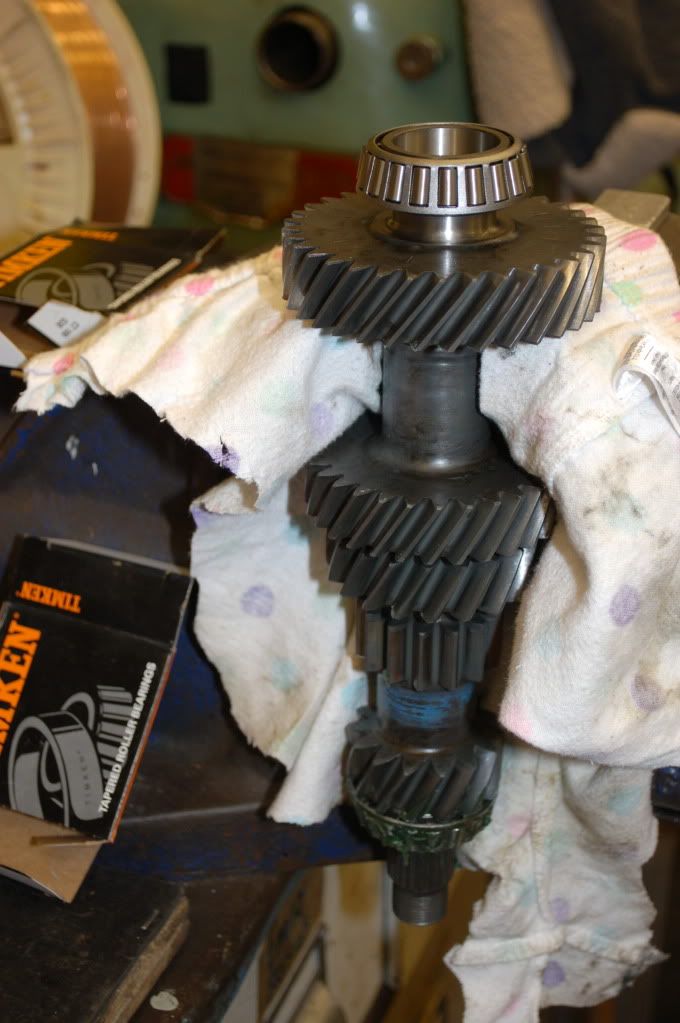
Now to re-assemble to mainshaft. It’s basically the reverse of the dismantling. Lubricate bearings. (By the way. The manual describes in detail how to dismantle each synchro/gear assembly to check for wear and measure end float - where necessary using sized selective spacers blah blah blah. All bearings heated before fitting to enable assembly.
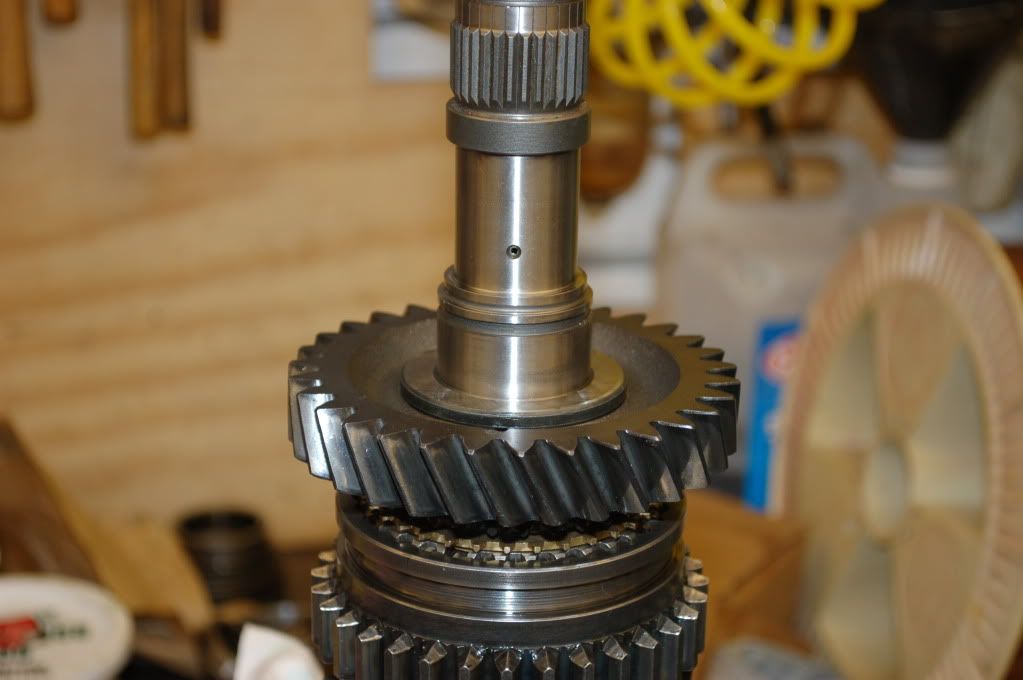
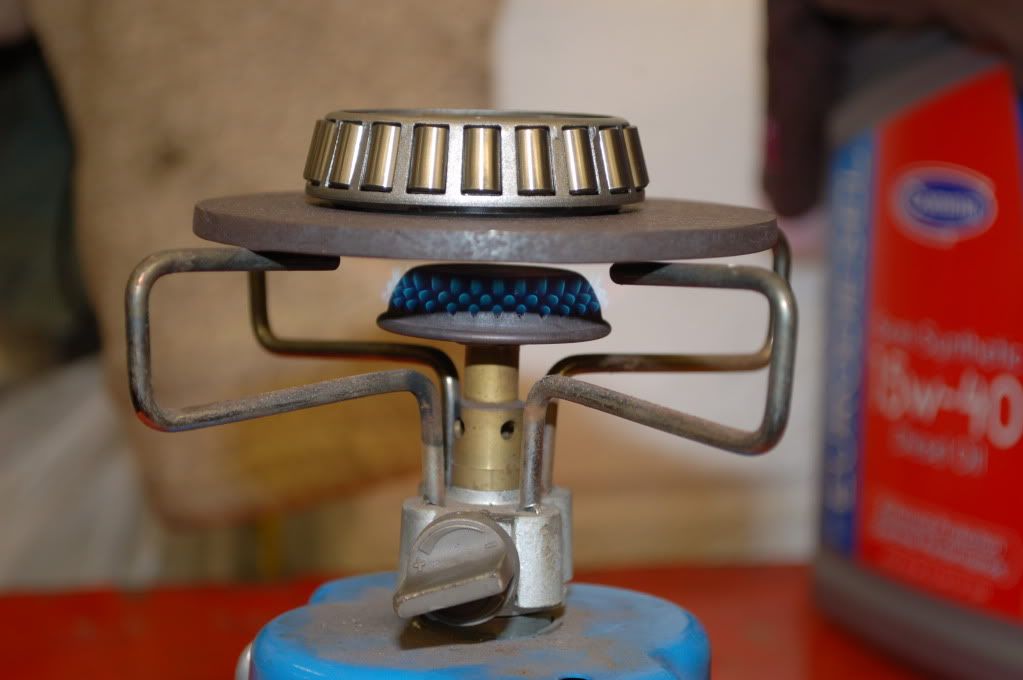
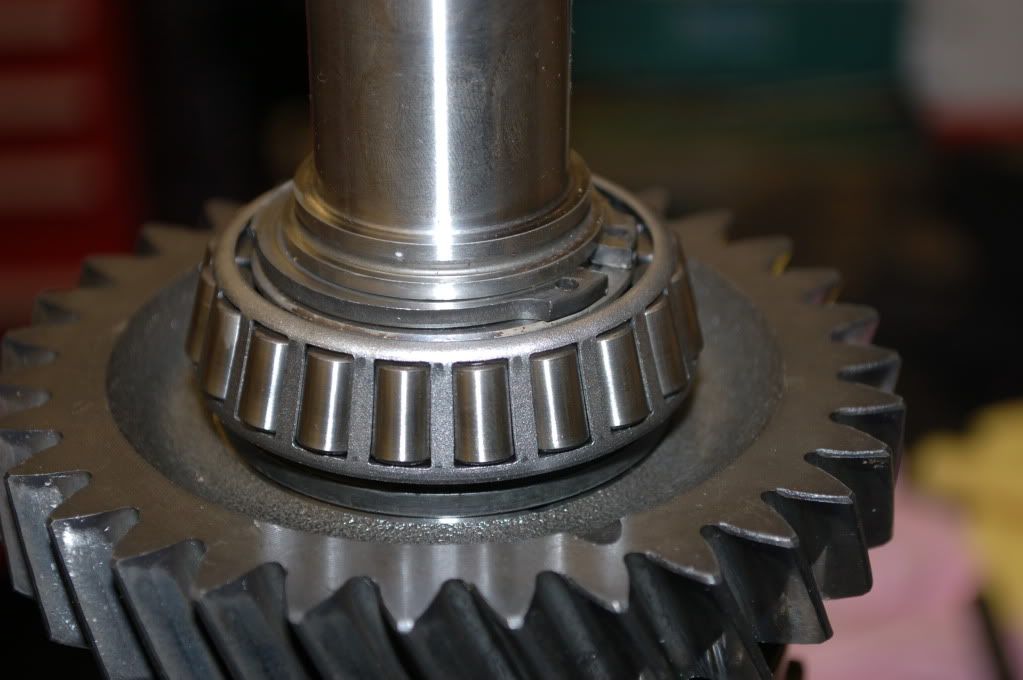
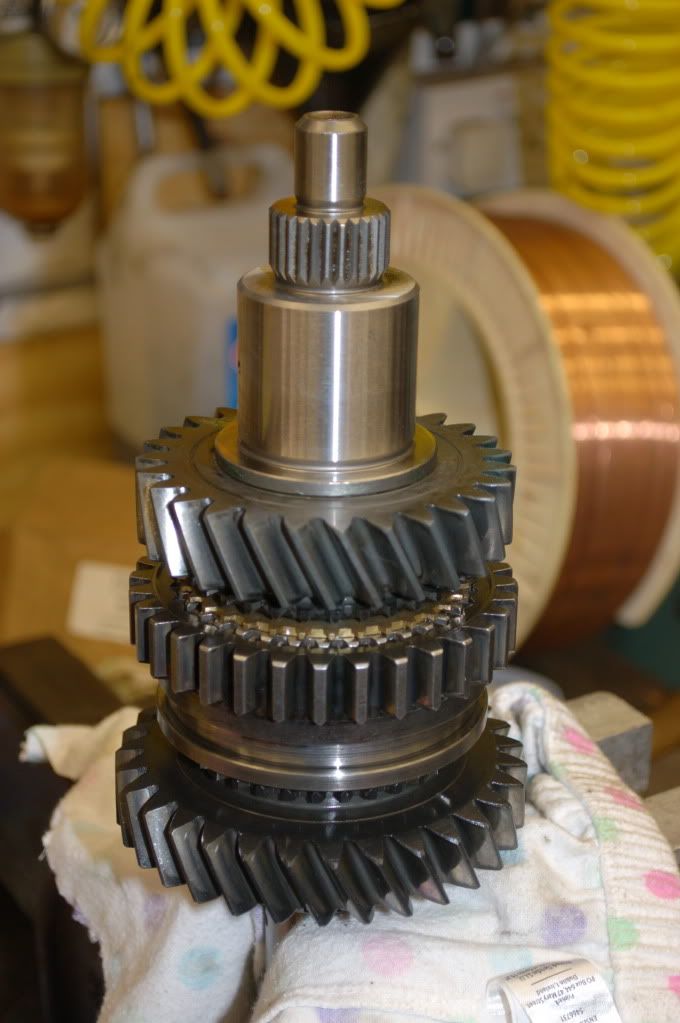
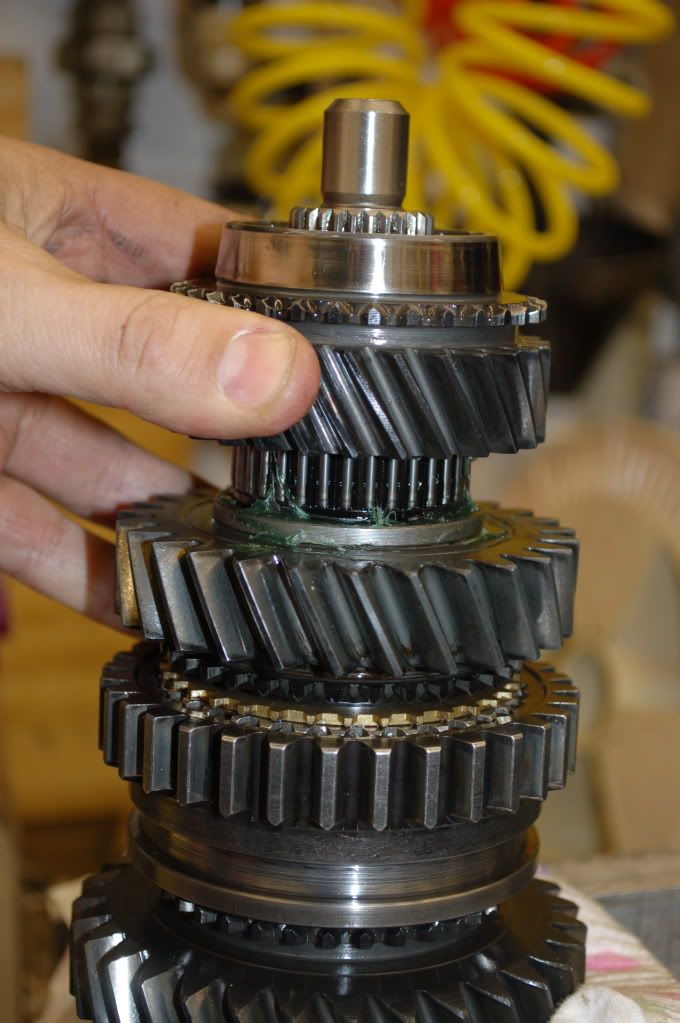
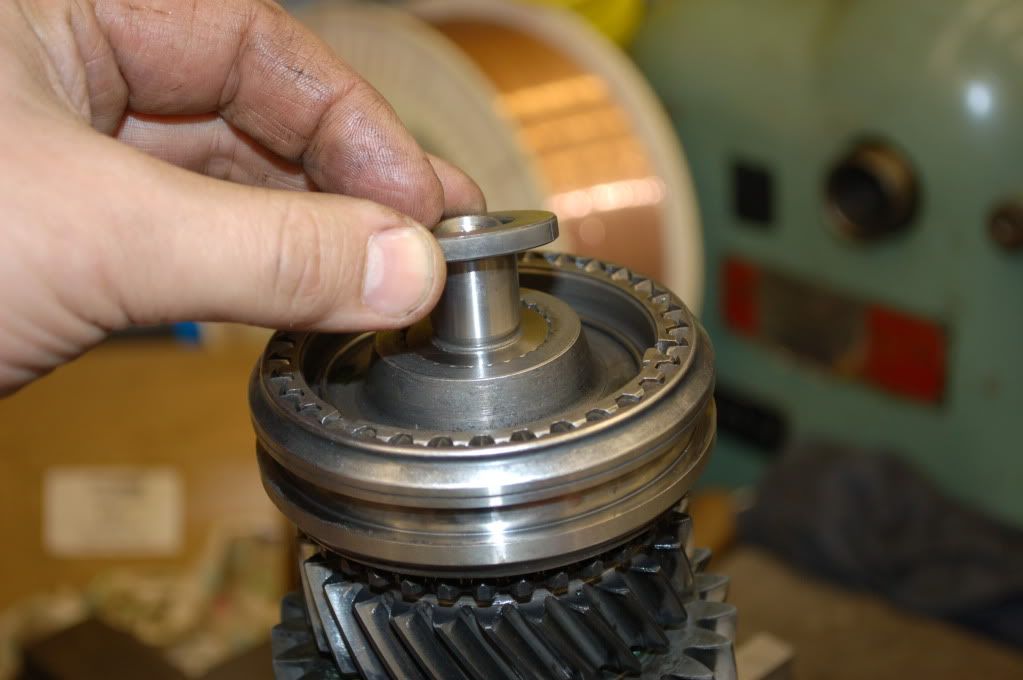
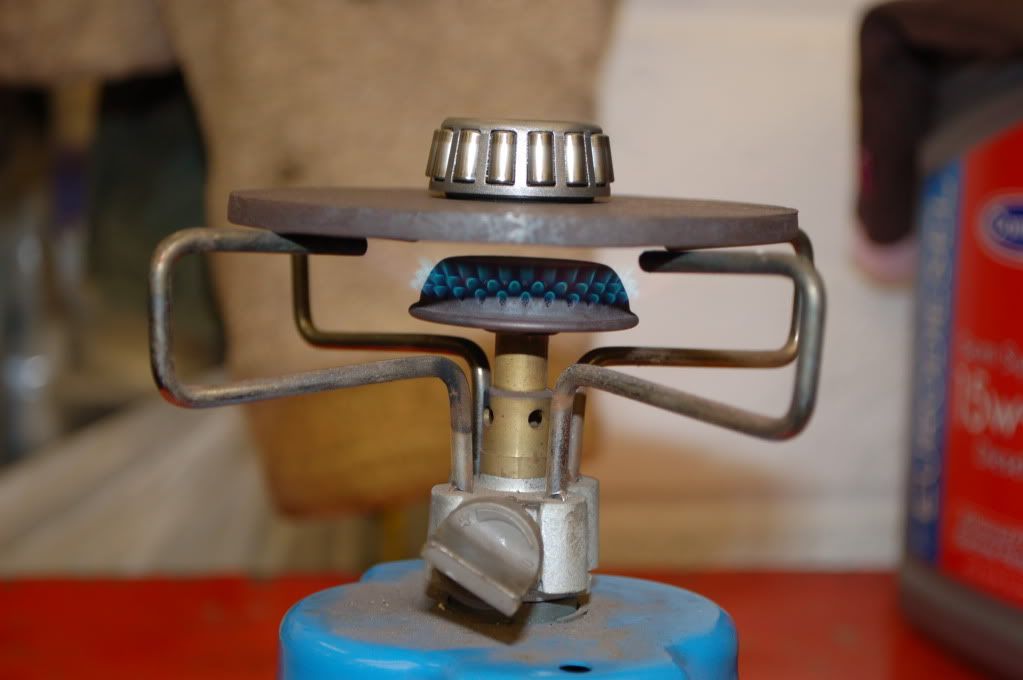
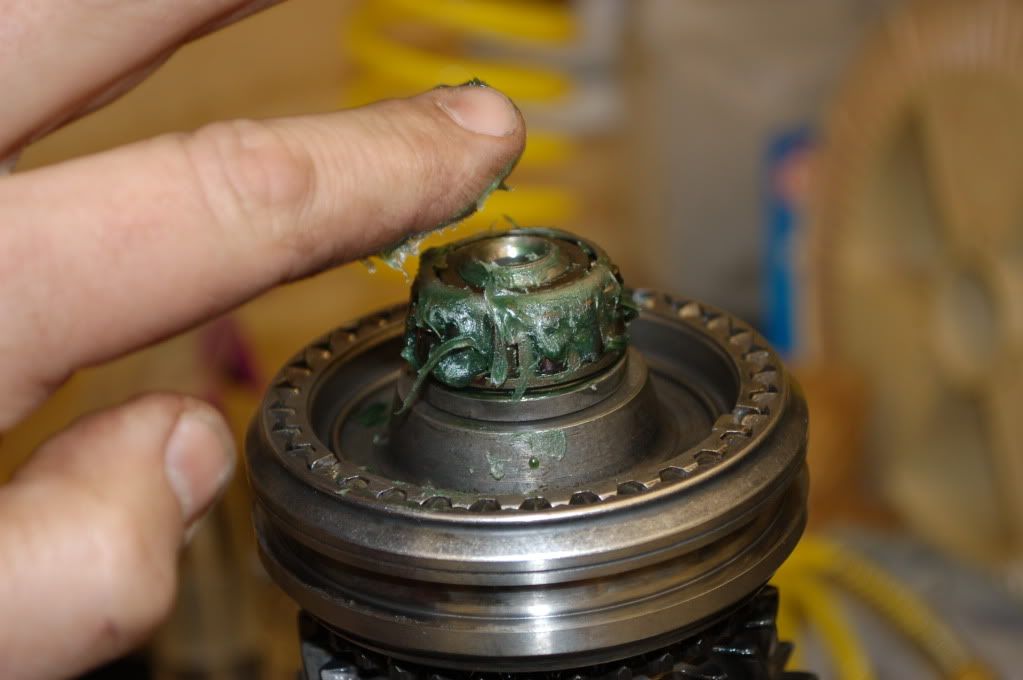
So. Here’s the assembled mainshaft (rear) with a TR7 mainshaft in the middle, and the buggered shaft in the foreground. You can see the slight differences between the shafts. On the TR7 shaft I’ve fitted the spacer you have to machine up to check for endfloat on 1st gear – just in case you were wondering what it was.

Onto the assembly into the centre plate. As you can see. All washed off with gasket faces cleaned. Fit bearing outer races – push fit only.
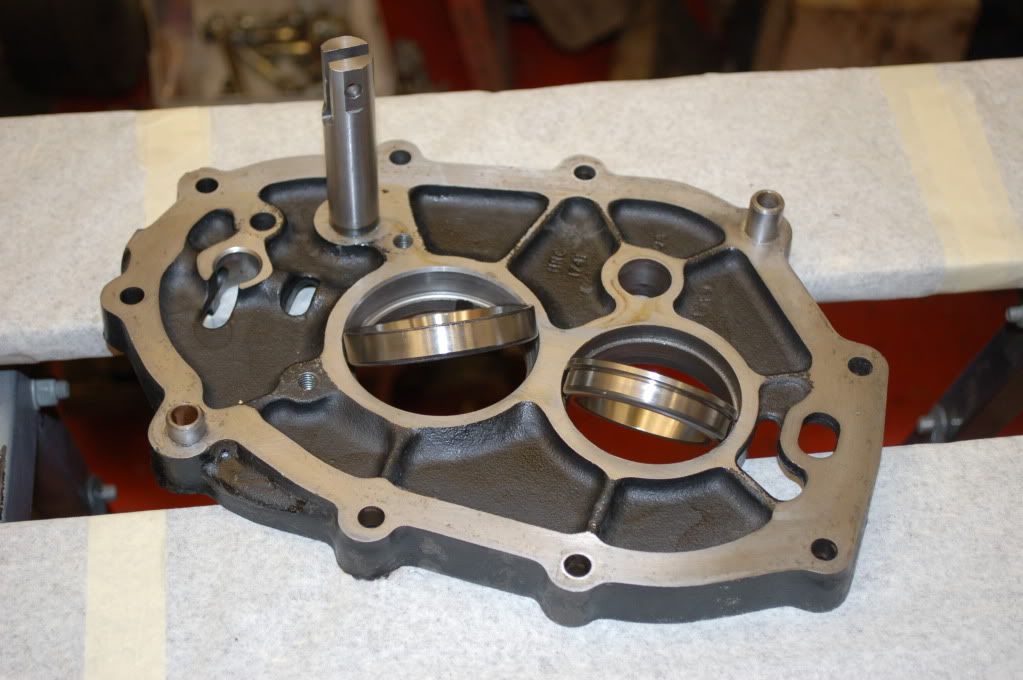
Fit selector forks to mainshaft, ensuring synchro’s are in neutral position.
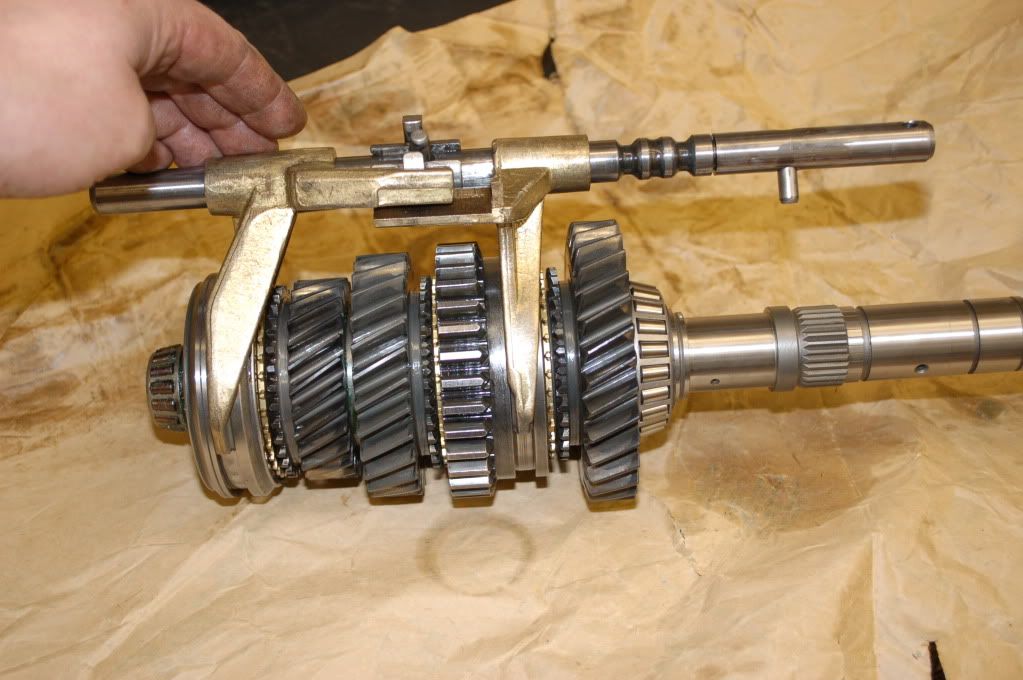
Fit mainshaft and selectors as a single unit to the centre plate.
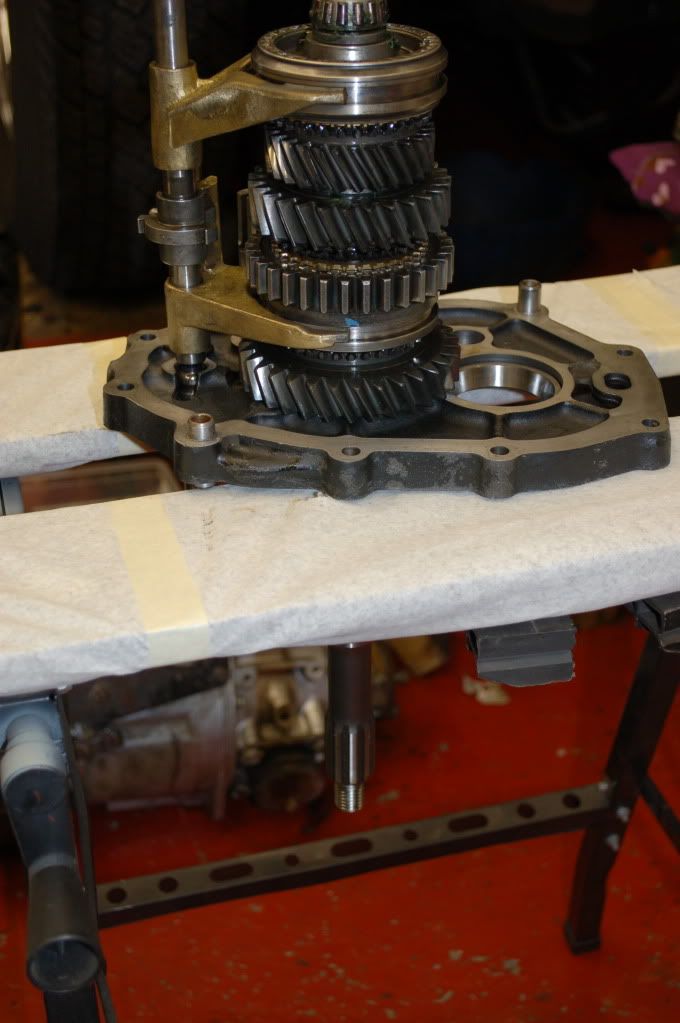
Fit layshaft.
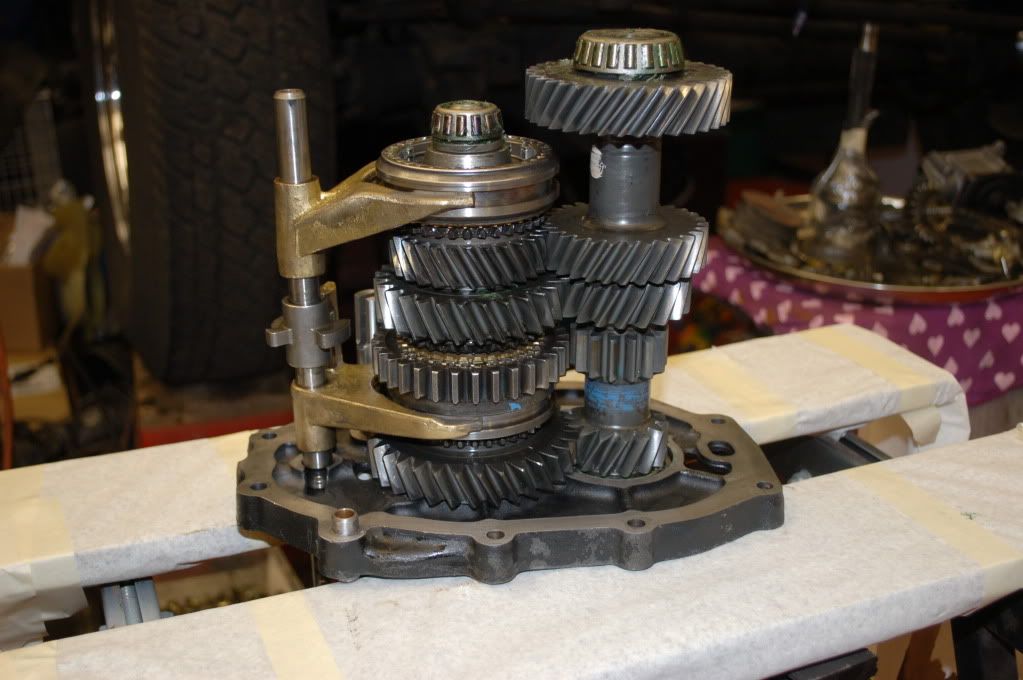
Fit reverse gear assembly and retain with bit of metal. This is to stop the reverse shaft falling out whist continuing with assembly.
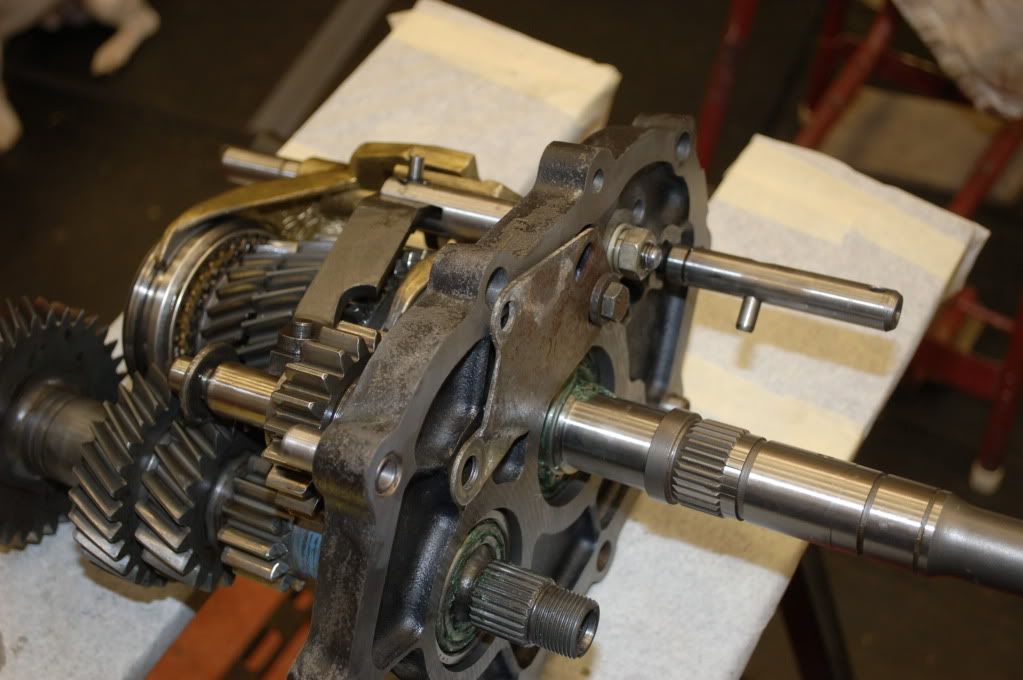
Fit 4th gear baulk ring and CPS.
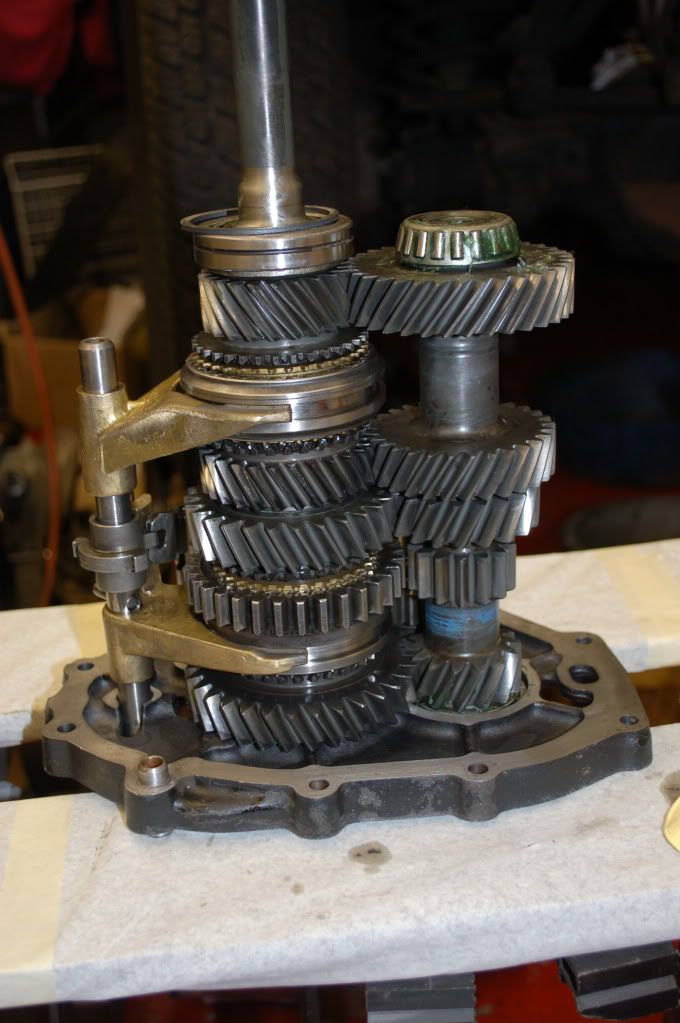
Make sure the selector spool is in neutral position and fit the detent ball, spring and plug.
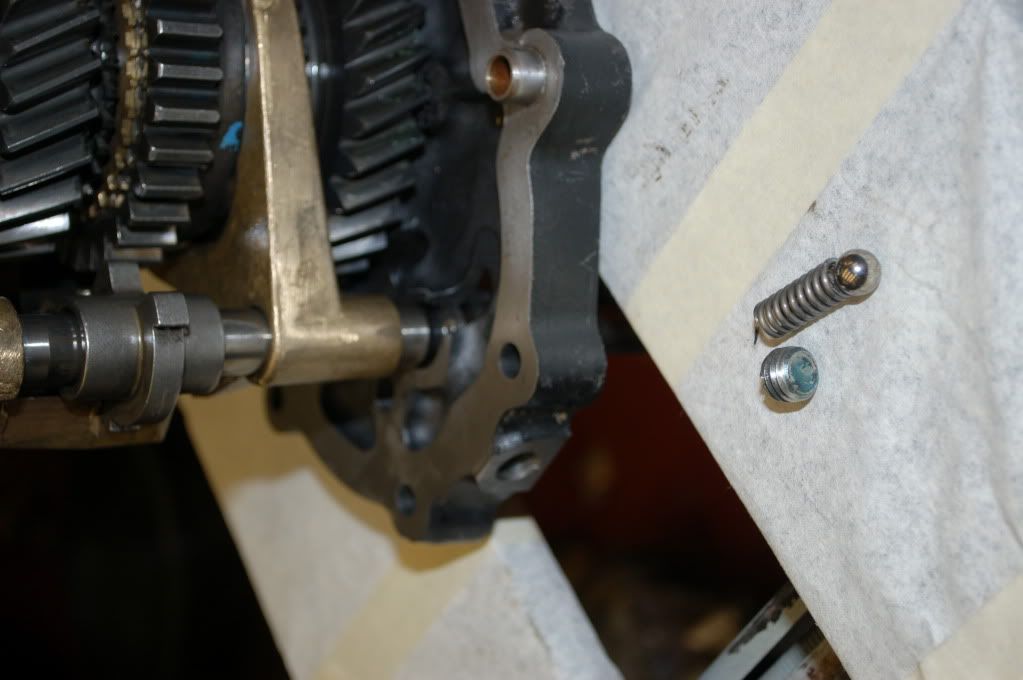
Cleaned out casing.
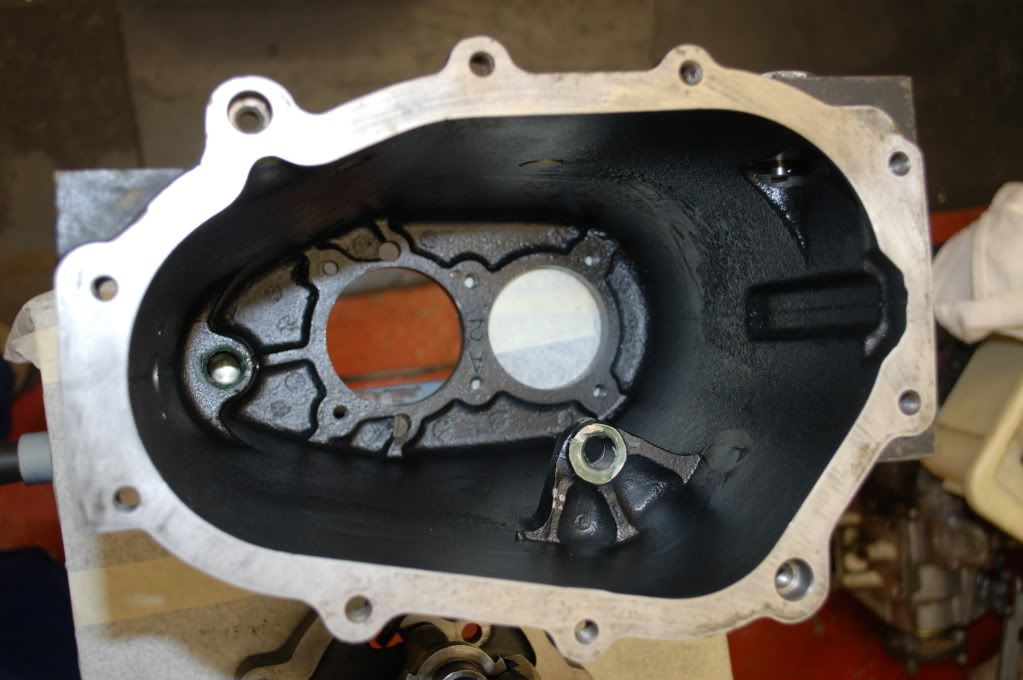
Fit gasket.
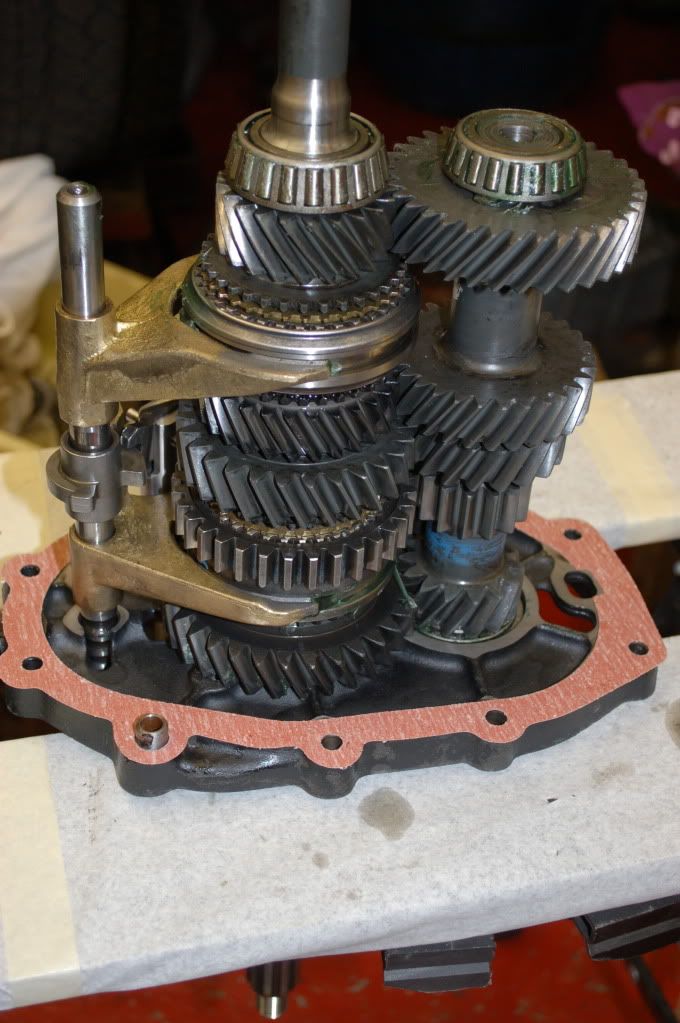
Fit casing (carefully).

Fit outer bearing races – push fit only.
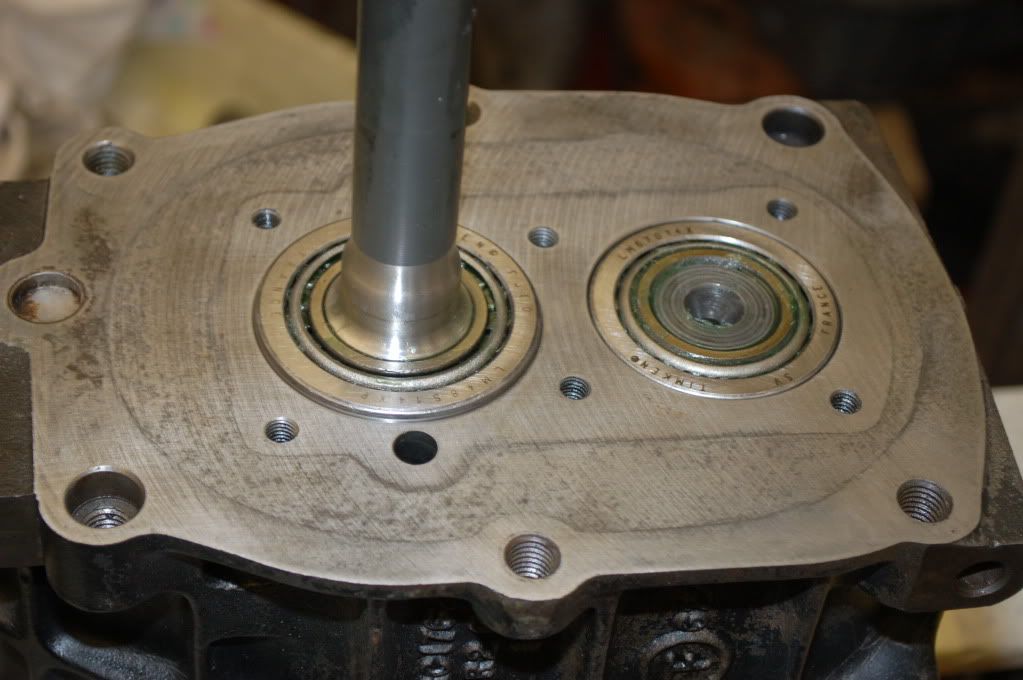
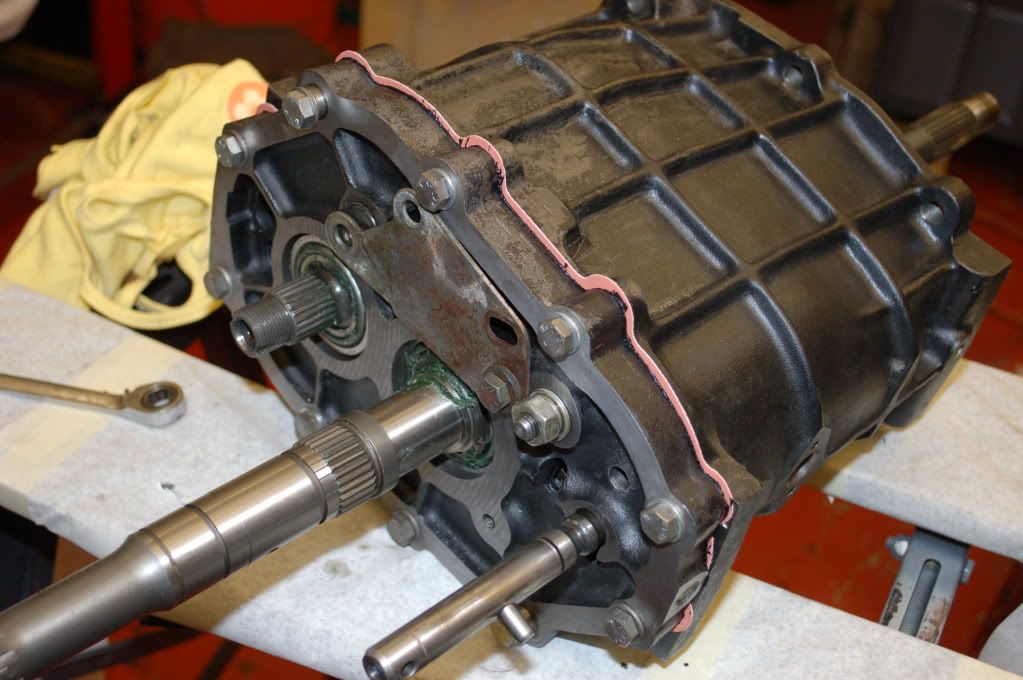
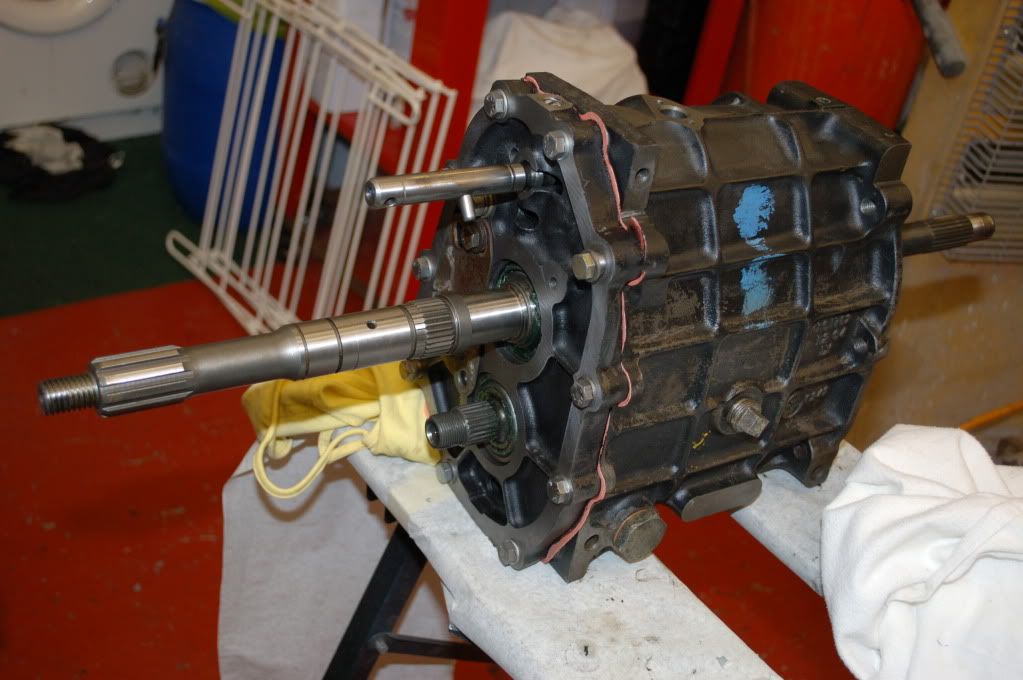
Fit new o-ring and fit spool retainer to casing, securing set screws with Loctite or similar.
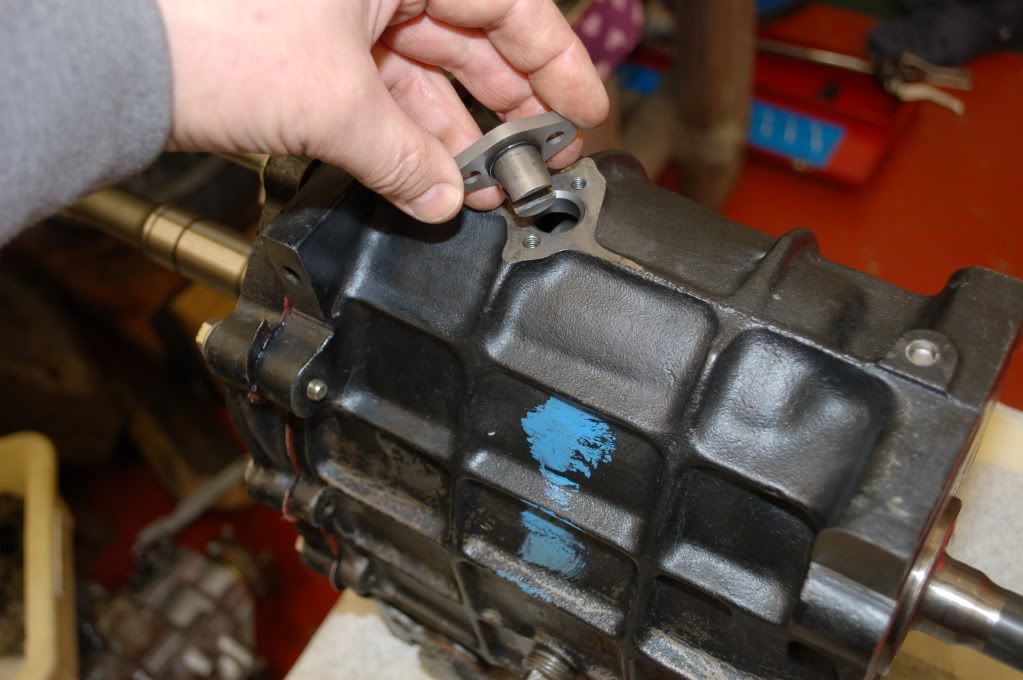
Oh yes – Loctite in detent plug.
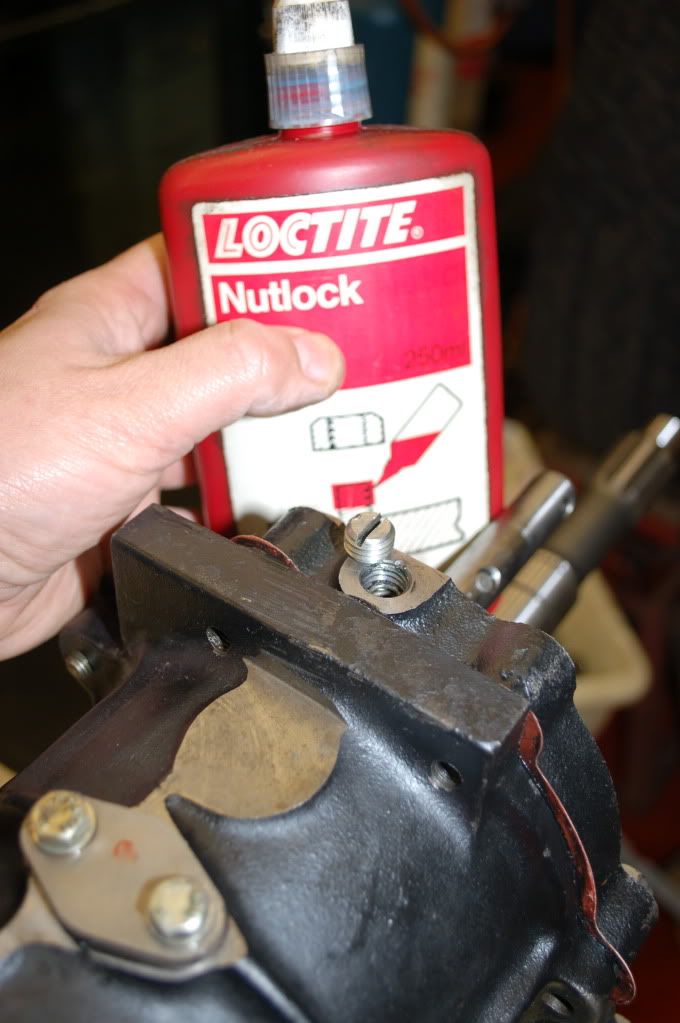
Stake plug.
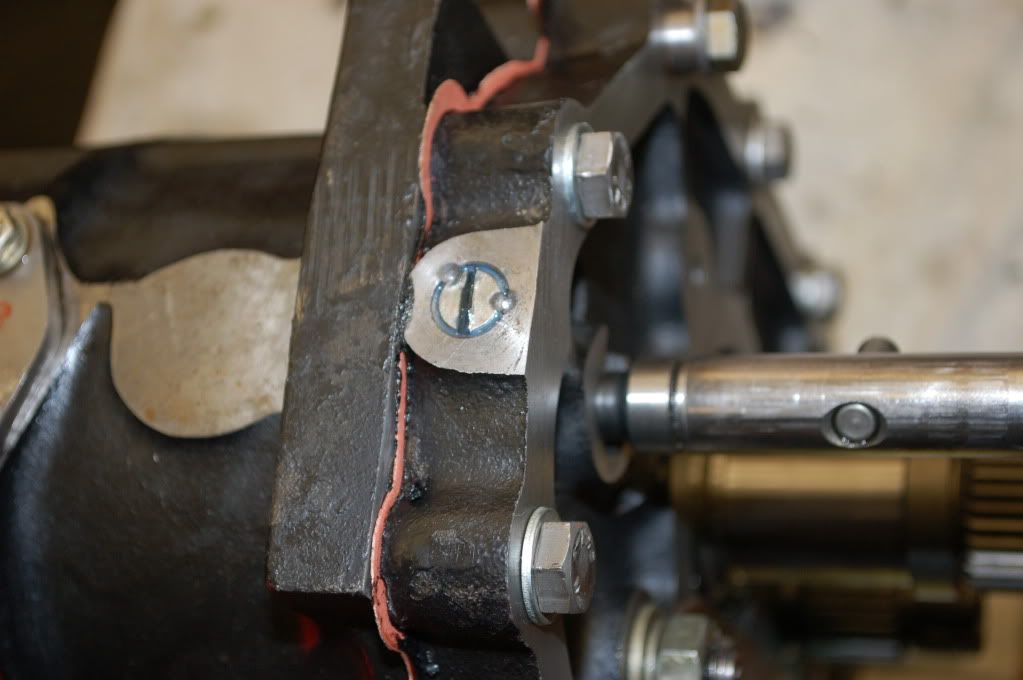
Now it’s time to make a tool to hold the front bearings in place, but mainly to take the force (as opposed to the bearing) on the layshaft when fitting the tight 5th gear assembly later.
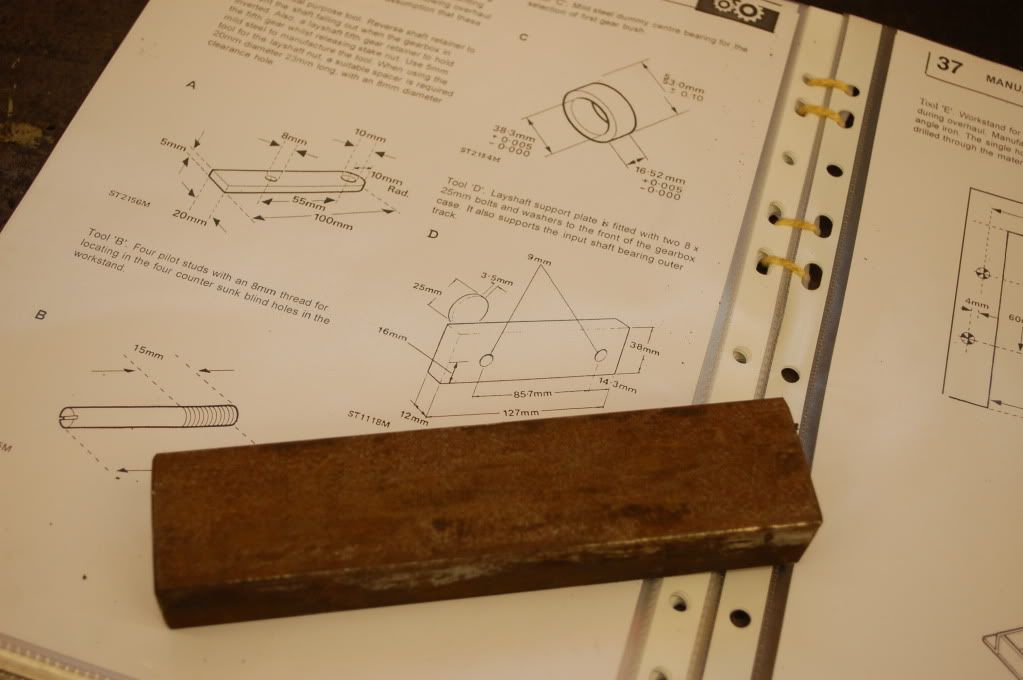
The manual gives dimensions. Take a piece of bar. Marked out and centre-popped ready for drilling.
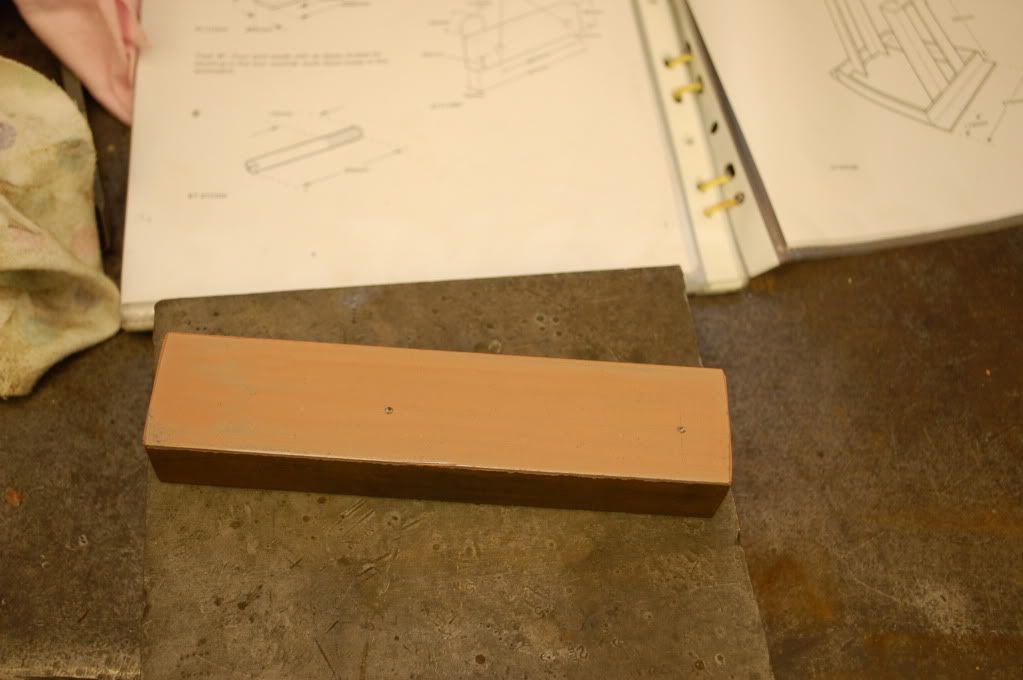
Spot drill.
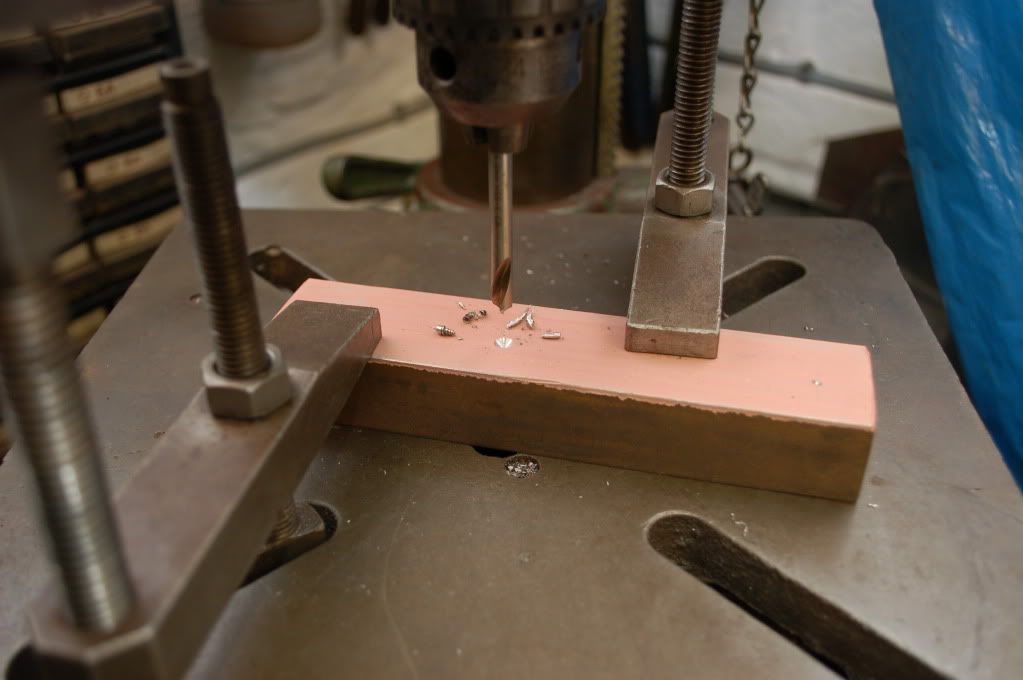
Drill out.
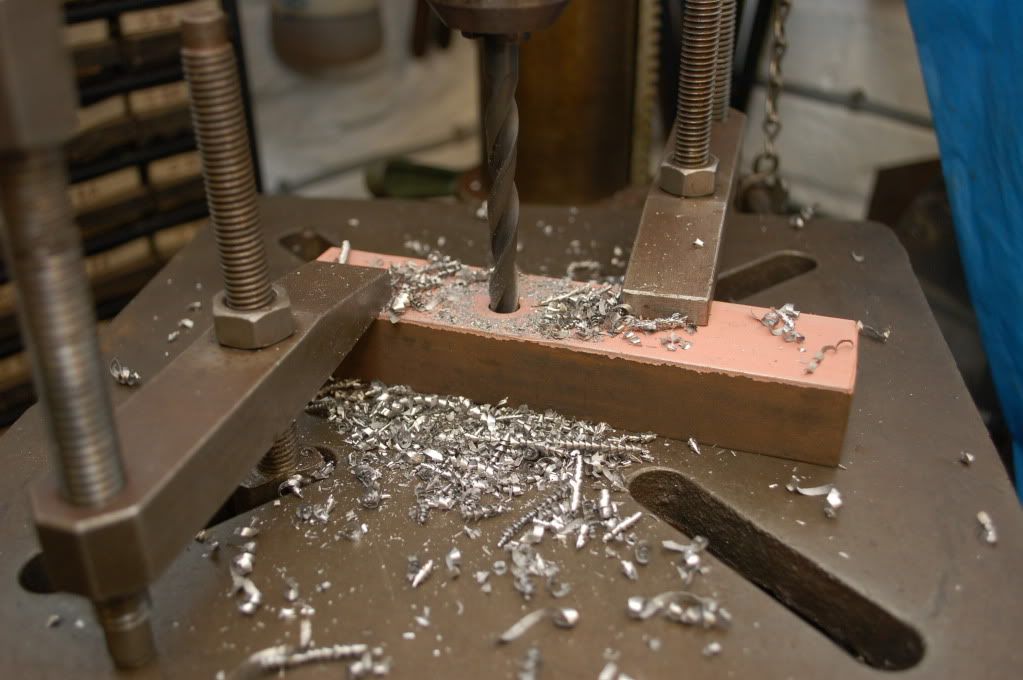
Now to make the distance piece that sits under this bar and picks up on the end of the layshaft.
Bit of scrap bar.

Part off disc 3.5mm x 25mm

Disc and bar ready. You could just use a few washers of course.
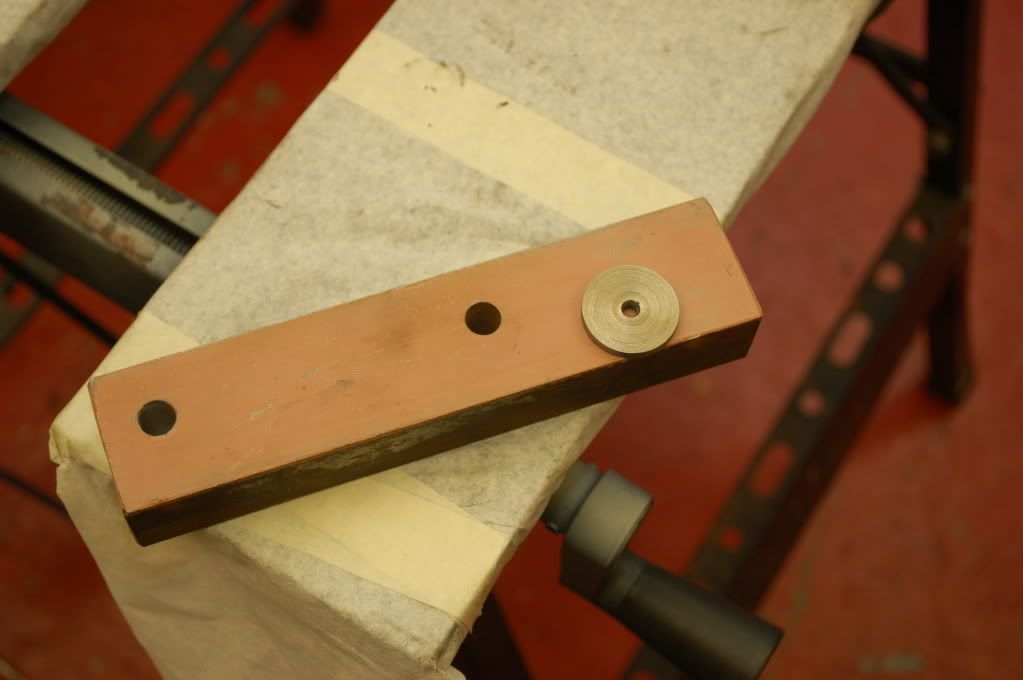
Disc ‘stuck’ on the end of the layshaft with a bit of grease to keep it in place.
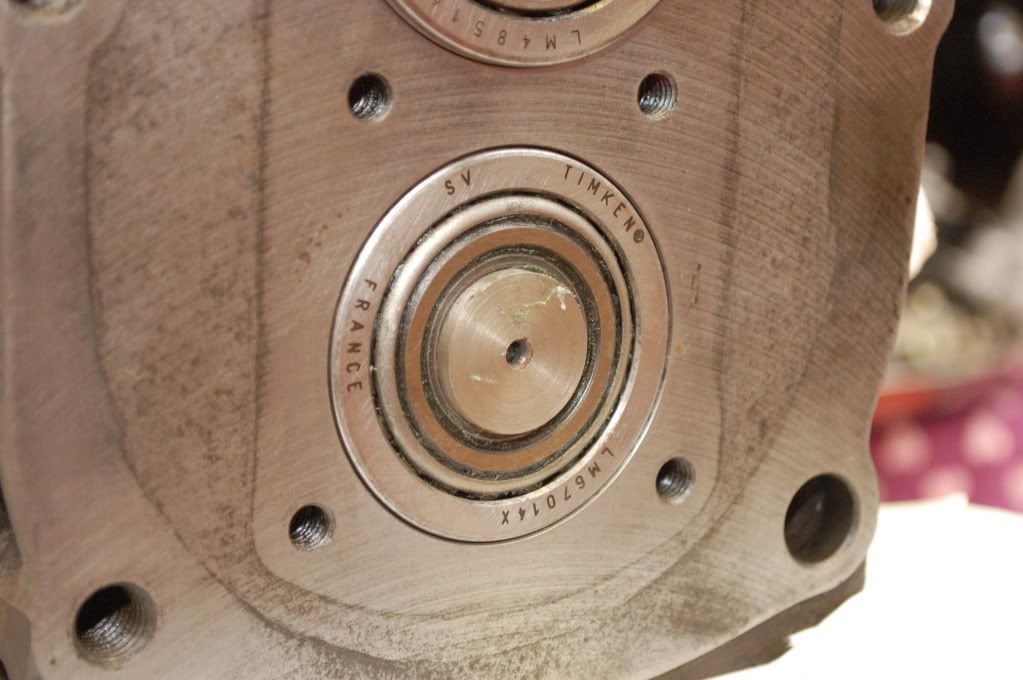
Bolt bar across.
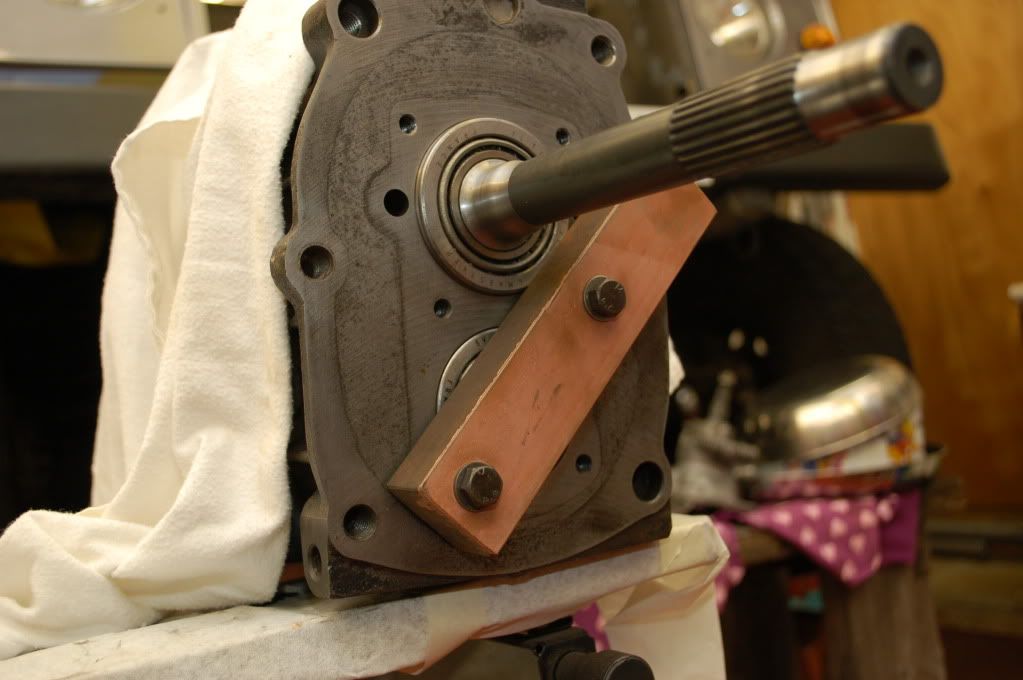
Invert box and remove reverse gear shaft holding ‘tool’.
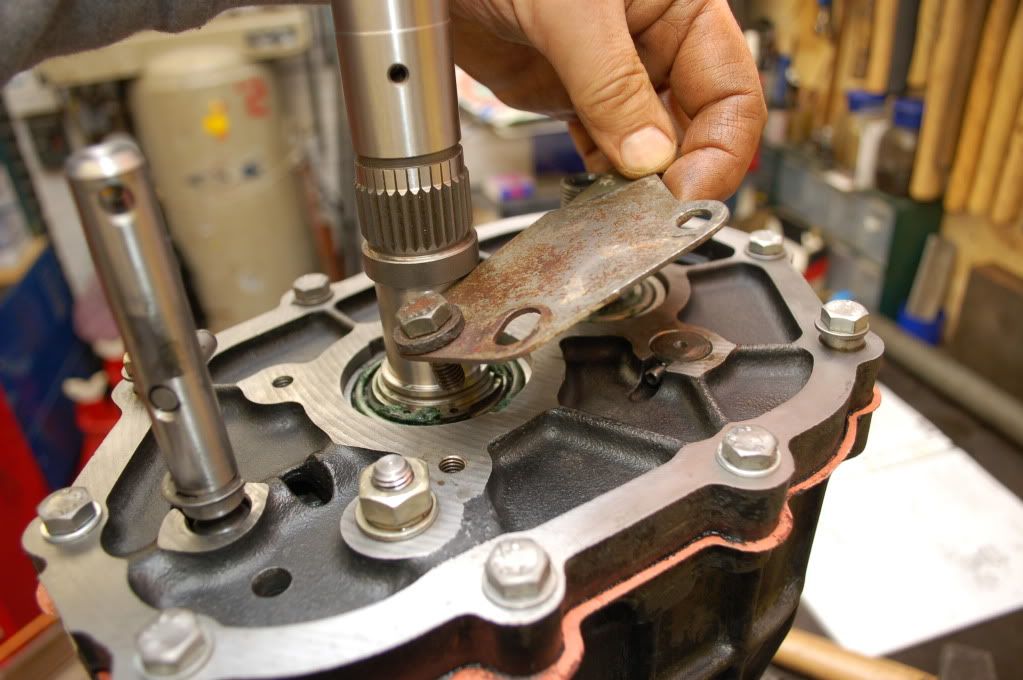
I held the box in the vice gripping onto the layshaft support bar I’d just fitted.
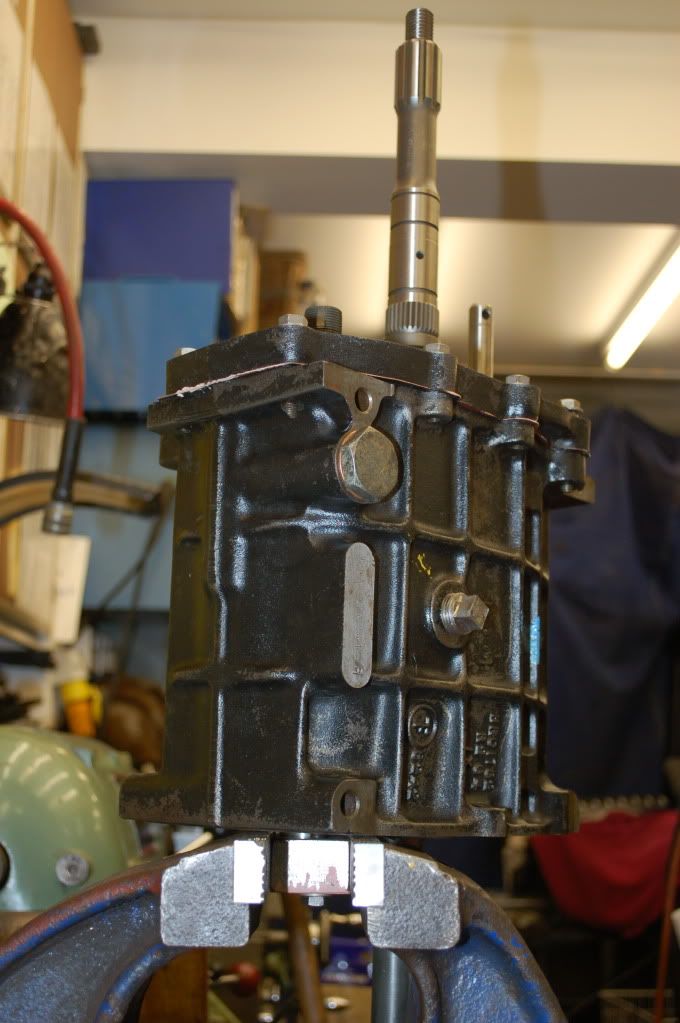
You now have to drive 5th gear onto the end of the layshaft. So needed to make a tool to help.
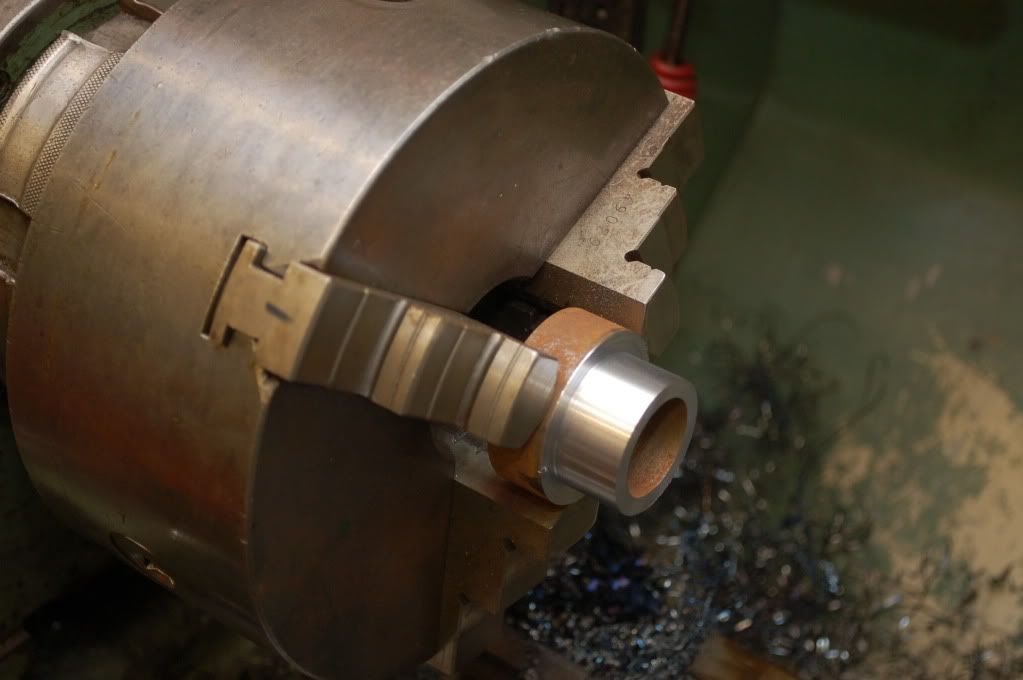
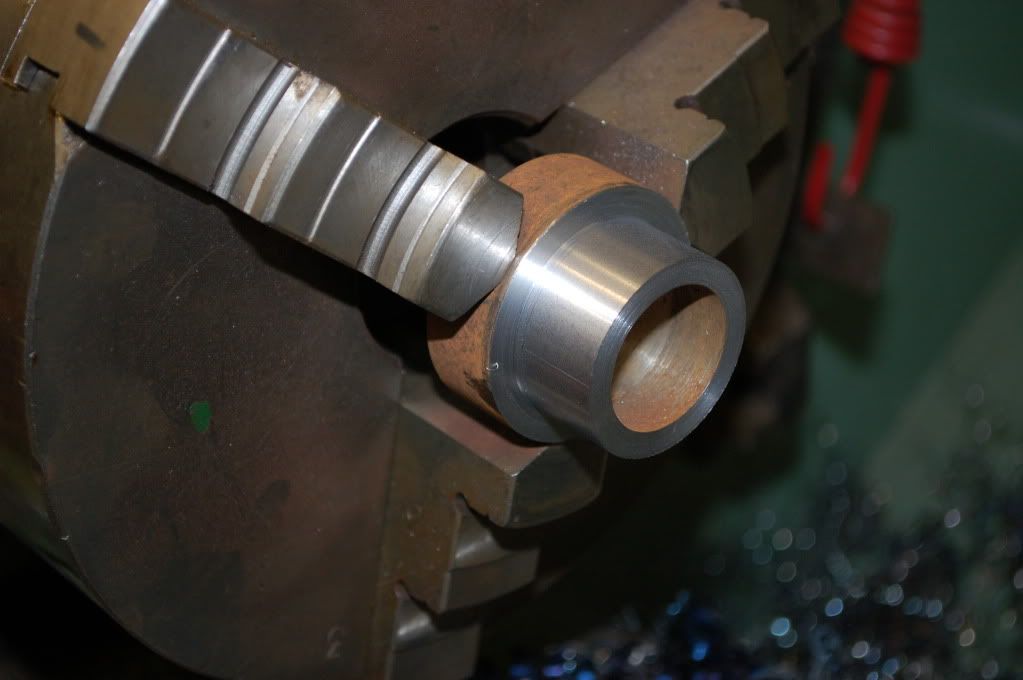
Used an old bearing race and a bit of pipe fitting. The bit above is a plug to go in the end of the pipe collar (to bash with a 3lb hammer!!!).
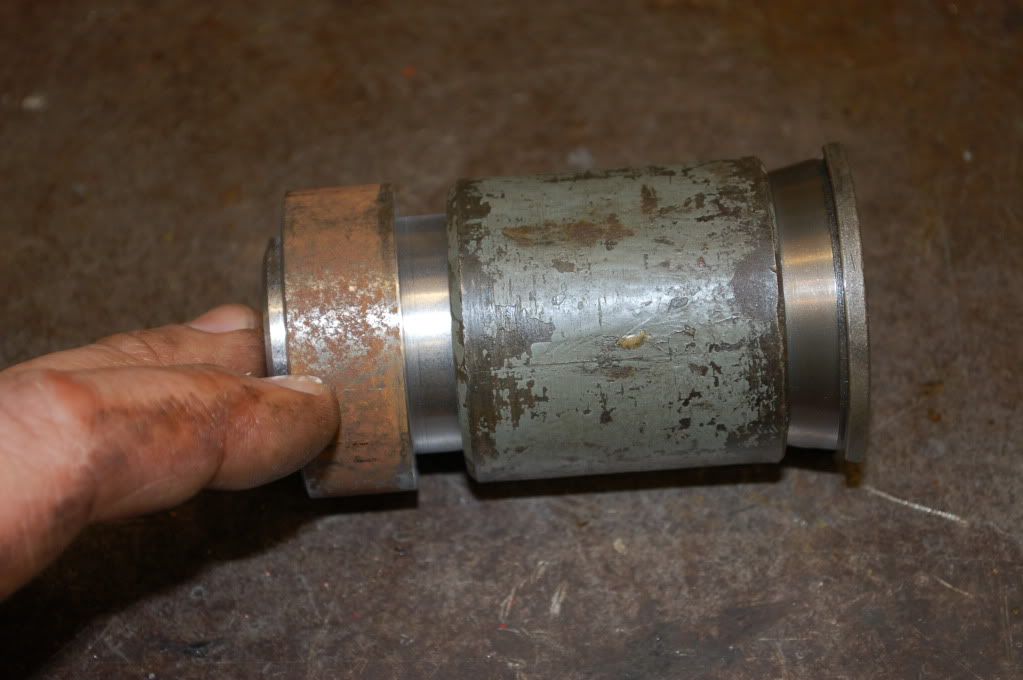
Heat gear.
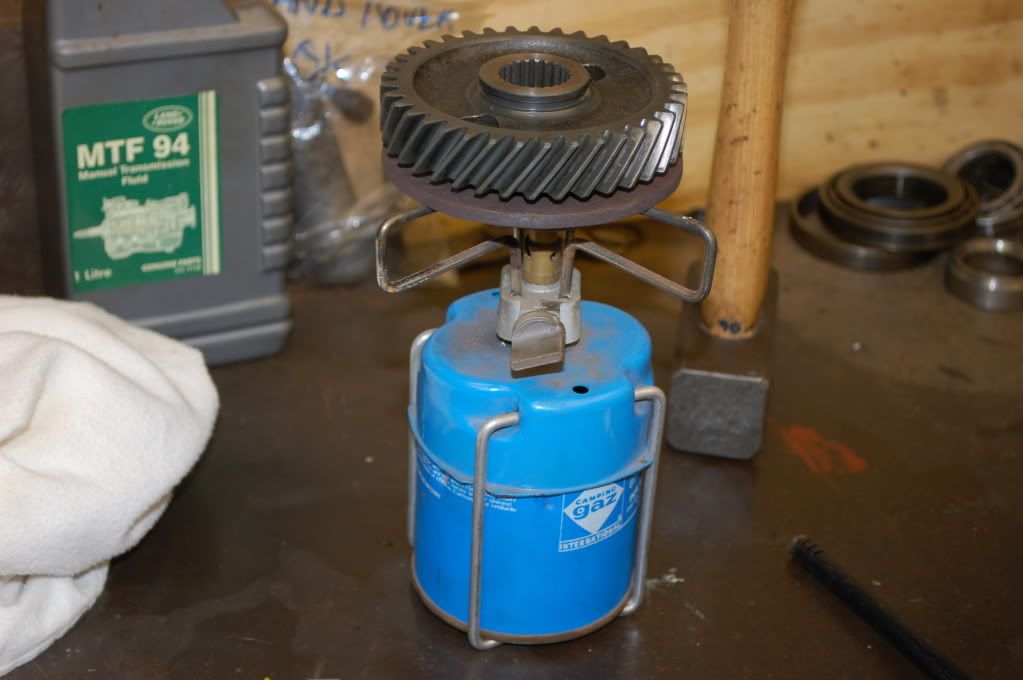
Bash the bugger home! You’ll see I fitted a bit of pipe over the mainshaft. Just in case one of my heavy hammer blows went off course – didn’t want to make a big dent in my new shaft!
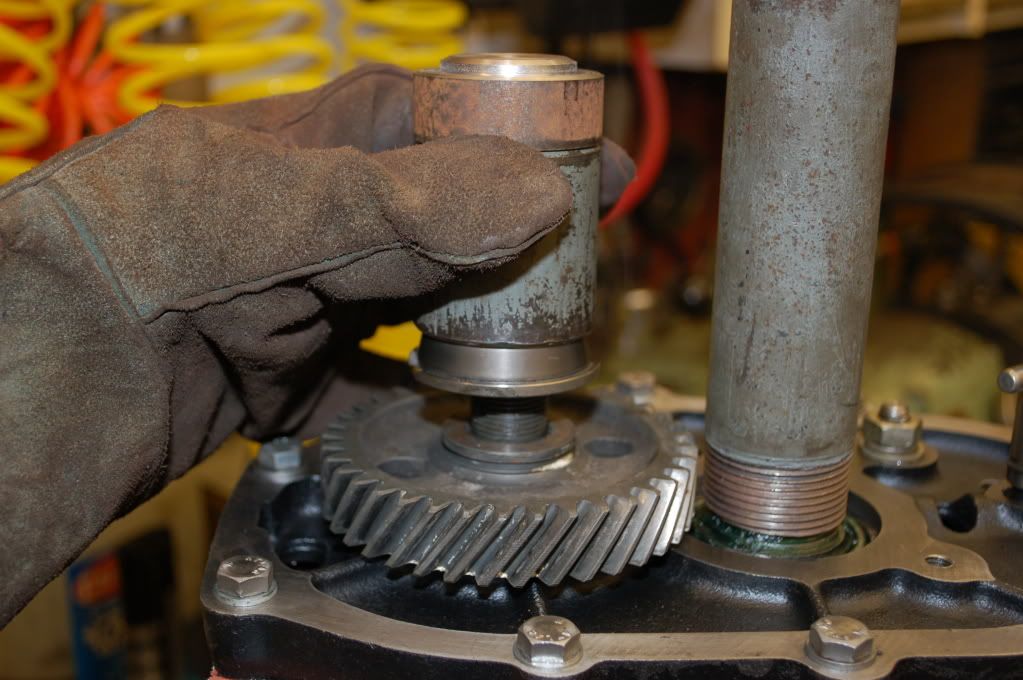
As I didn’t have a new retaining nut I took a few thou off the original so it would stake up into new metal when re-fitted. Clocking the nut in the chuck before machining.
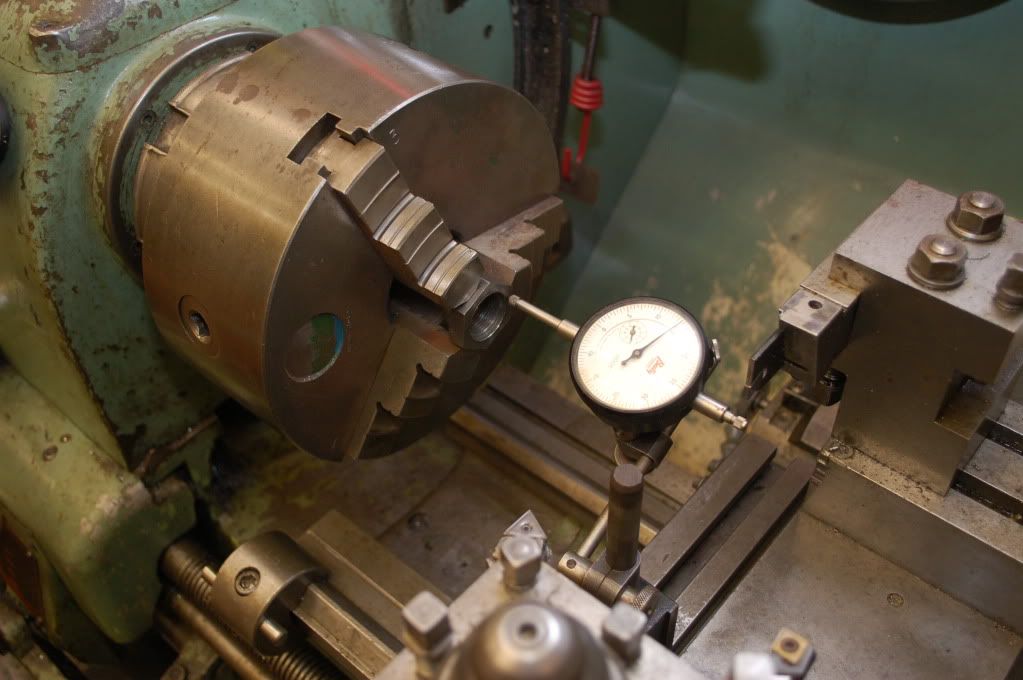
Machined.
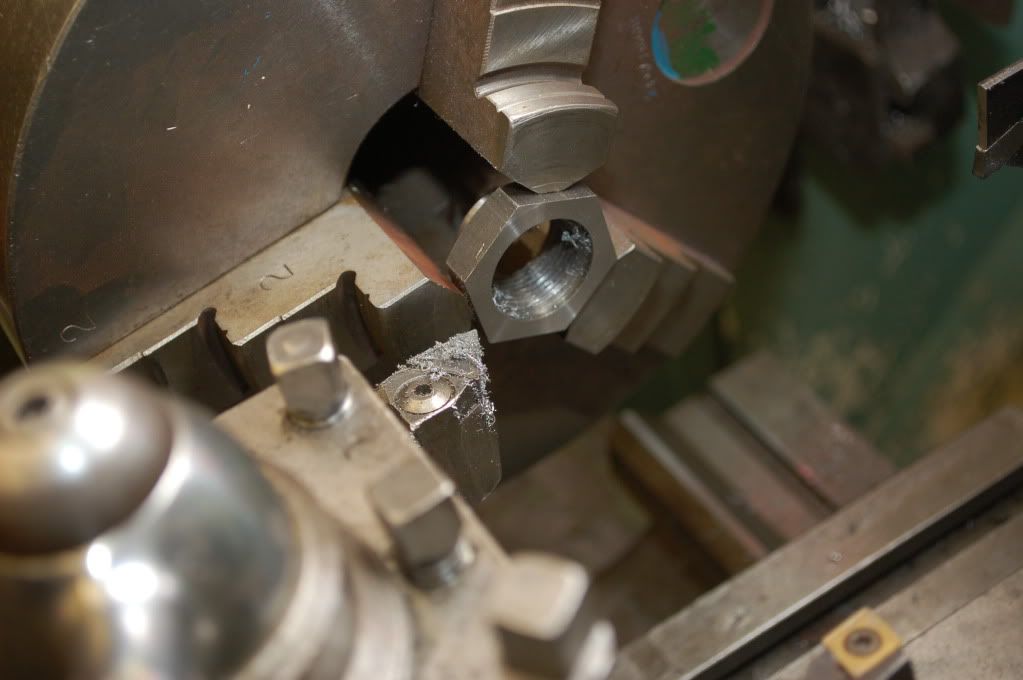
Fitted – loosely.
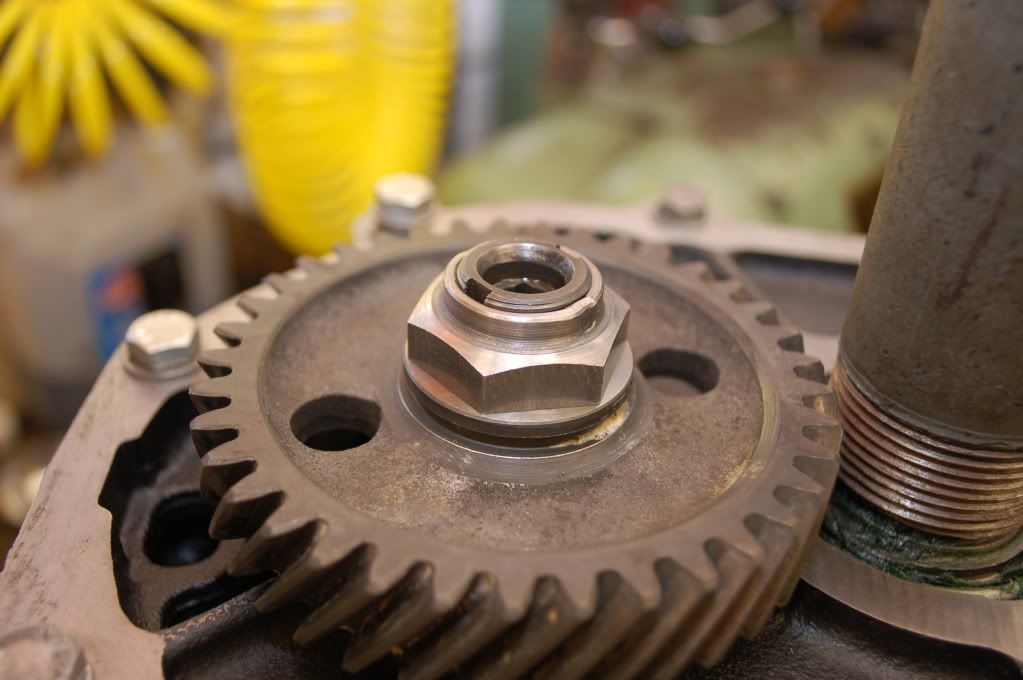
Fit 5th gear bearing cage.
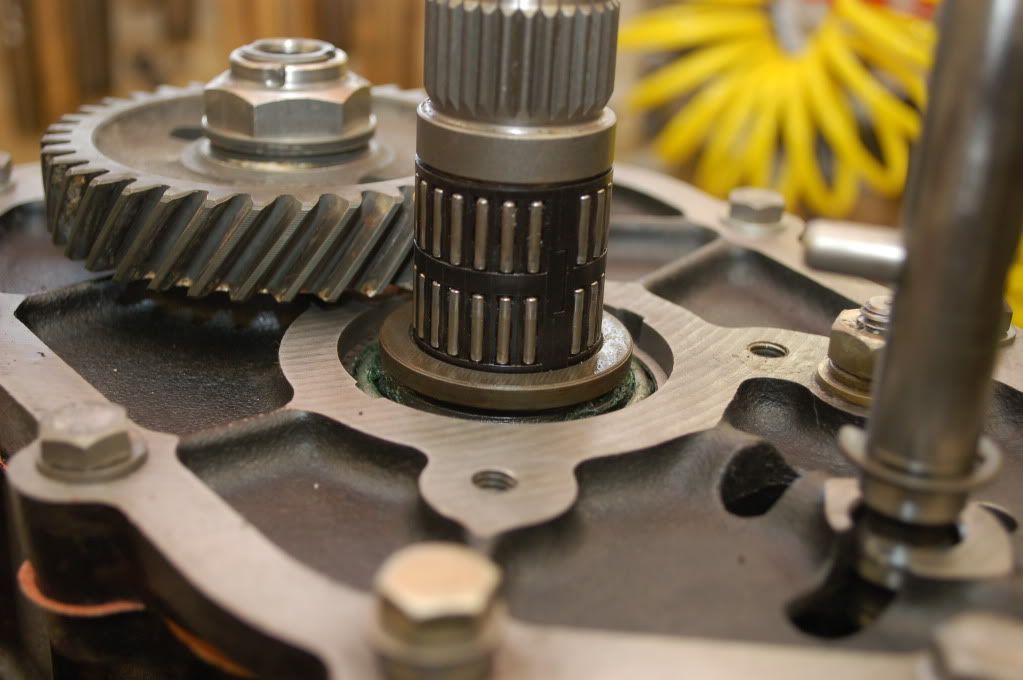
Followed by assembly.
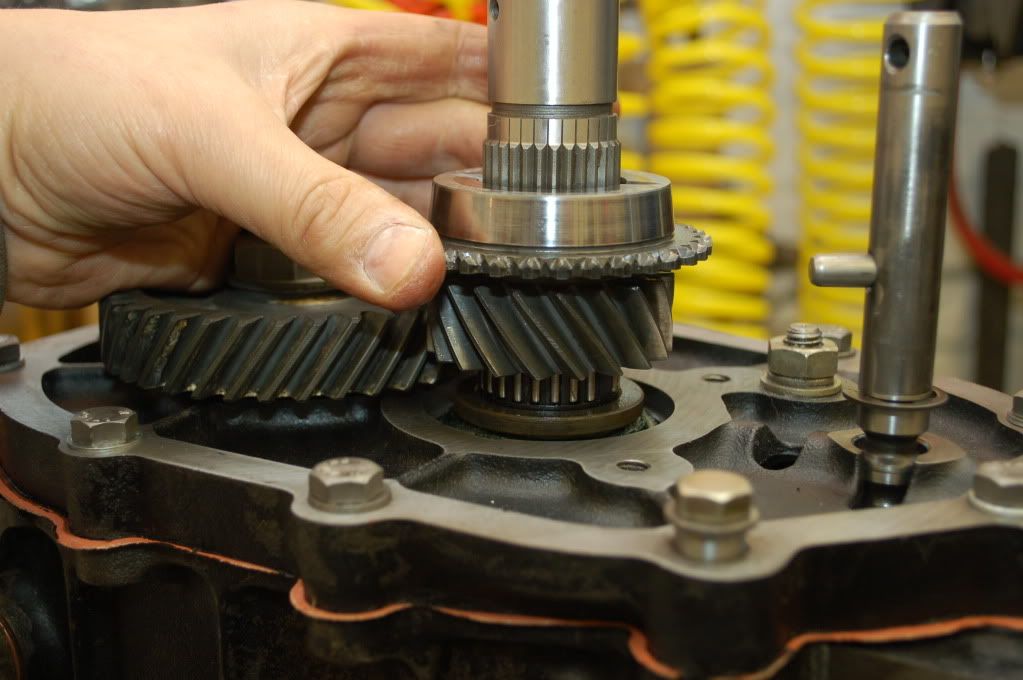
And baulk ring/synchro assembly.
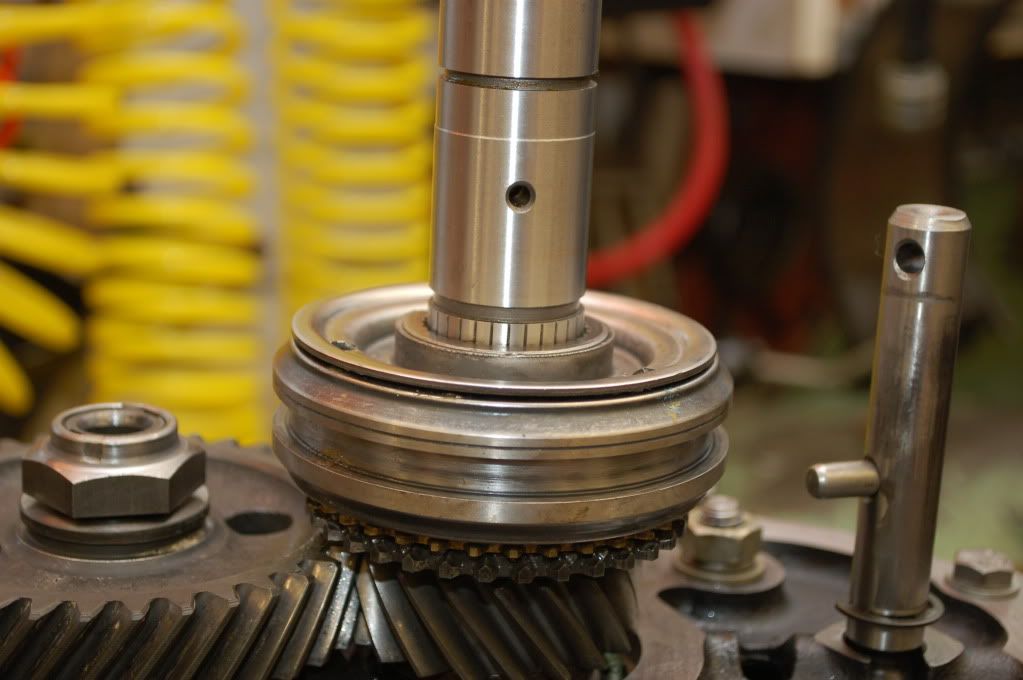
Fit 5th gear ‘retaining’ tool and tighten nut to 230Nm.
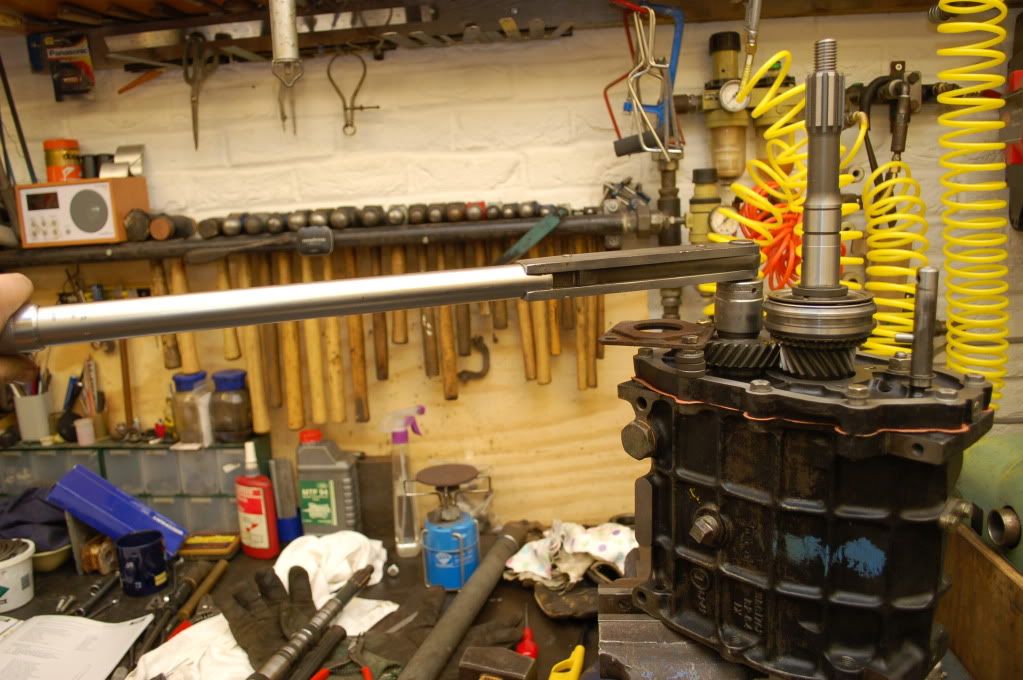
Measuring the inner member synchro clearance (up to 0.002â€). Use selective washer to achieve correct tolerance between it and the circlip.

Stake nut.
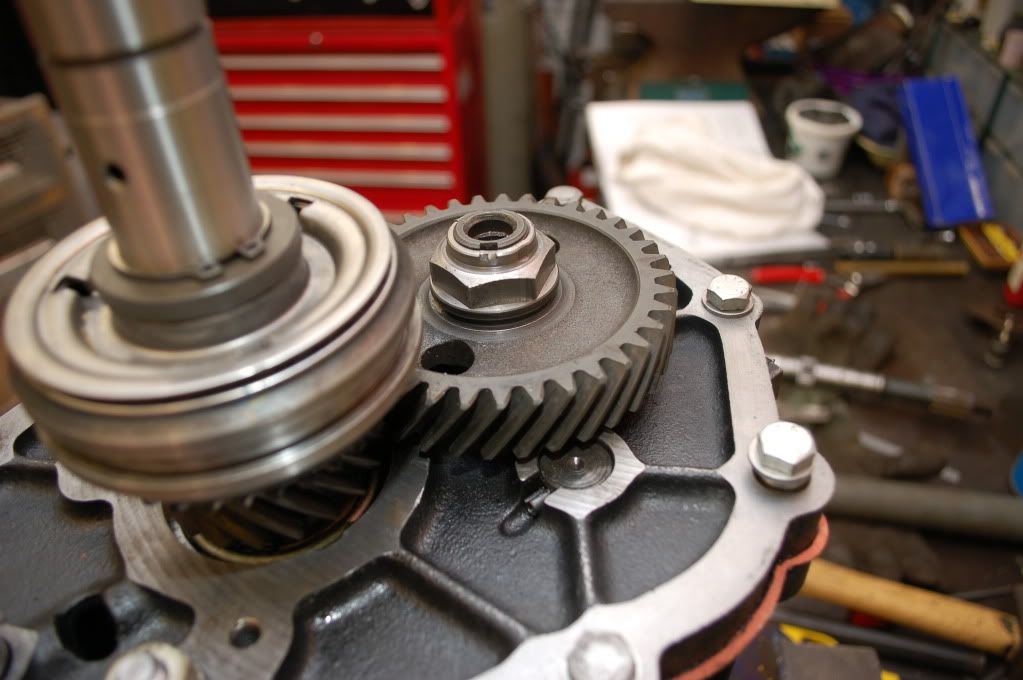
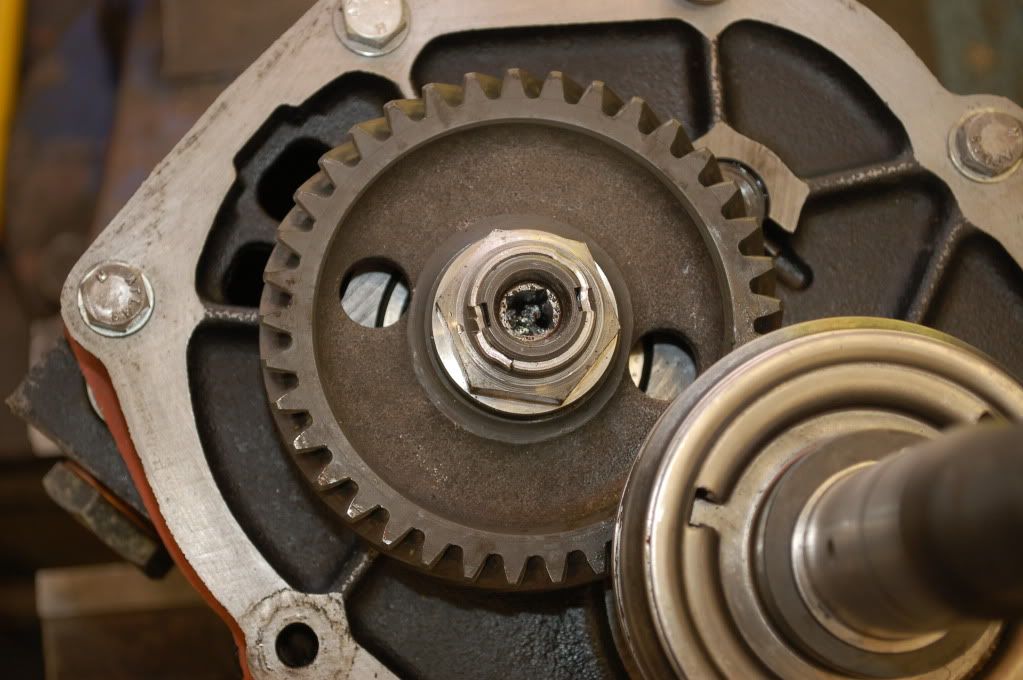
Fit 5th gear selector fork assembly.
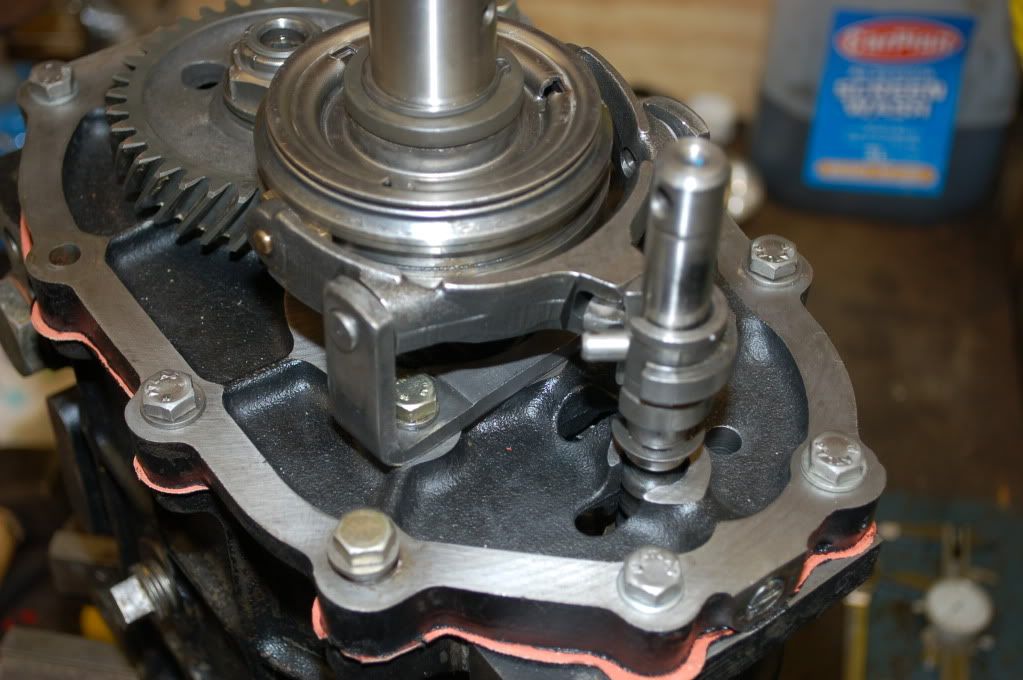
Fit oil pump drive square to end of layshaft.
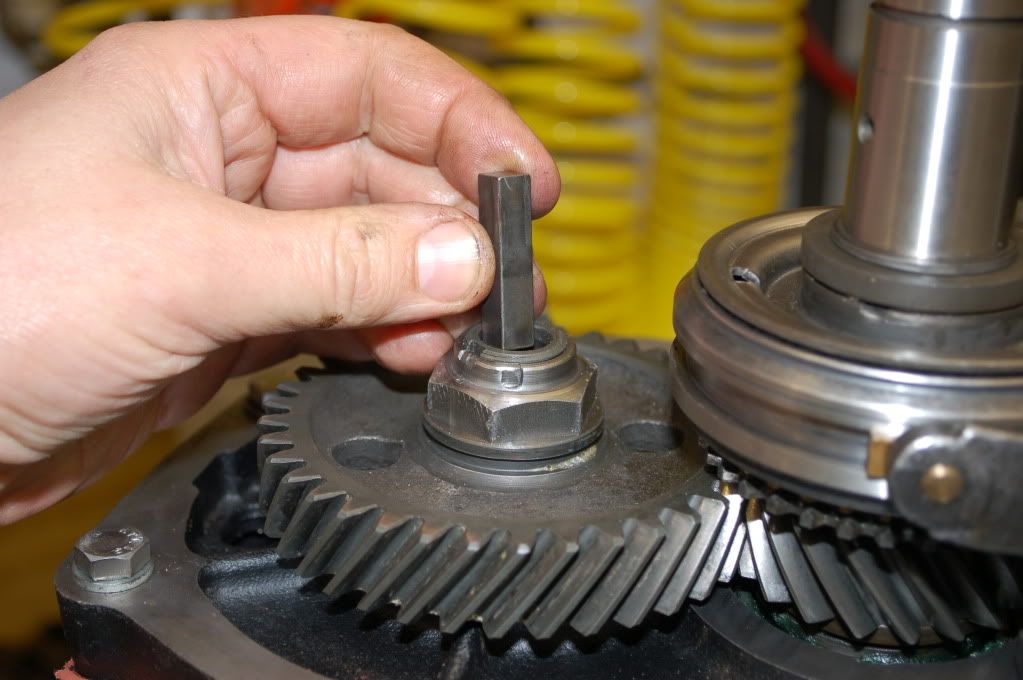
New and old oil pump gears. These gears were the best I’ve evere seen. Other TR7 boxes I’ve stripped have has bits of swarf and chunks missing on occasion.
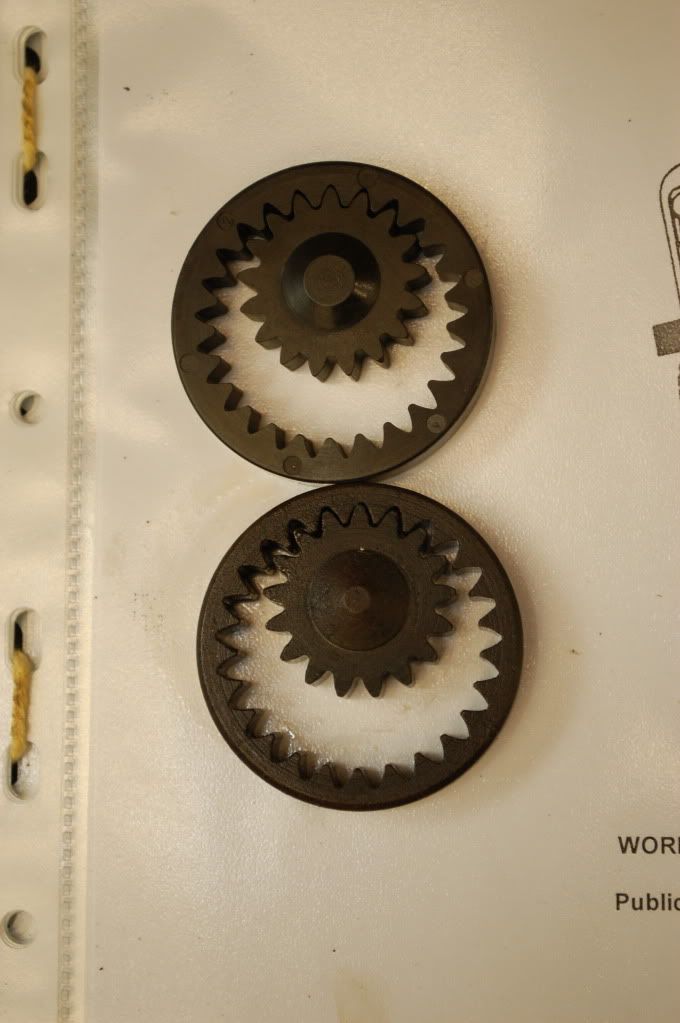
Fit gears to casing.
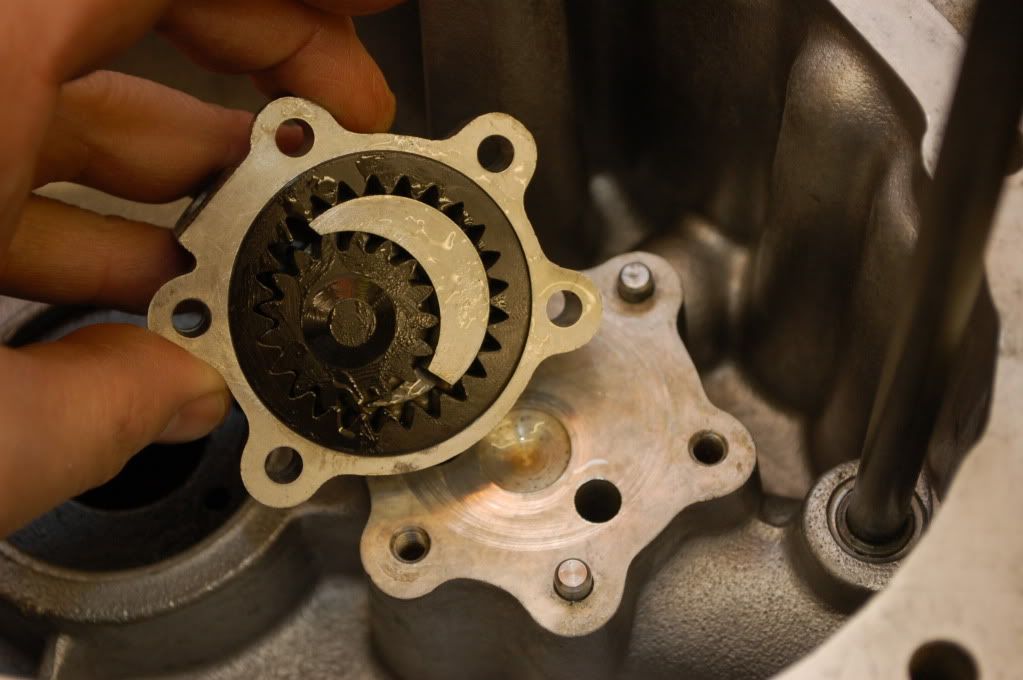
Line up oil pump square drive with the oil pump. Fit gasket and offer up casing.
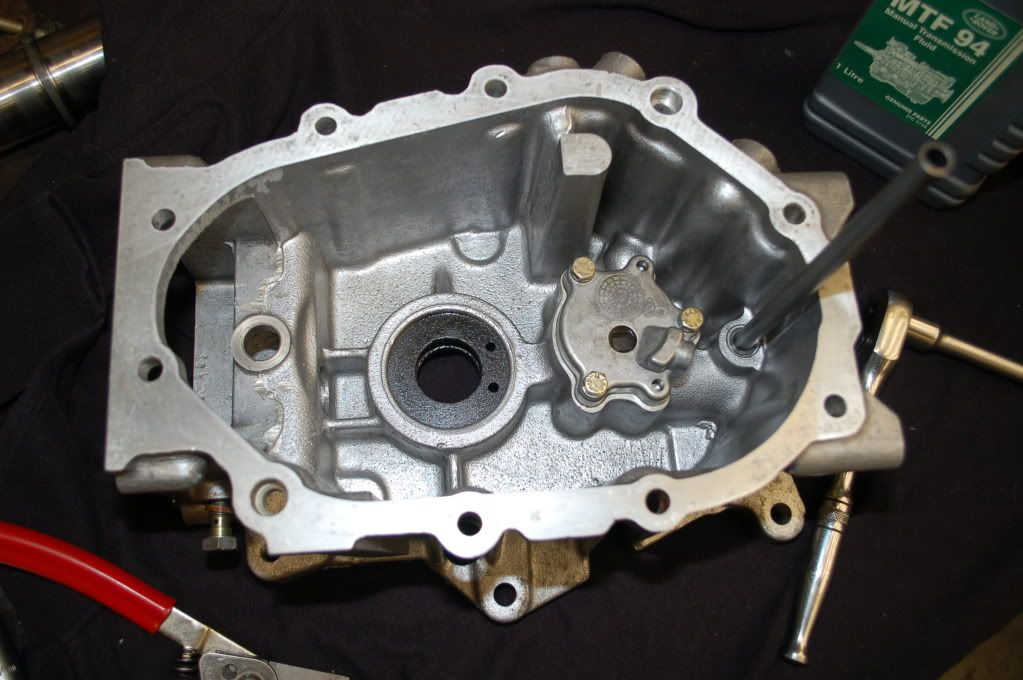
[img]http://i422.photobucket.com/albums/pp305/shauniedawn/LT77%20Gearbox%20Overhaul/DSC_8721.jpg?t=1265496119[img]
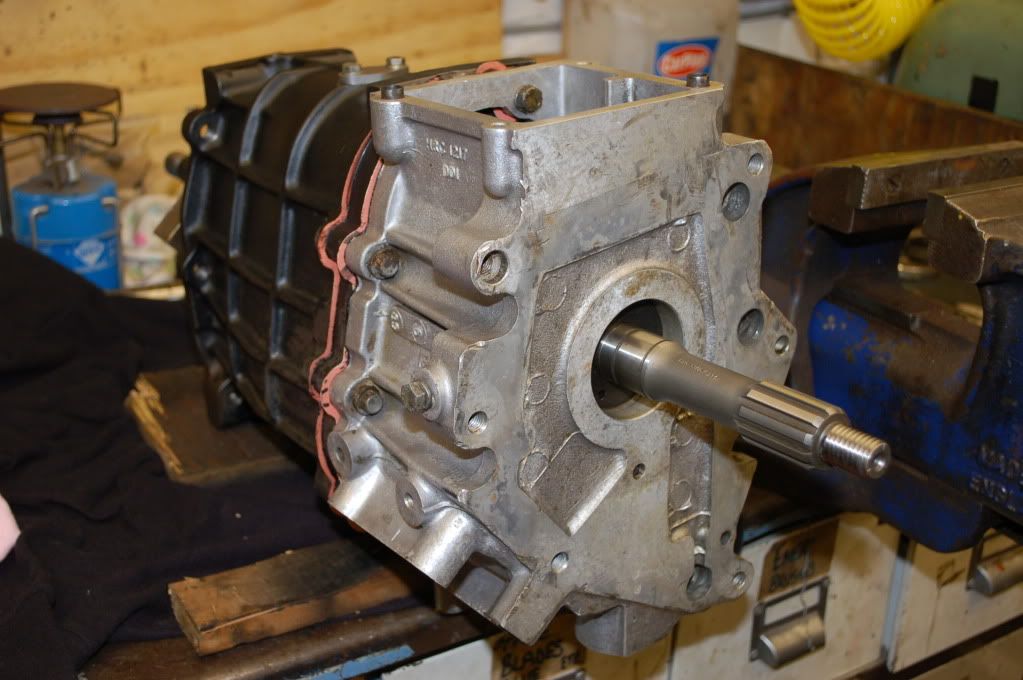
Remember the TR7 casing is a bit different with a support roller bearing and the output flange, which is held on with a nut. Here’s a flange holding tool I made to hold it whilst the nut is tightened.
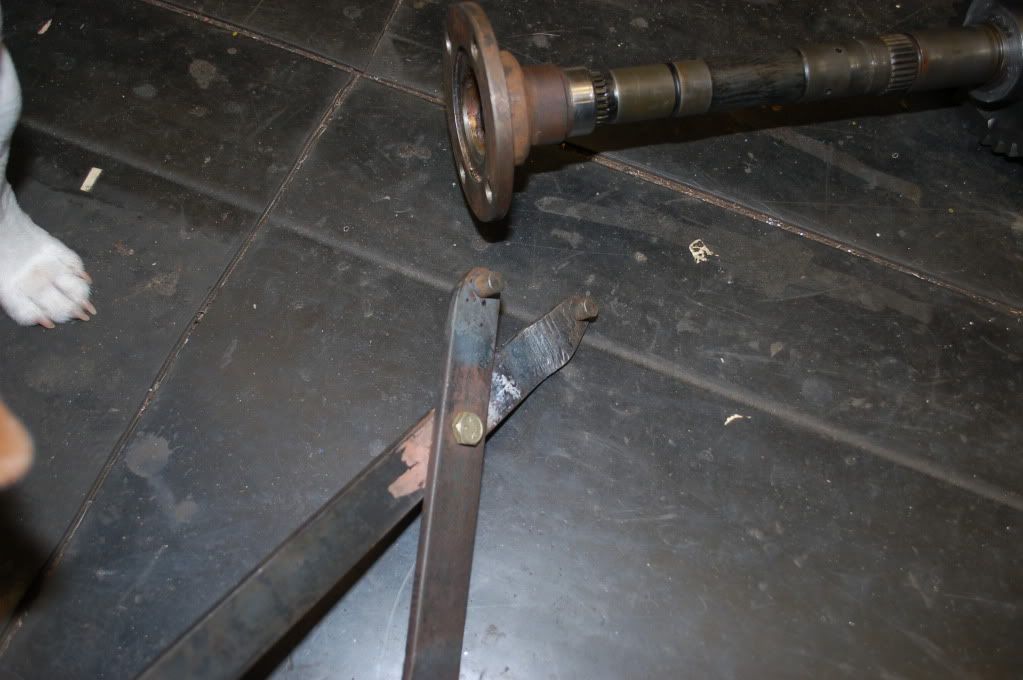
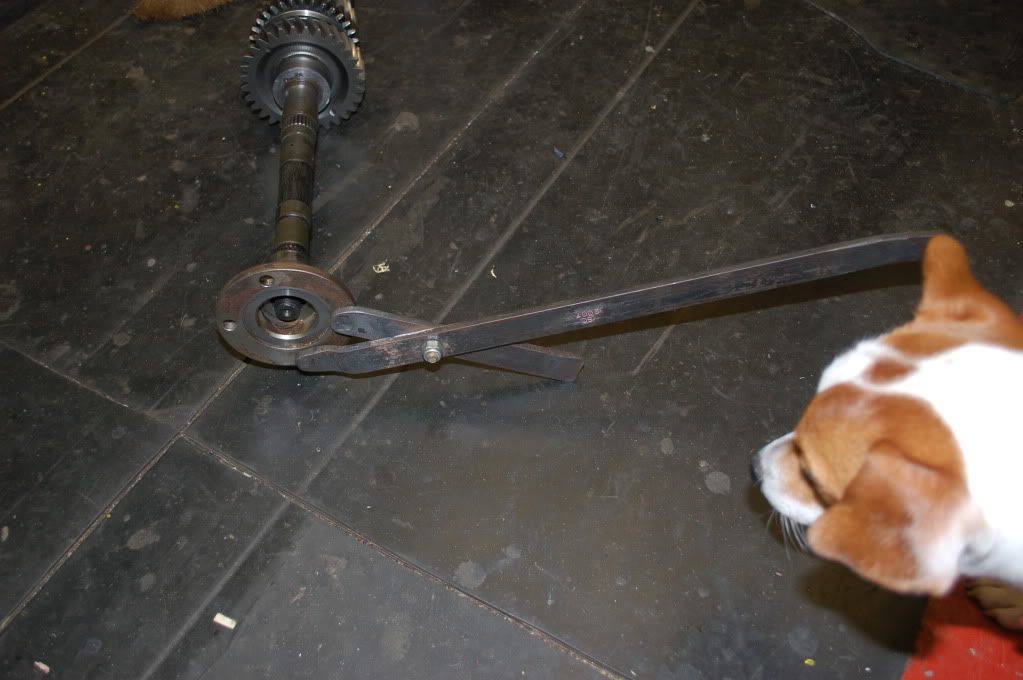
But the Land Rover is a bit different as it has a collar pressed onto the mainshaft that seals the casing. The inner is sealed with an o-ring, the outer of the collar direct onto a regular oil seal.
Fitting o-ring.
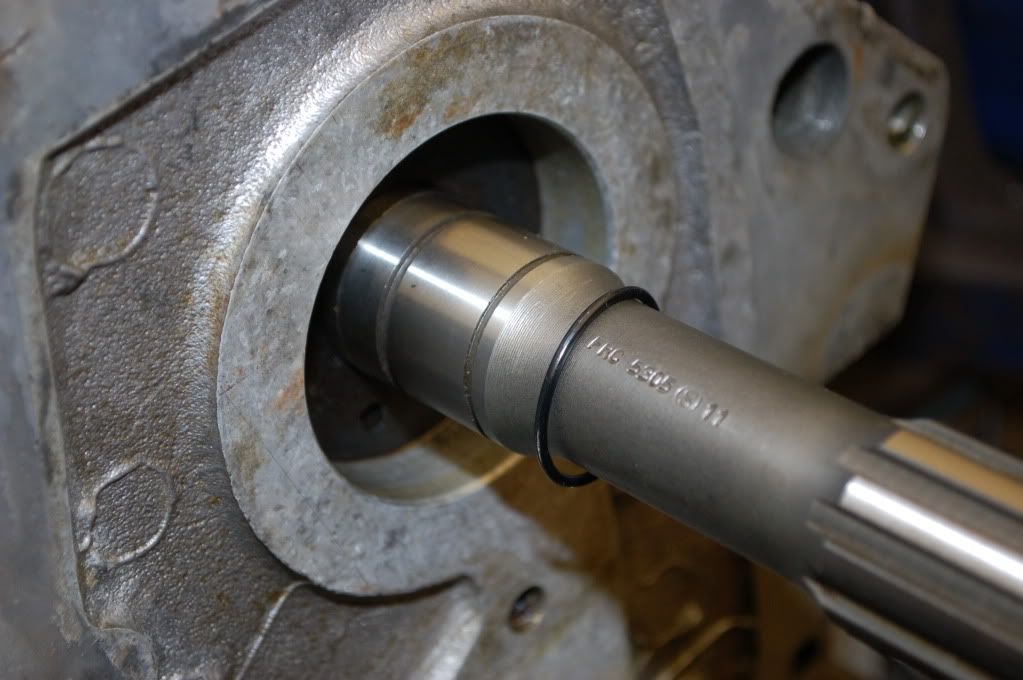
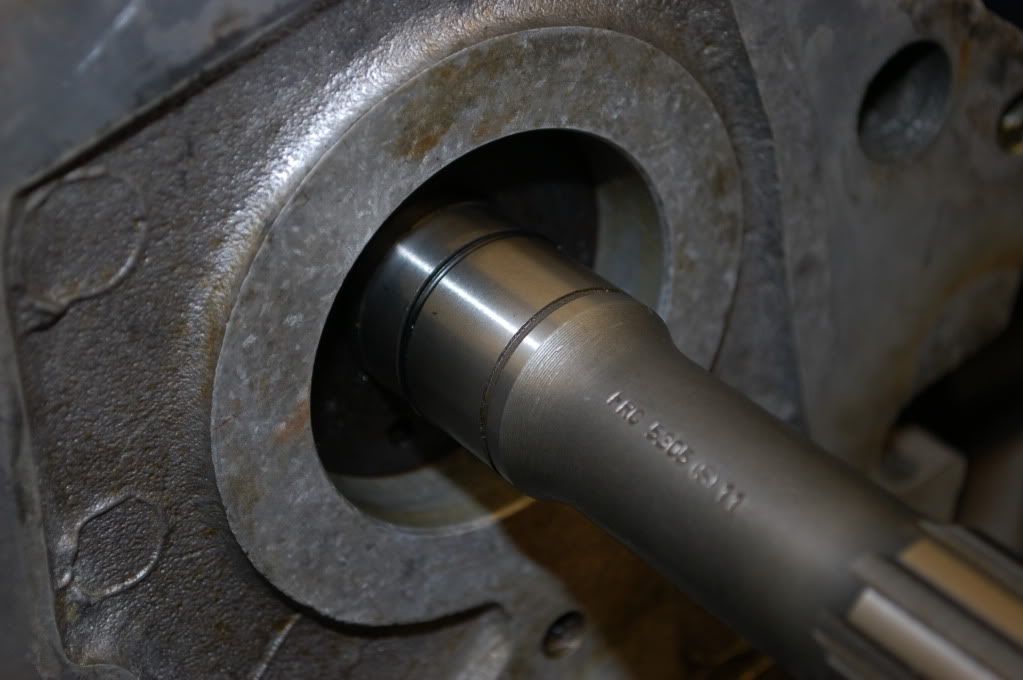
Fitting oil seal.
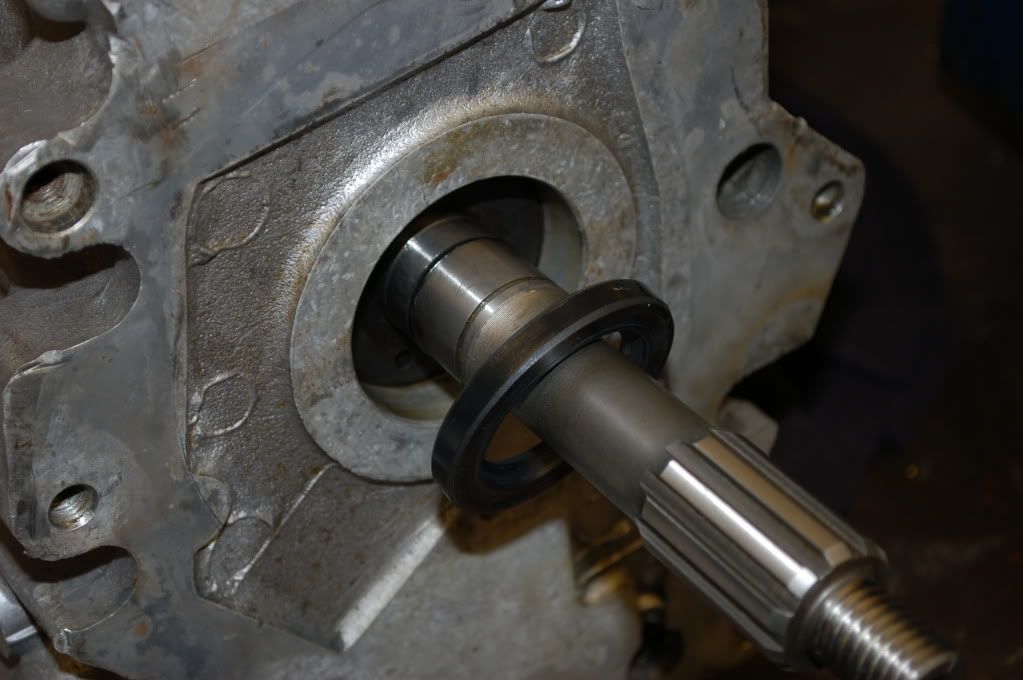
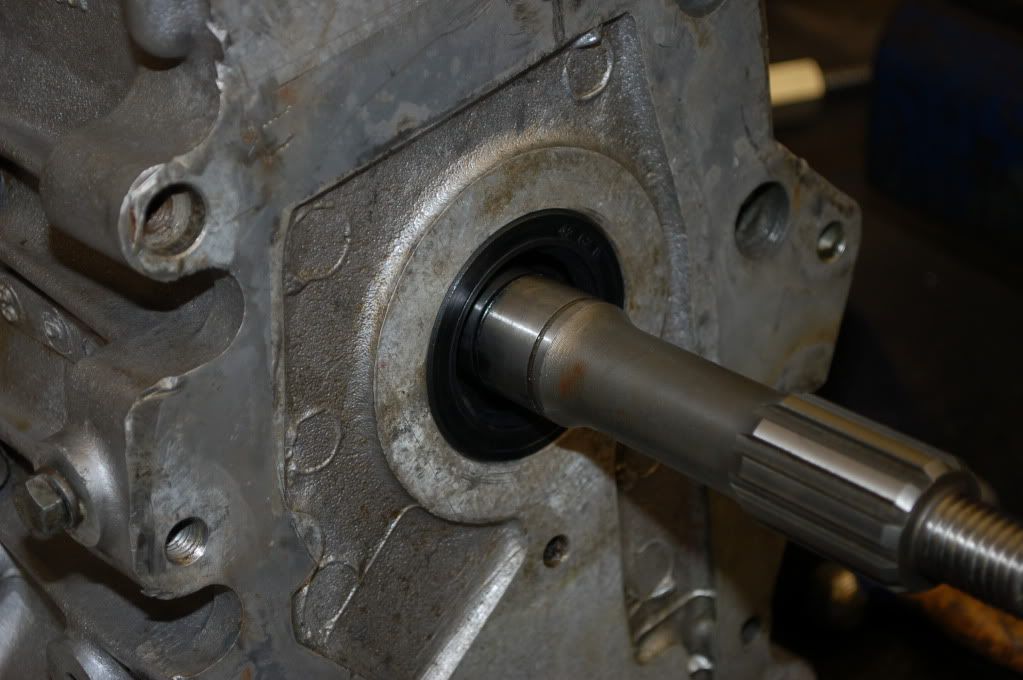
Here’s the collar.

Now. I didn’t want to heat the collar to get it on as I would be likely to damage either the seal or the o-ring or both. So a different approach was needed.
Here’s my assembled bits and bobs to do the job.
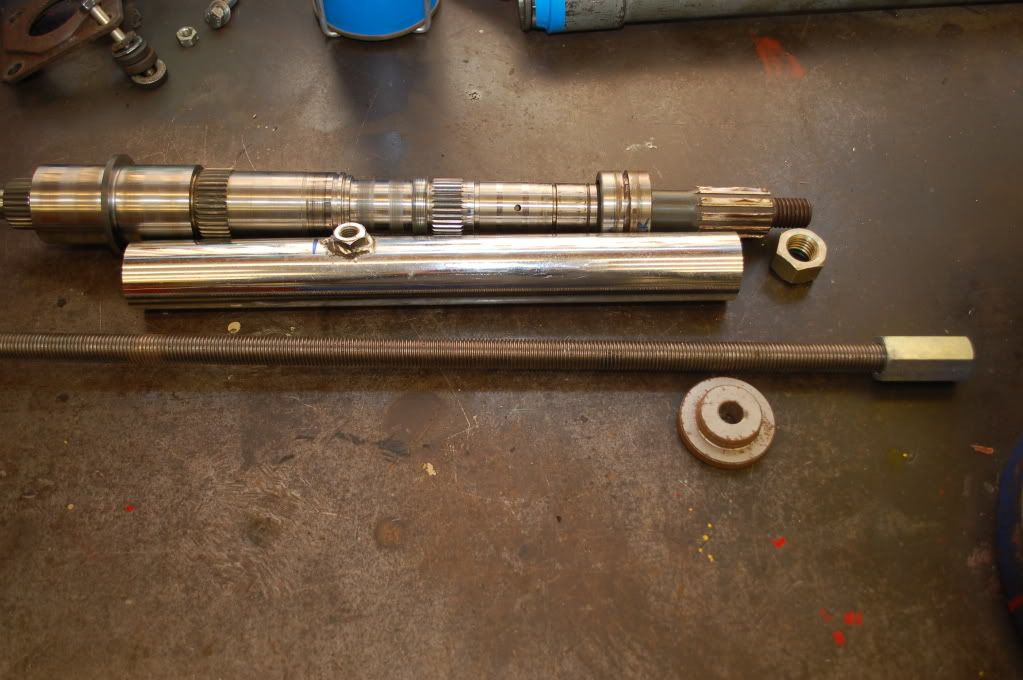
Part off bit of scrap tube.
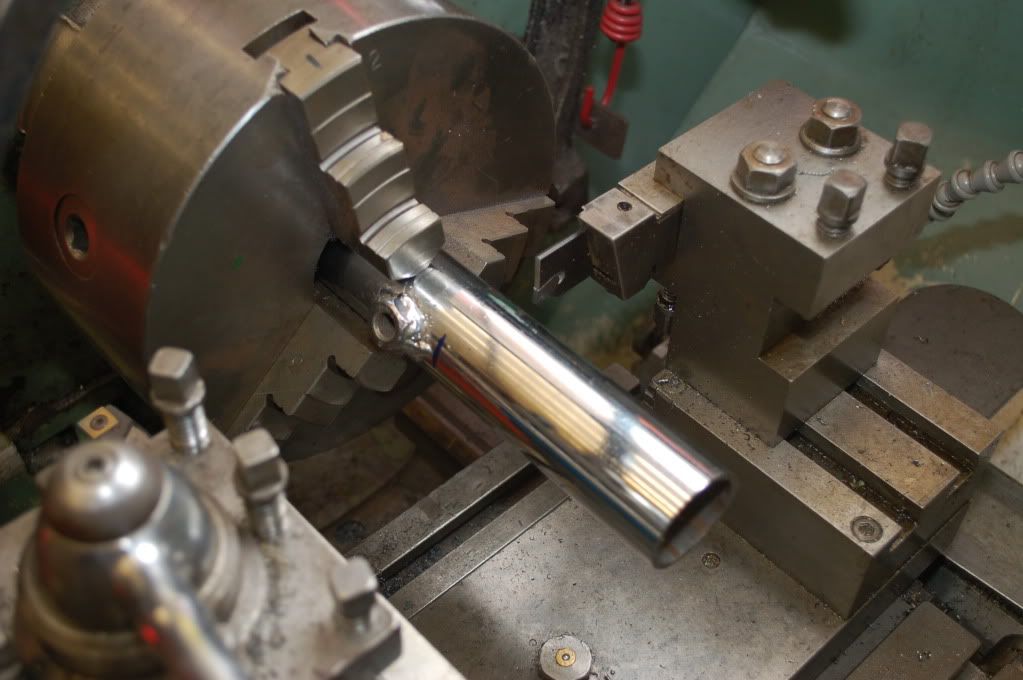
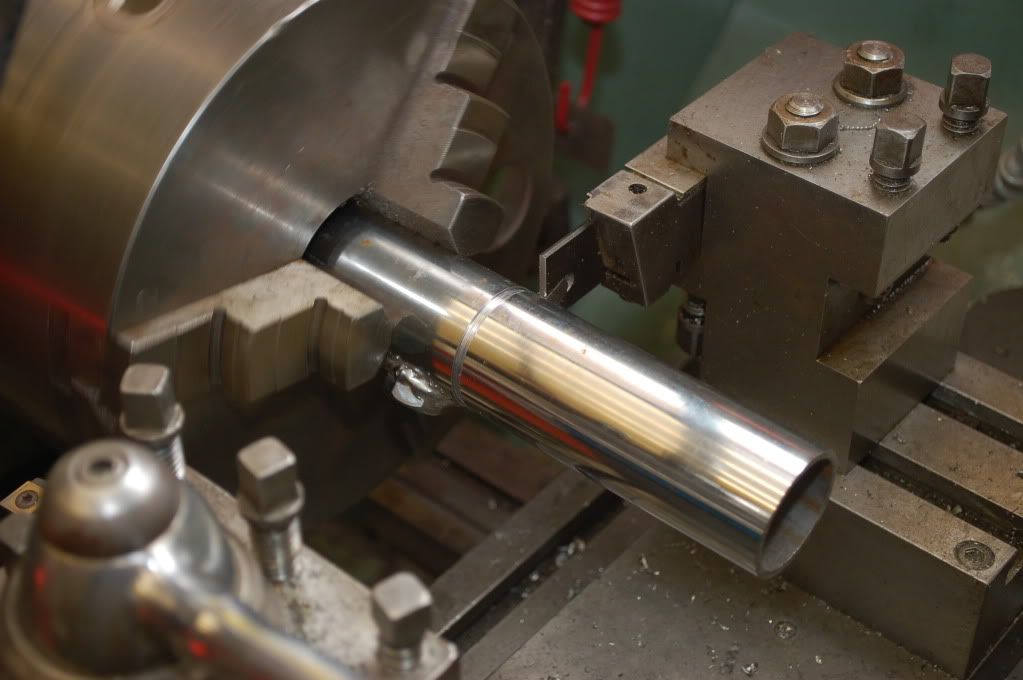
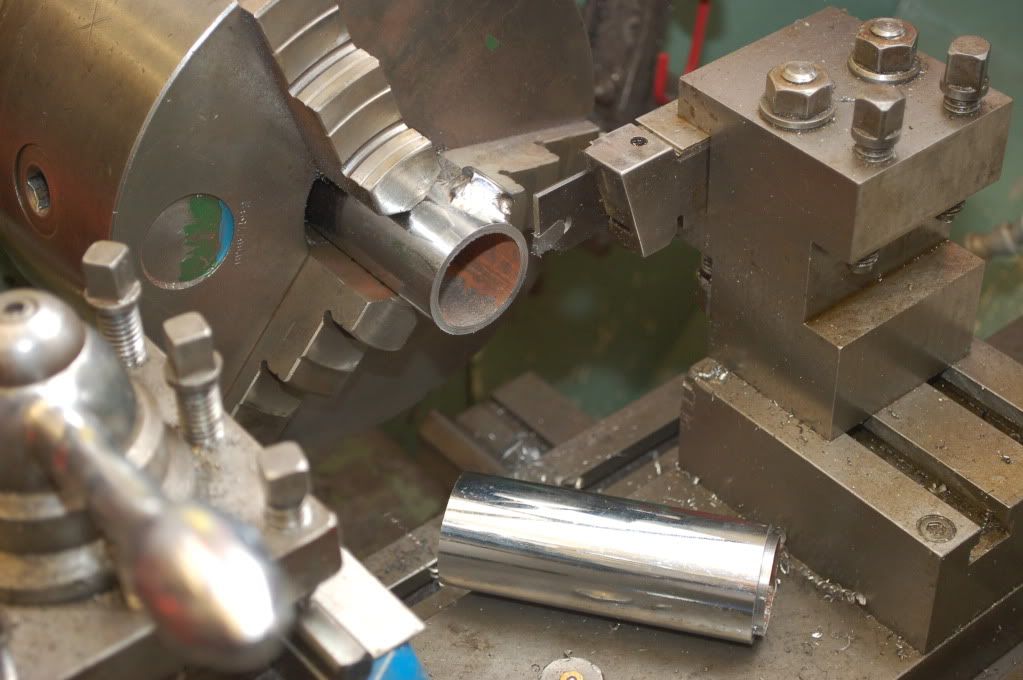
As this was chromed, needed to machine a bit of the chrome off where I was going to weld.
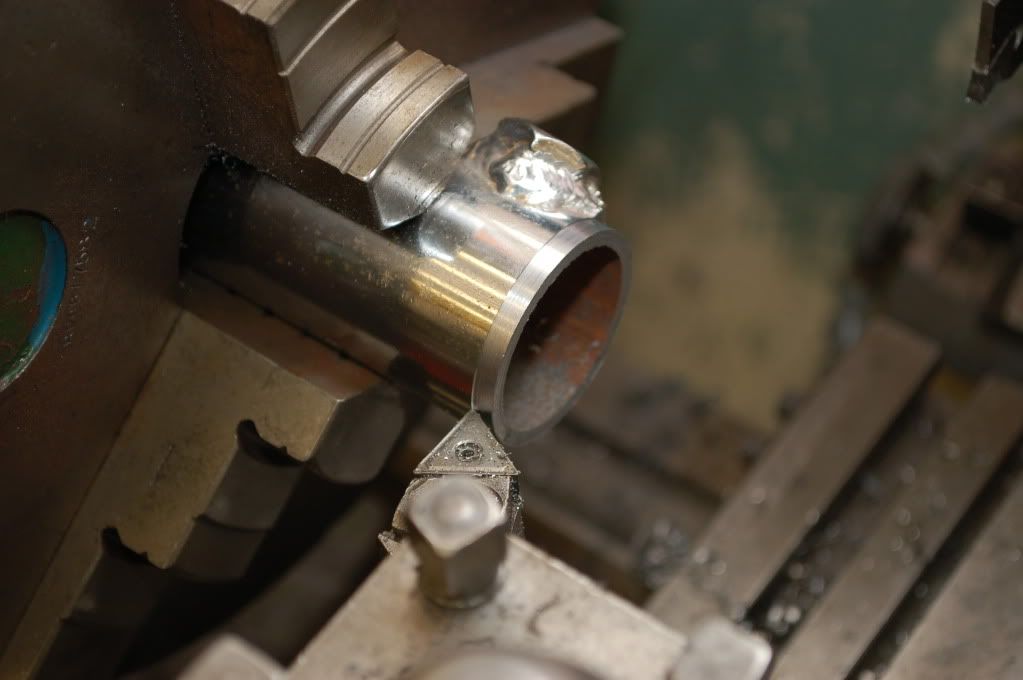
Machining an ‘end’ for the tube.
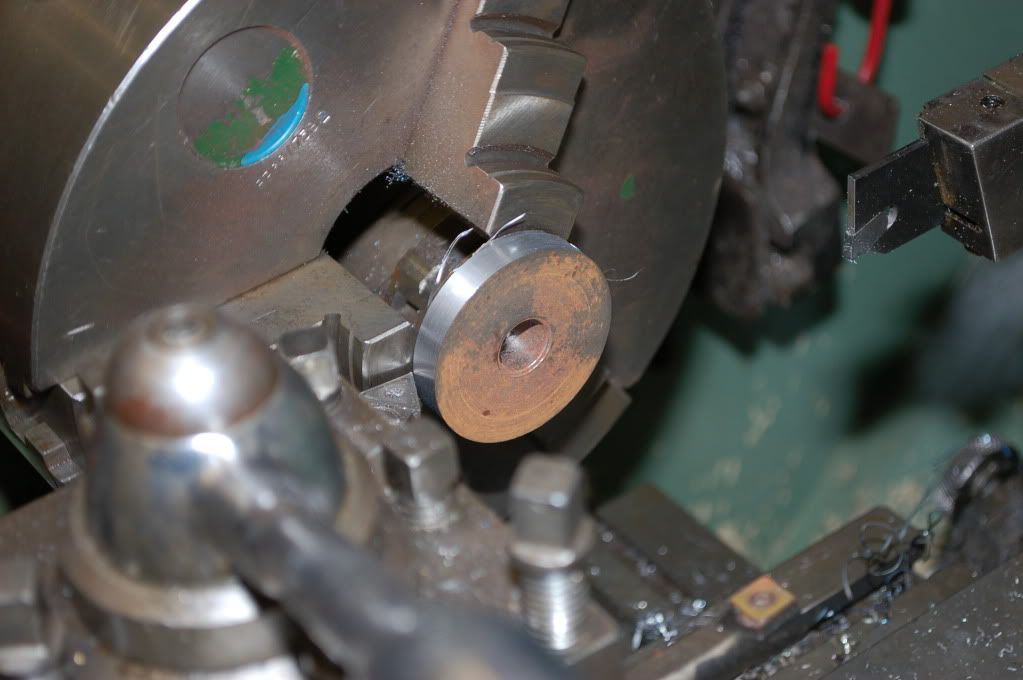
End fitted into tube – you can just see the join.
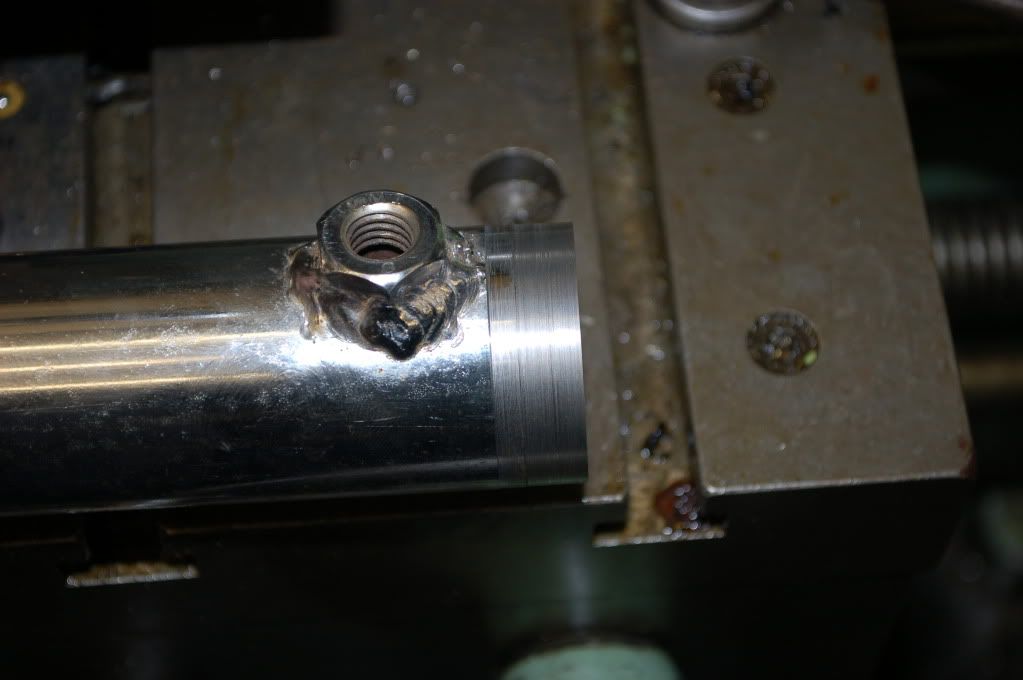
This nut is to pick up on the threaded end of the mainshaft. It’s an odd size at 18mm. Machined off nyloc bit.
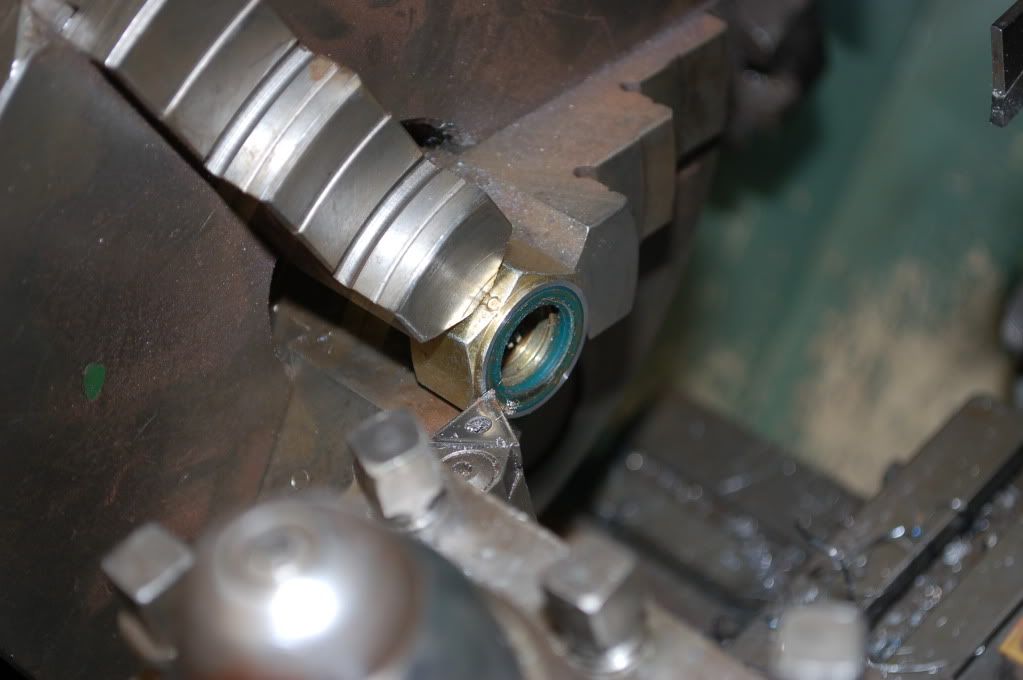
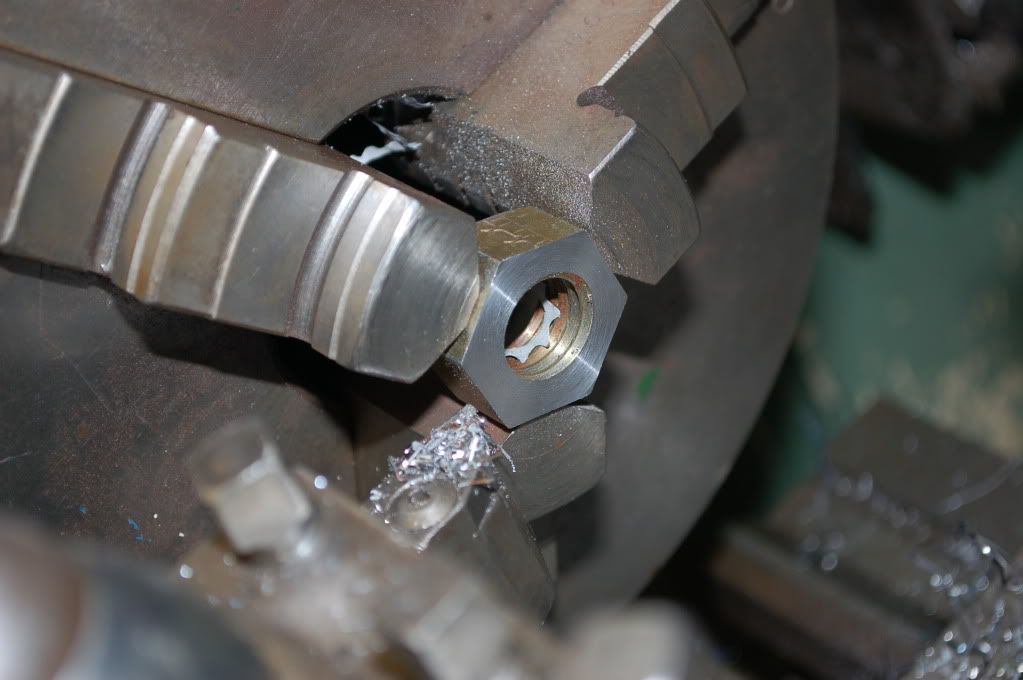
Weld nut onto end of studding.
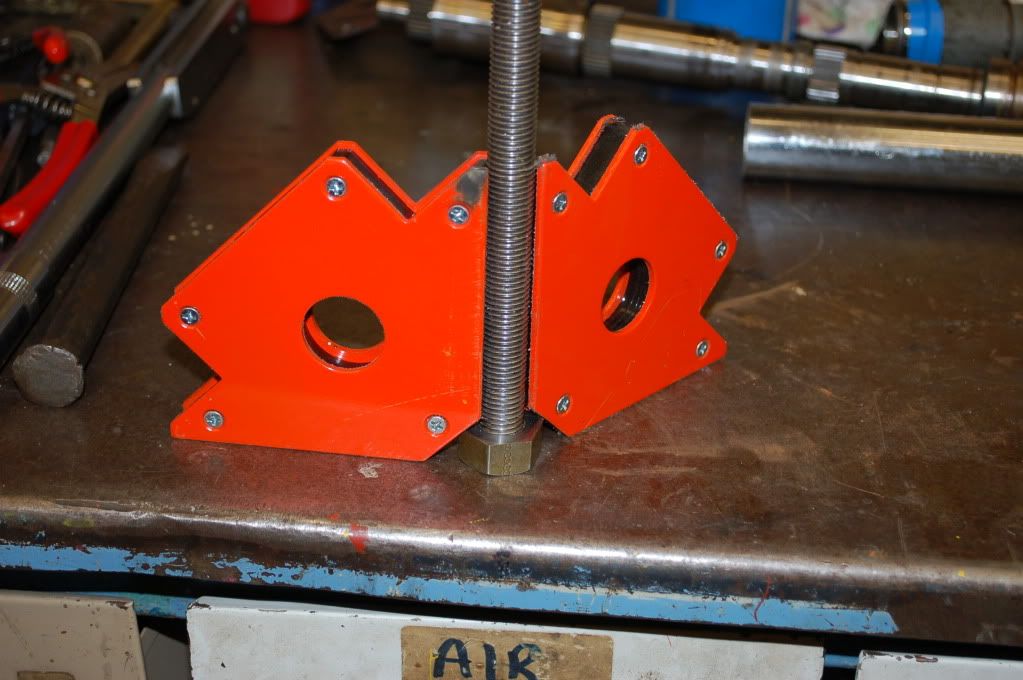
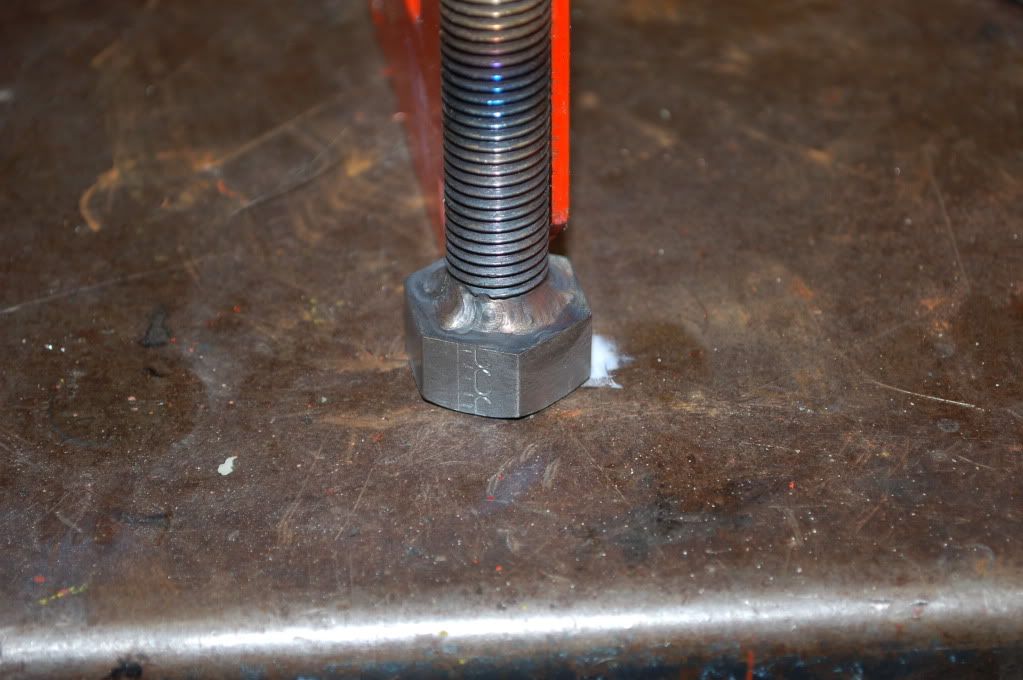
Weld end into tube.
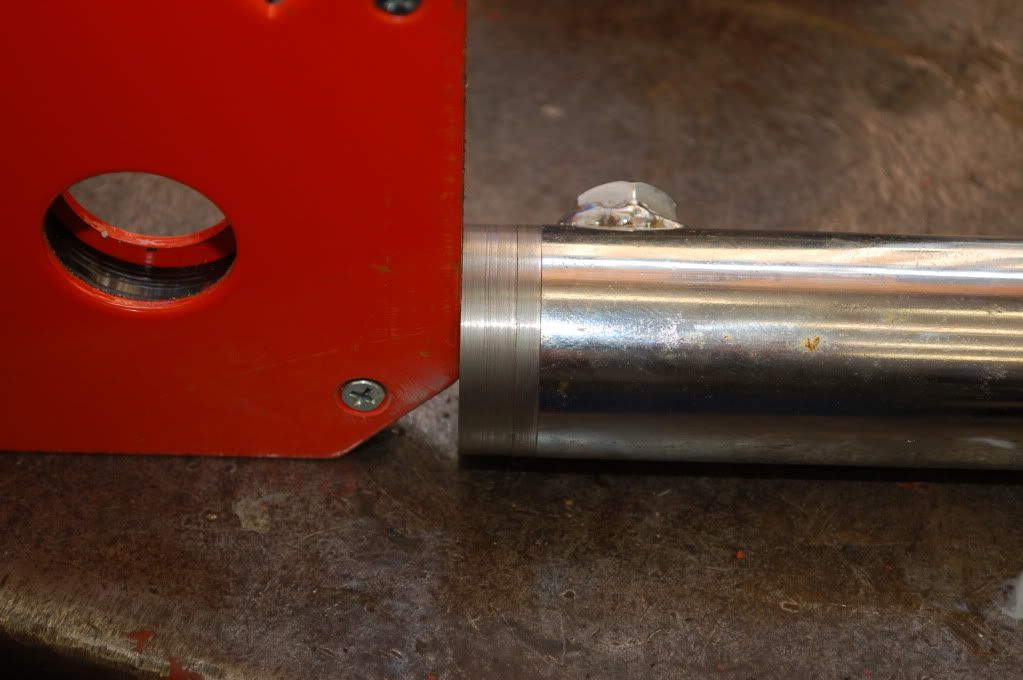
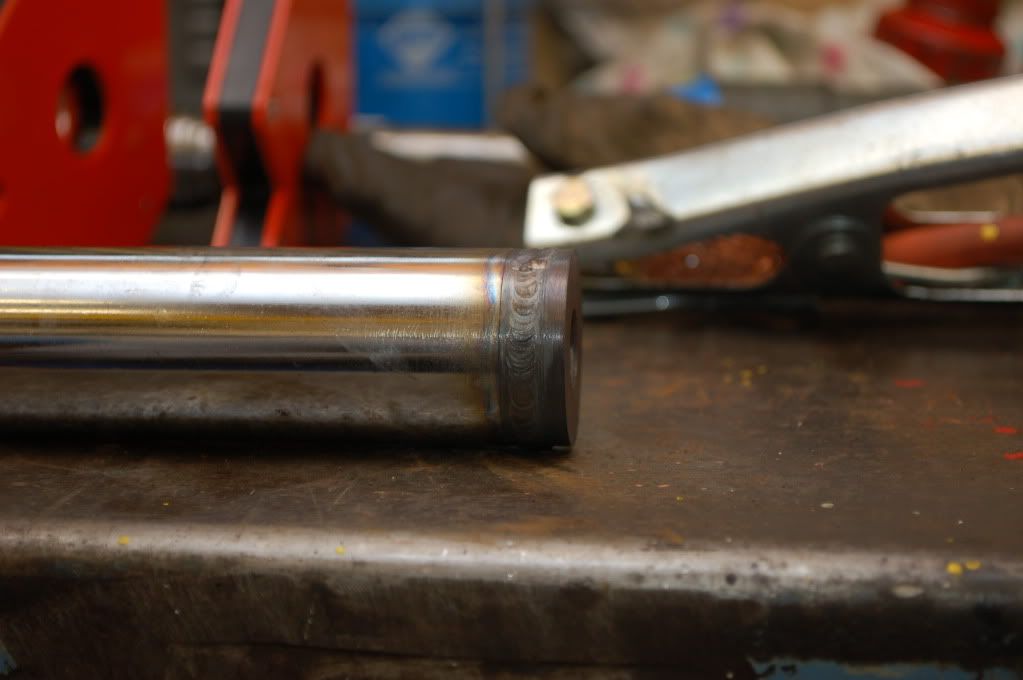
Drill clearance hole for studding to pass through.
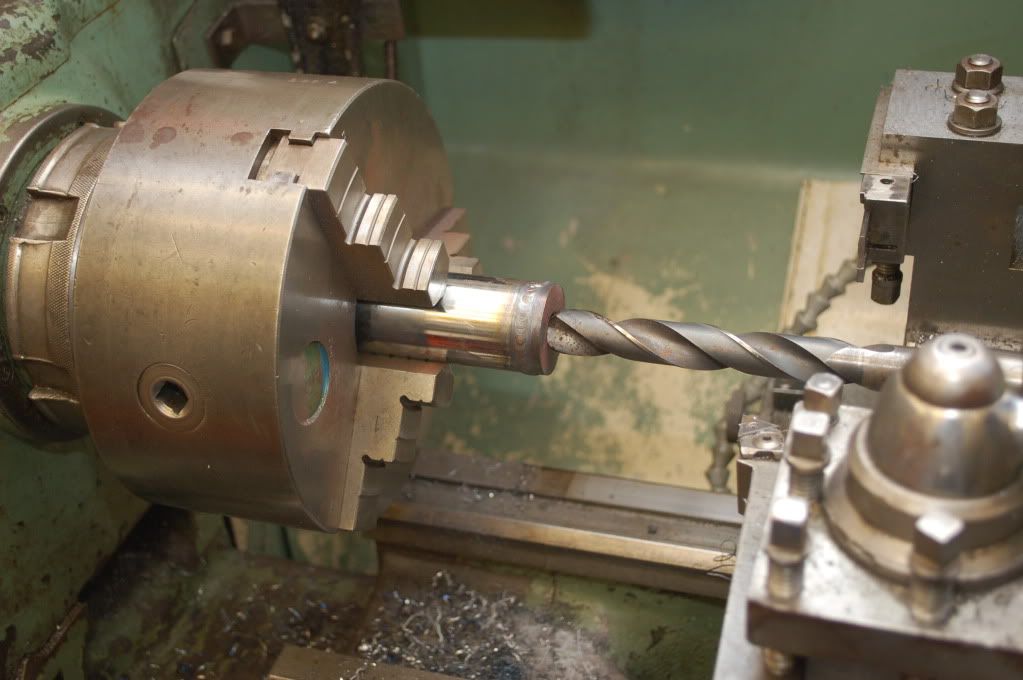
Take off rough edge.
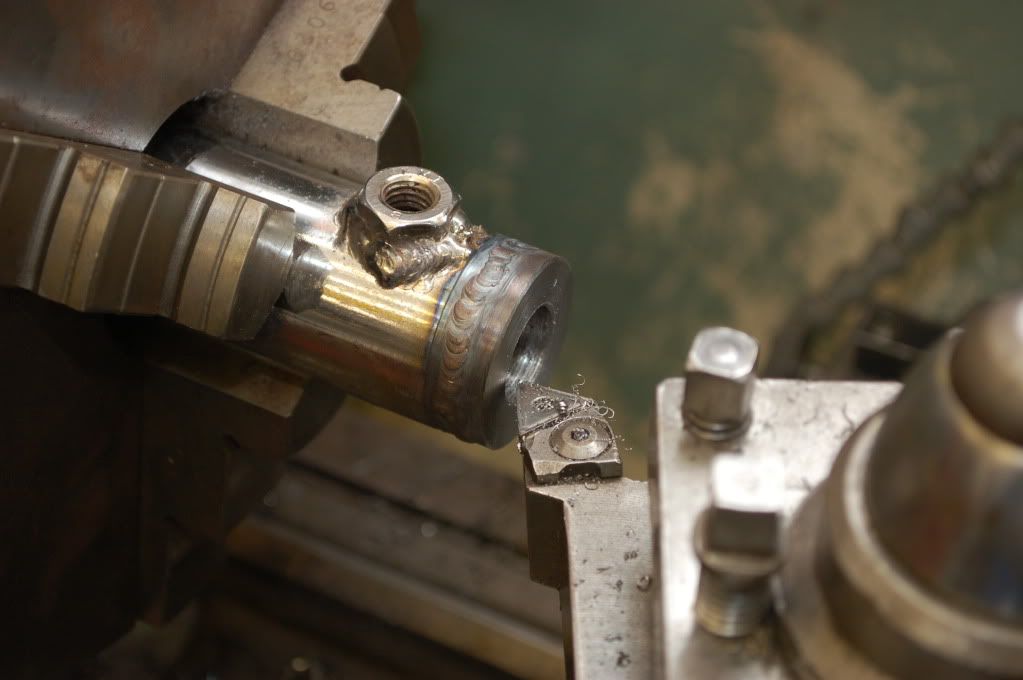
I was going to use that welded on nut as my holding point for this tool, but decided against that, and ground the nut off.
Found a nut instead.
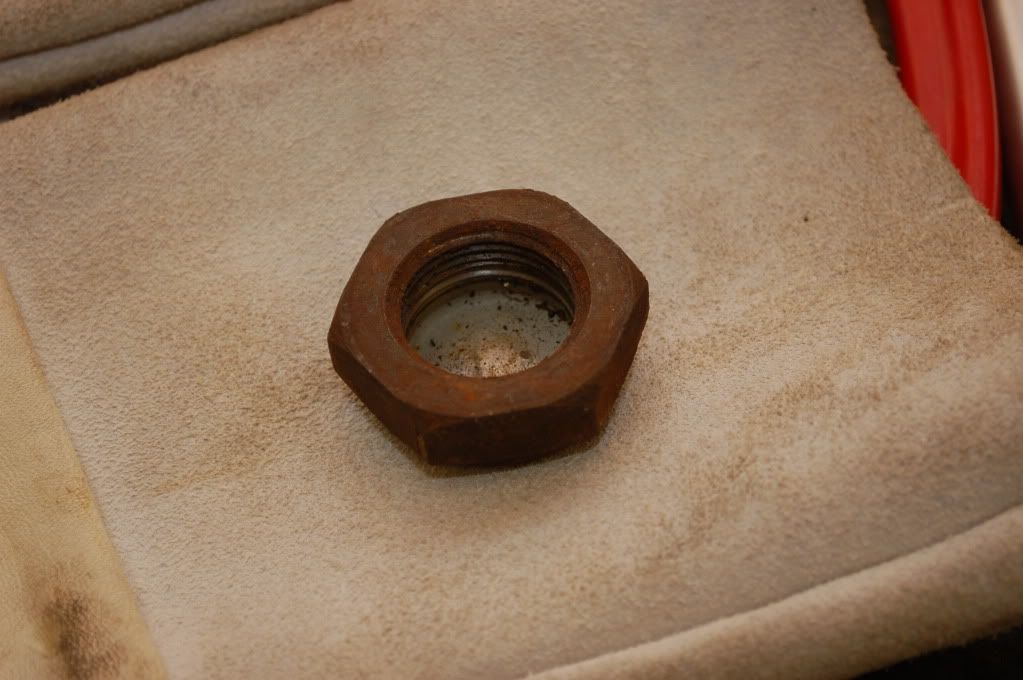
Bored nut out to OD of the tube.
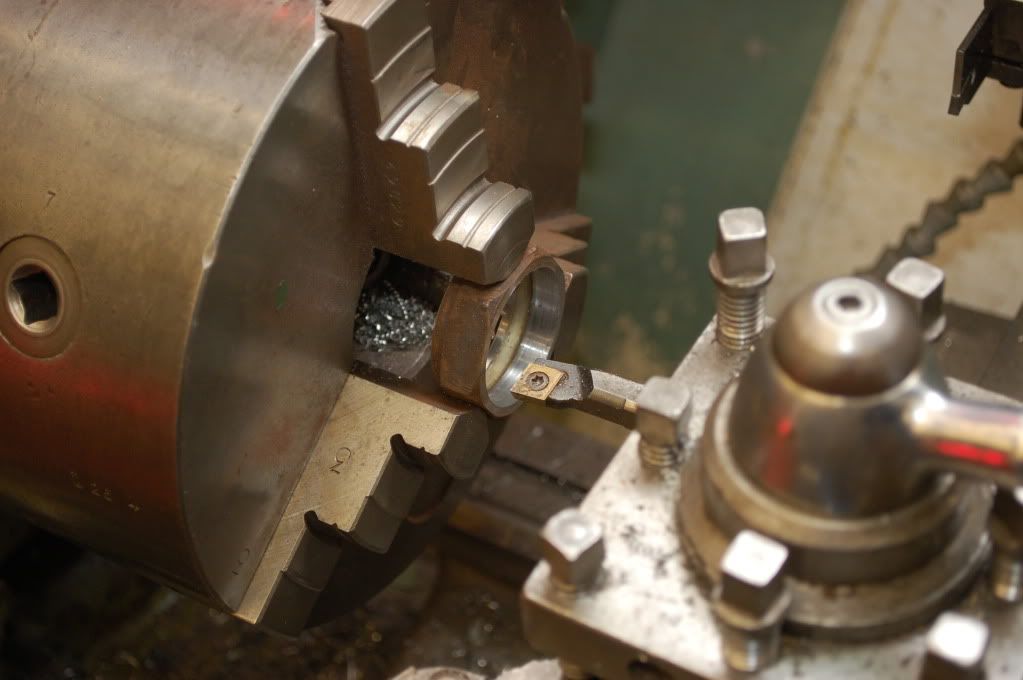
Slid nut onto tube.
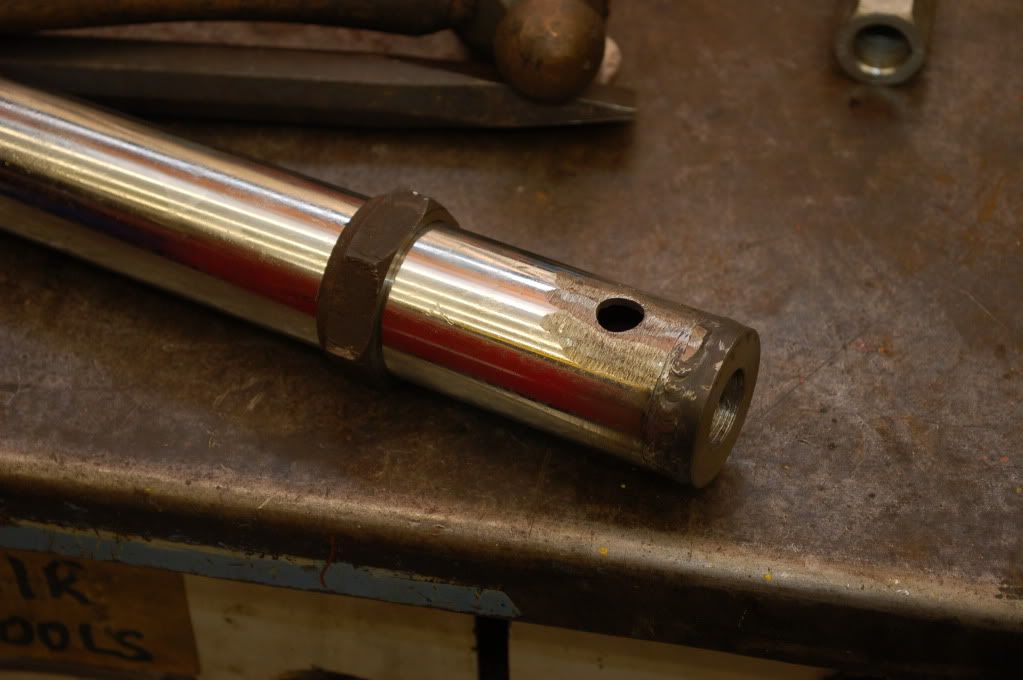
Welded into place.
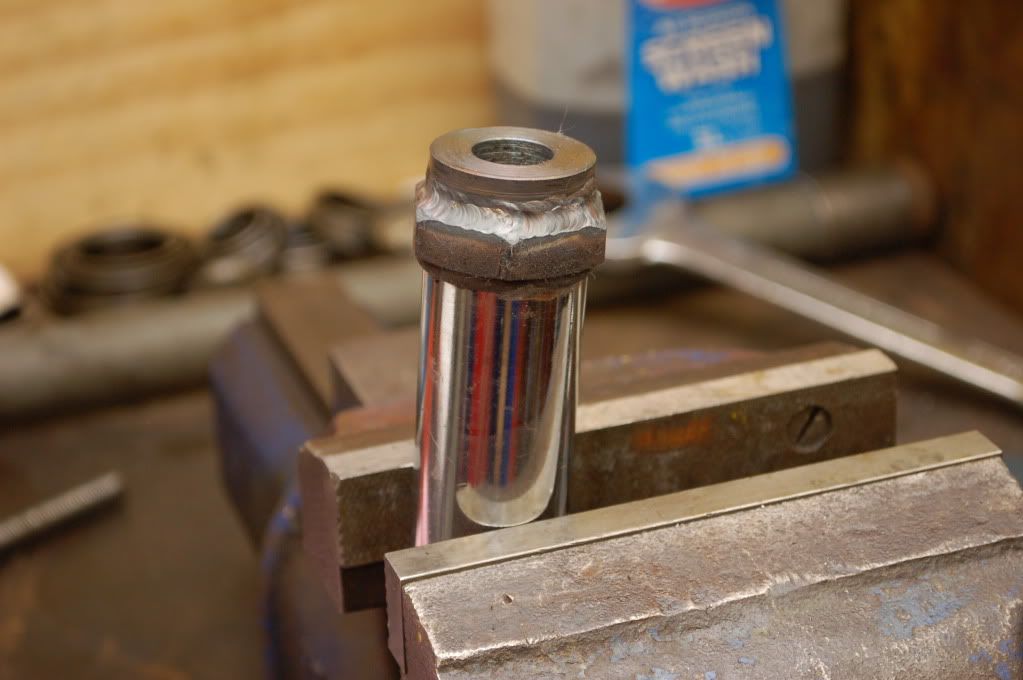
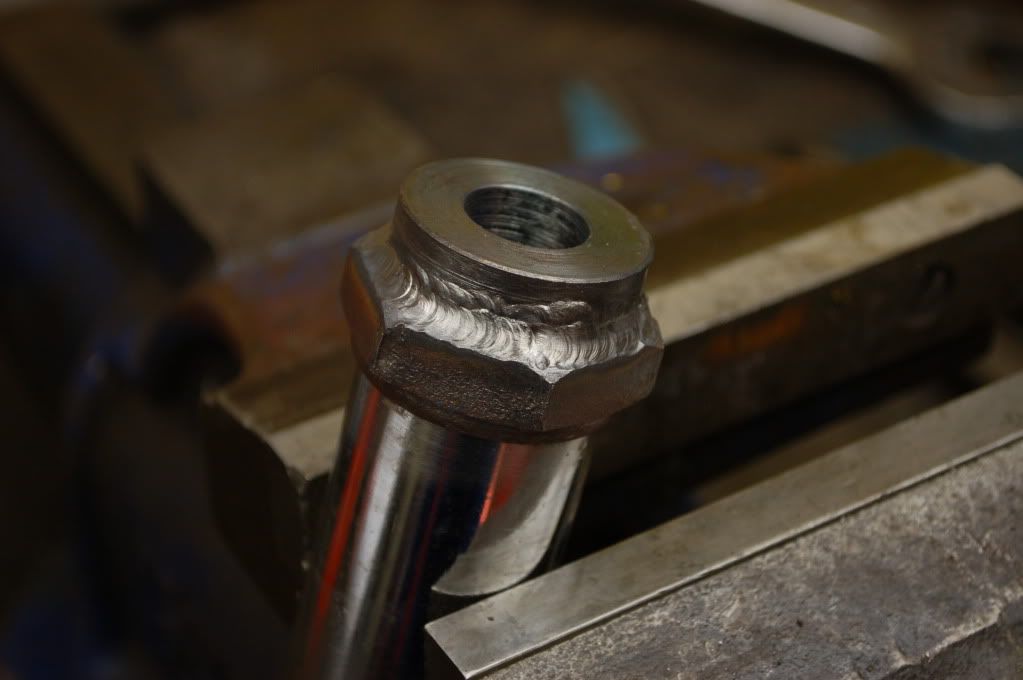
Finished tool ready for action!
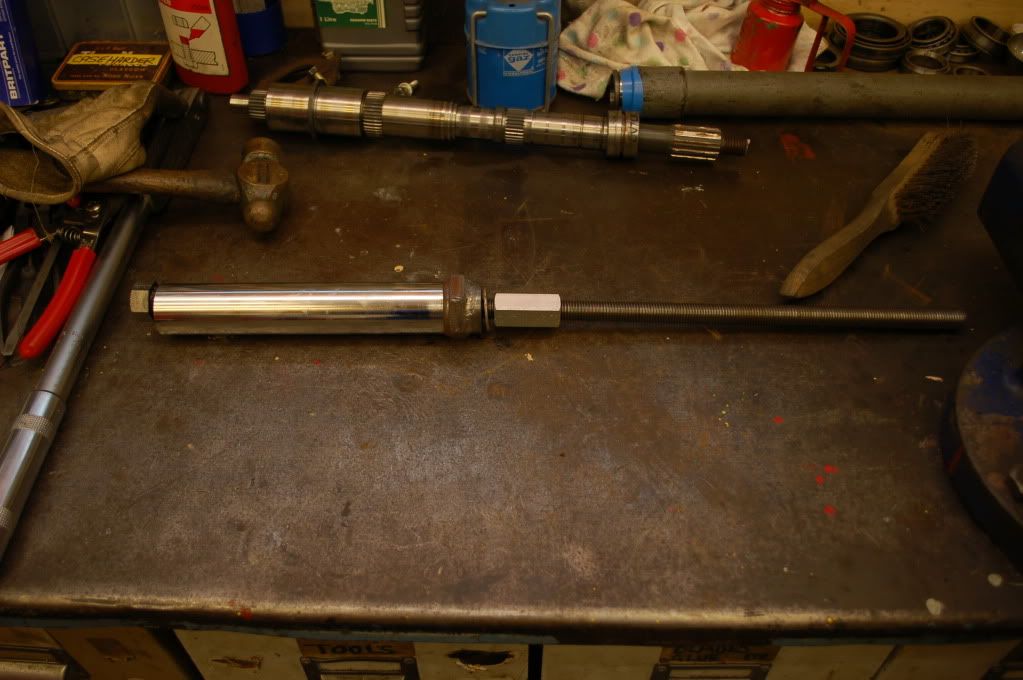
Screw nut/studding onto end of mainshaft.
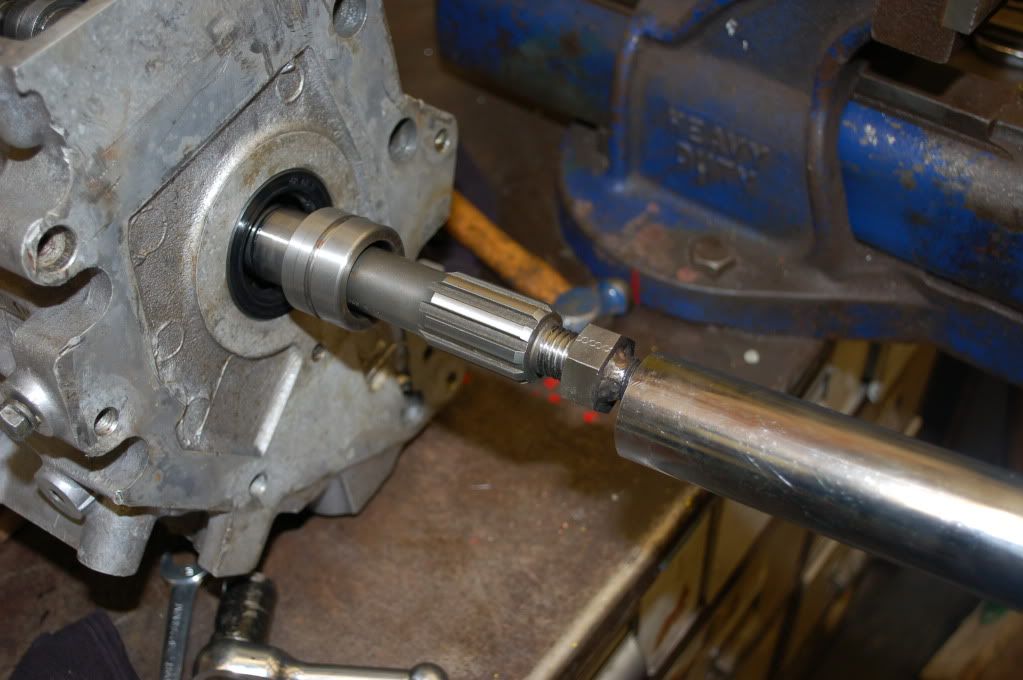
Screw nut down studding to force collar onto shaft. Worked a treat! And no damage to seals [:)]
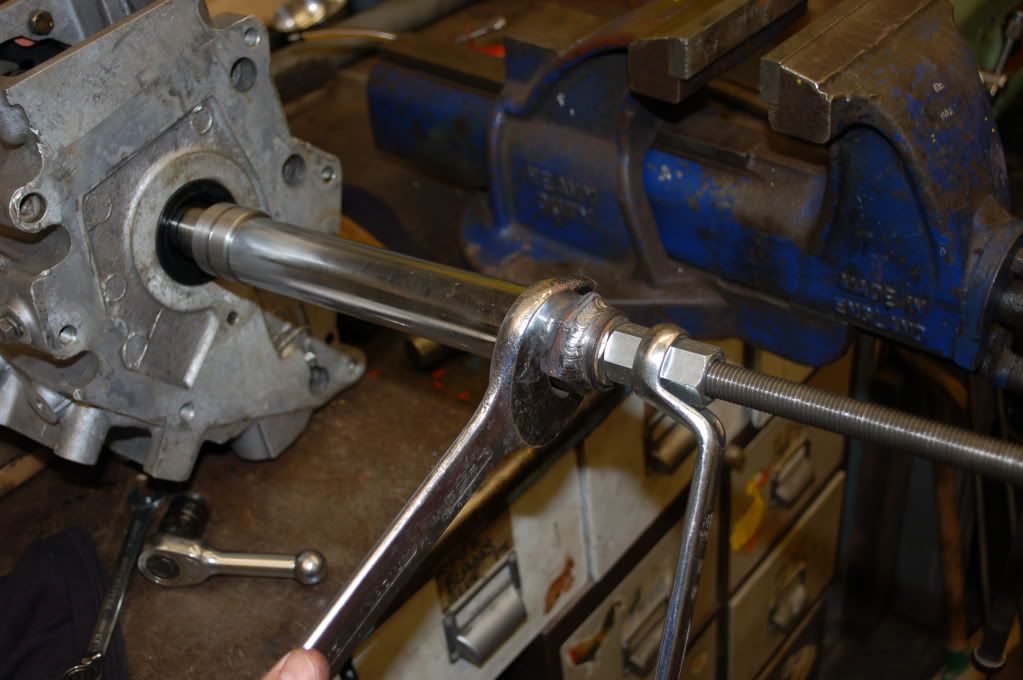
Better photo.
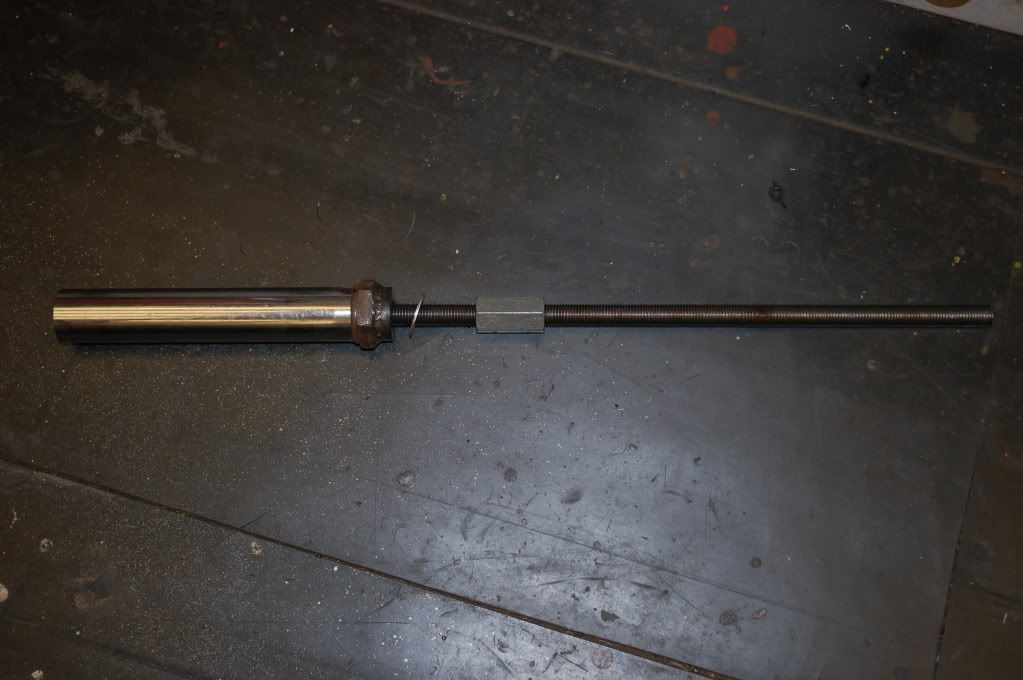
Collar fitted.
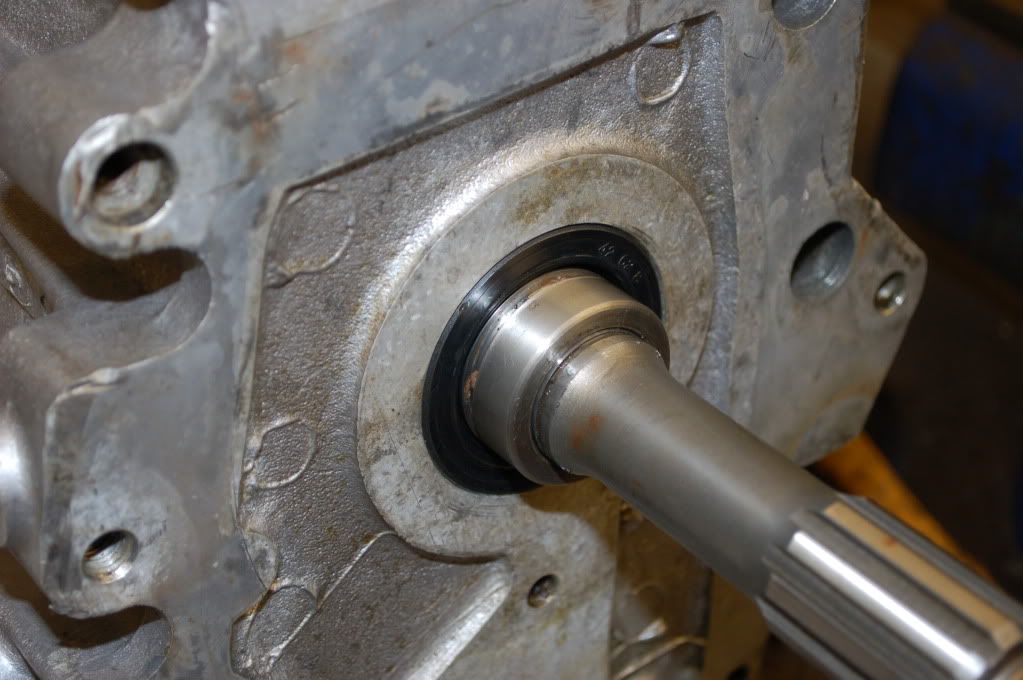
Fit snap ring to shaft.
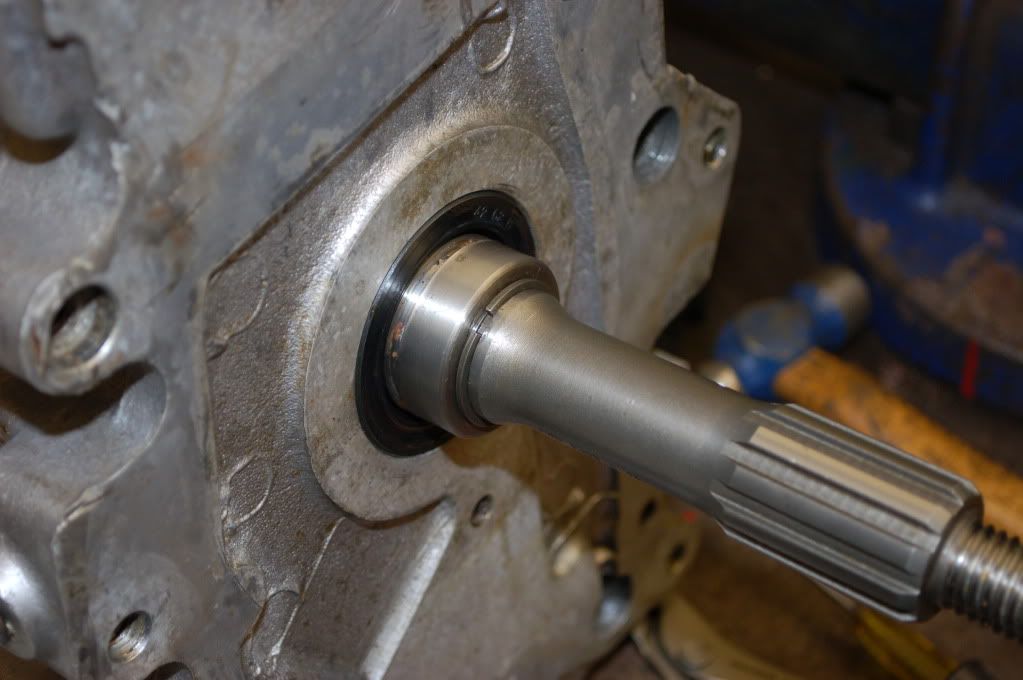
Now we’re up to sorting the endfloat/preload on the main and layshafts. Invert gearbox.
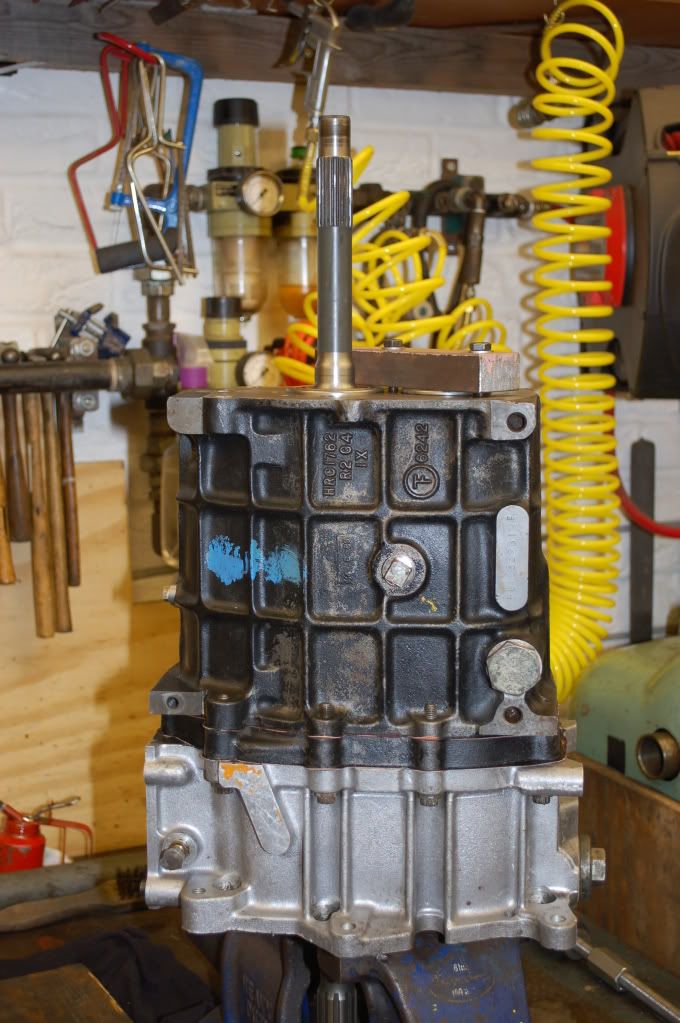
Remove holding tool.
Fit spacer to mainshaft, and measure clearance as per manual. Land Rover manual shows you how to measure using feeler gauges.
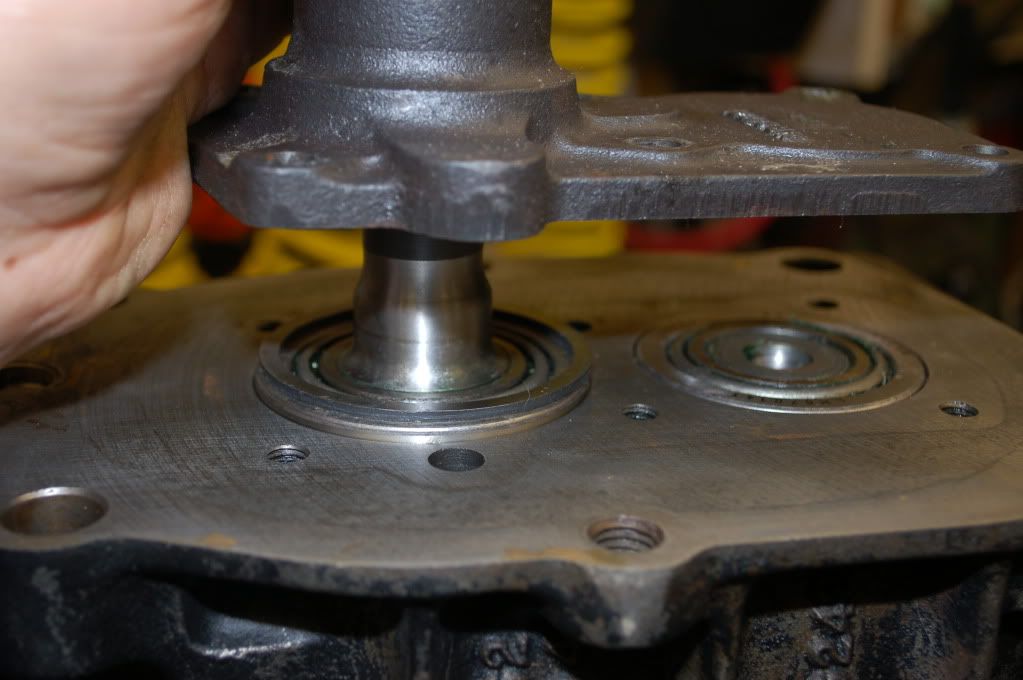
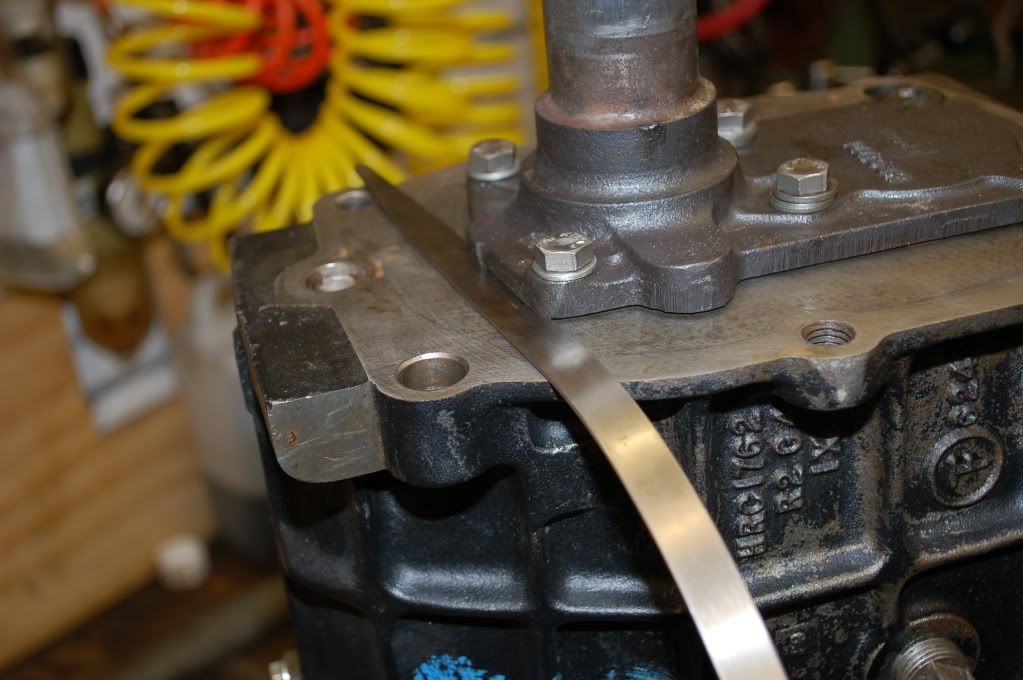
I preferred to use a DTI as per the TR7 manual though.
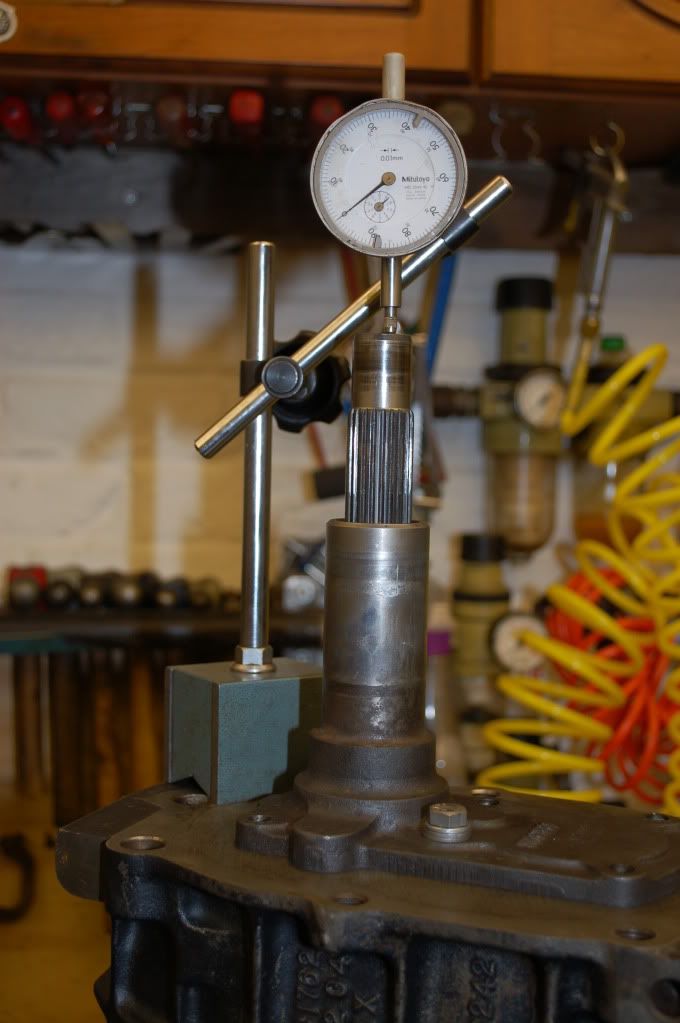
Remove packing piece, and repeat for layshaft. You have to use the feeler gauge method for this shaft.
Replace shims as appropriate. I needed to buy one, but managed to grind another down on a diamond stone.
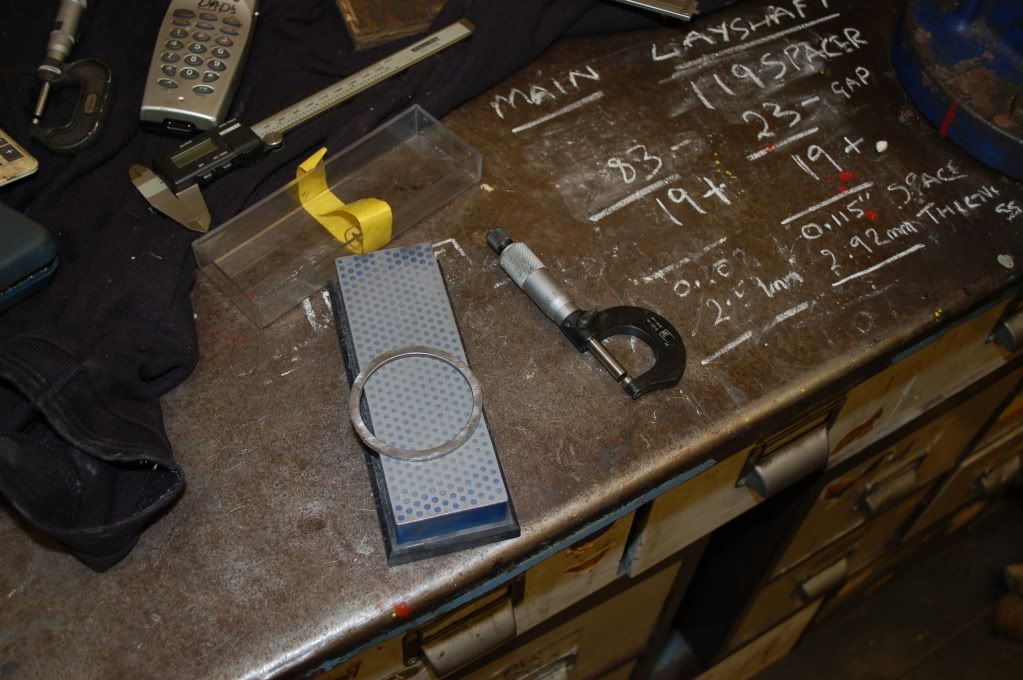
Fit correct size shims, oil seal to housing, and then housing to casing.
These next few pics are just of the gear leavers going on (all stripped and re-greased).
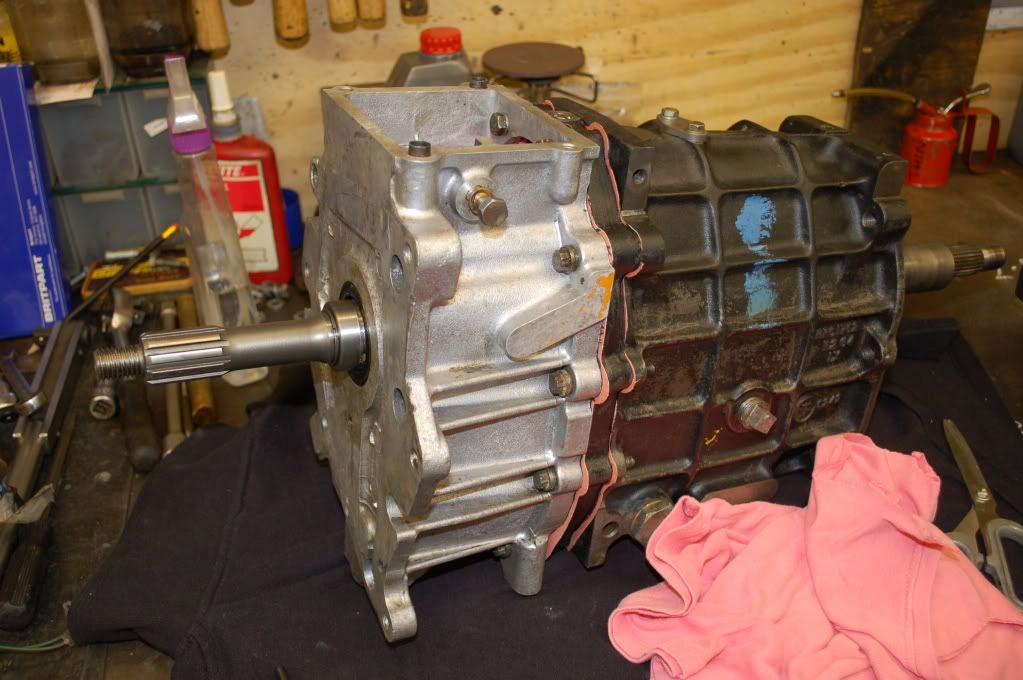
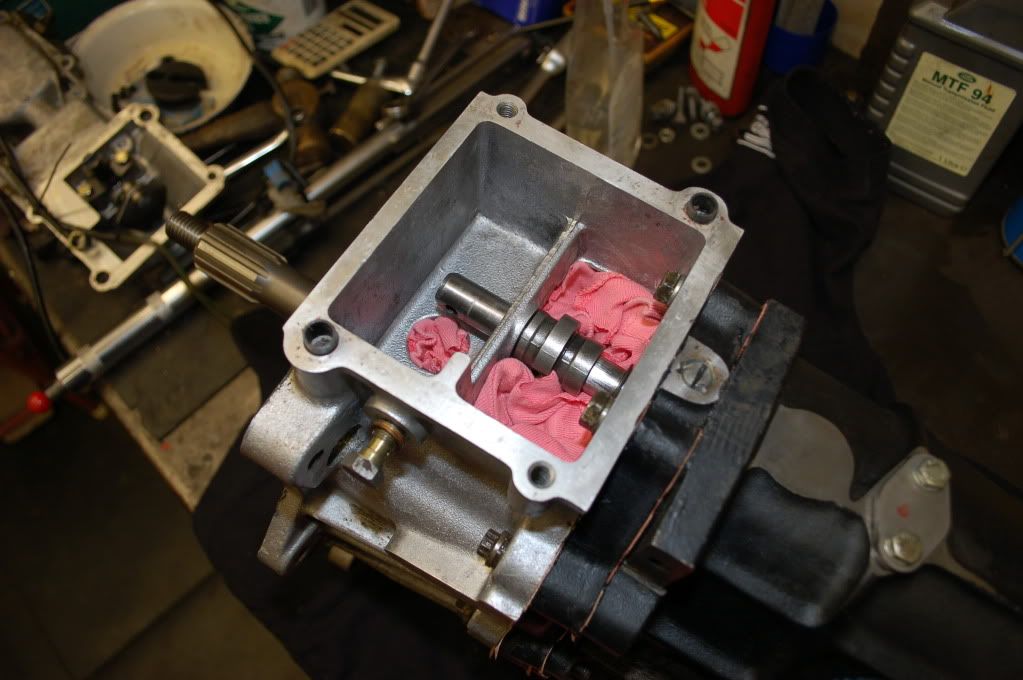
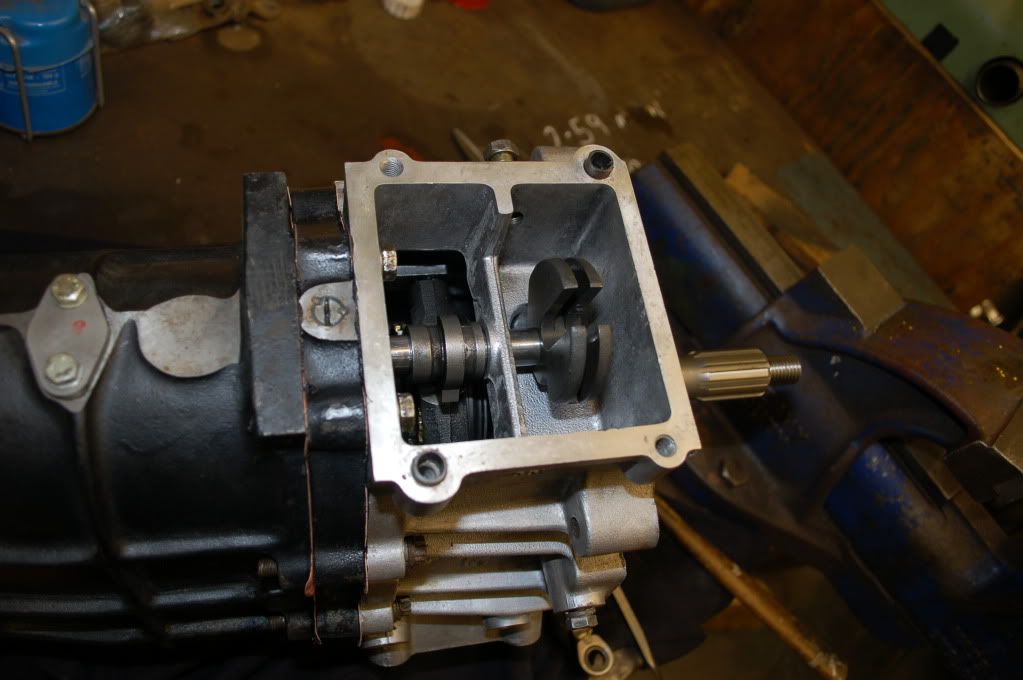
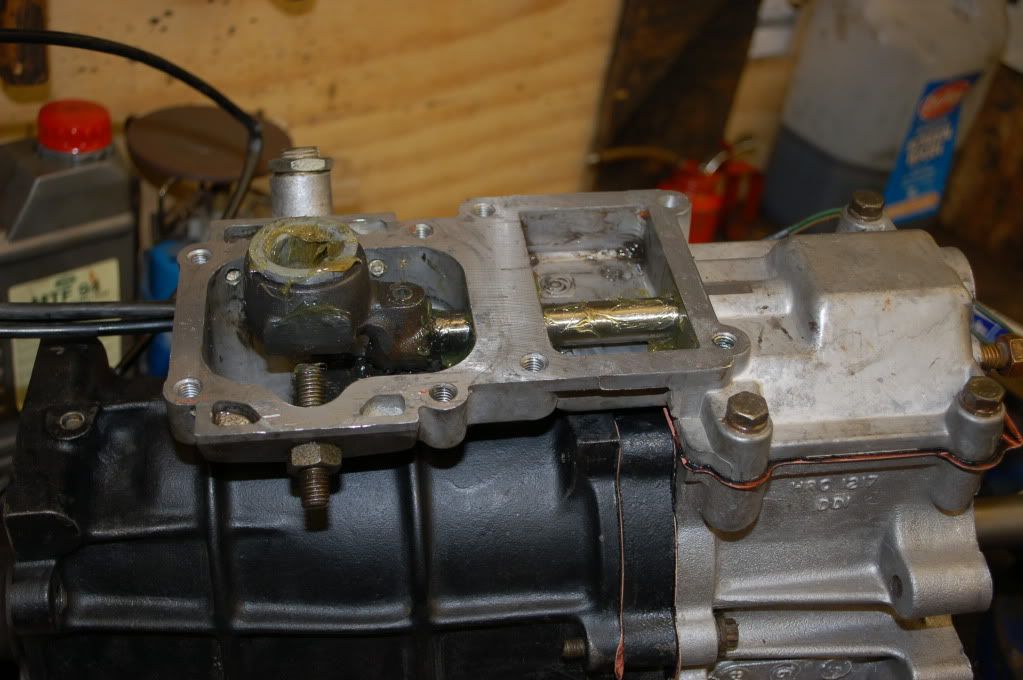
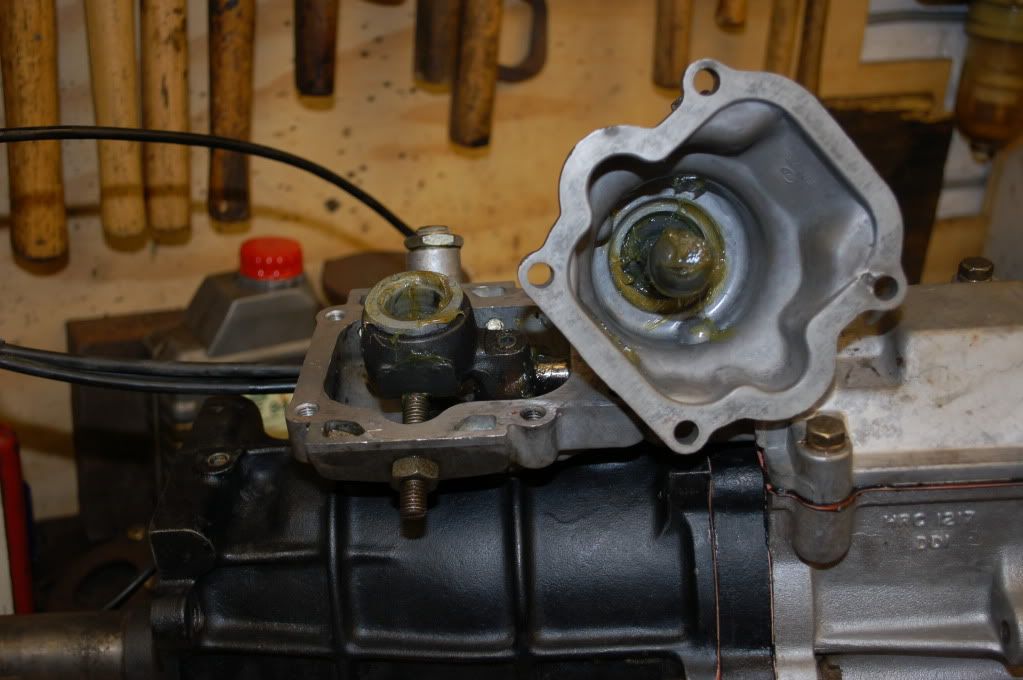
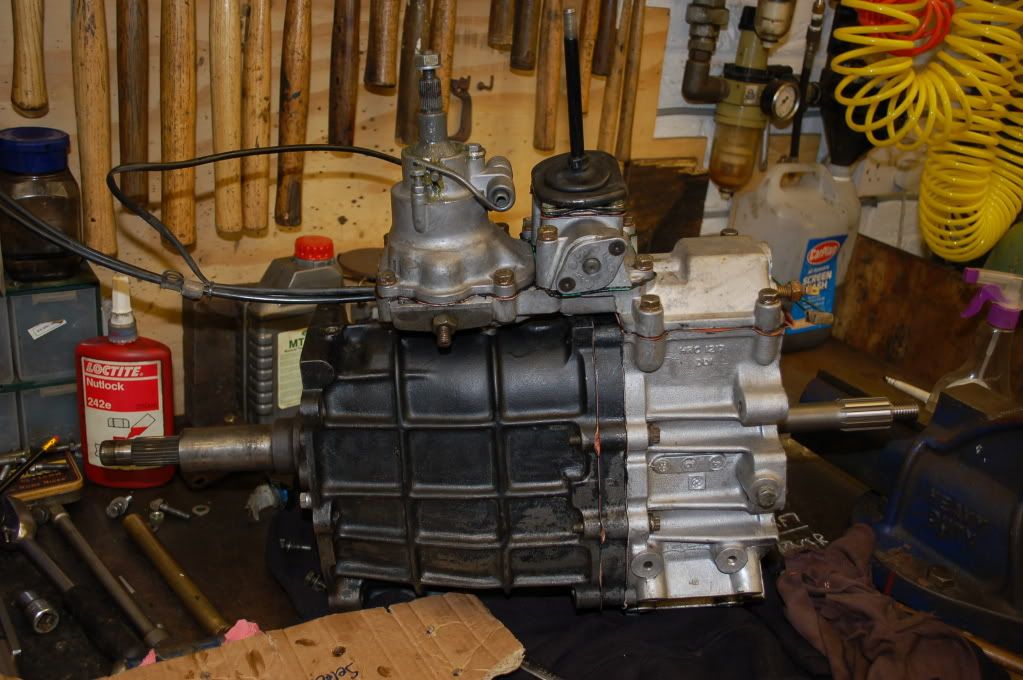
Bell Housing.
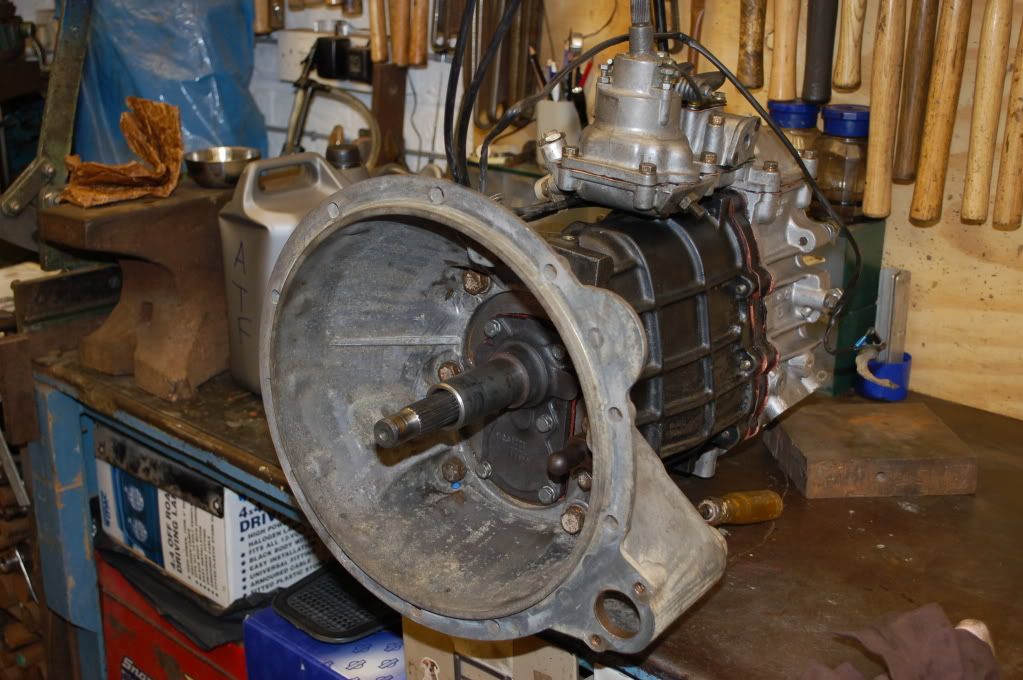
Then the clutch lever arm. There is a ‘heavy duty’ one listed for the Land Rover. In reality, it’s identical with a bit of 1†strip welded in place. The TR7 and 8 can suffer from the same fate as the Land Rover with the pivot pin wearing its way gradually through the arm. This little modification gives it a few more years use…
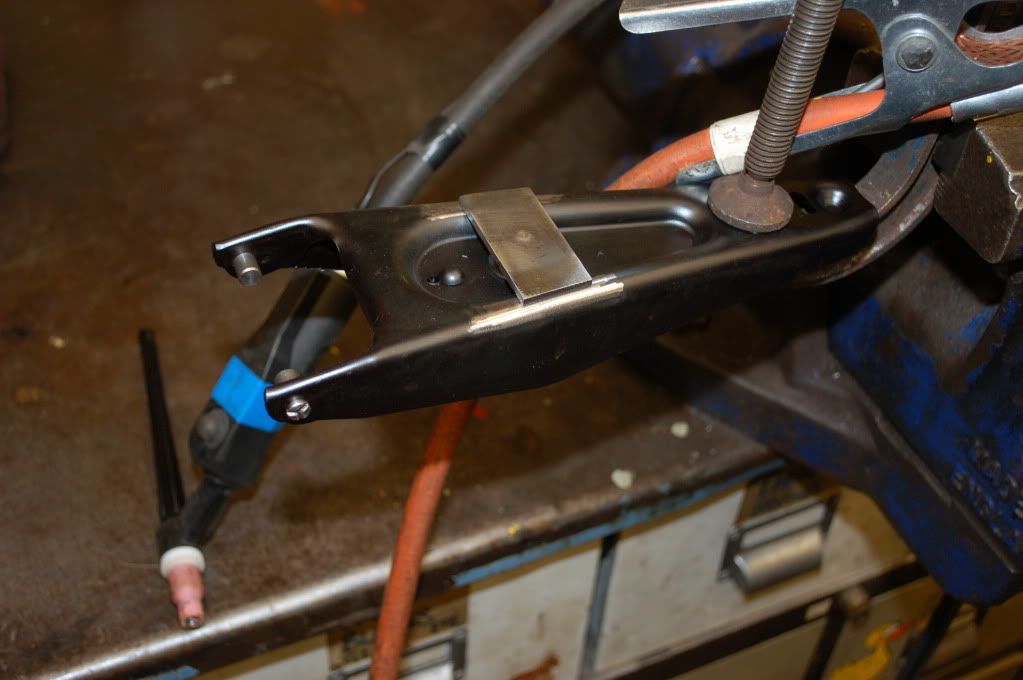
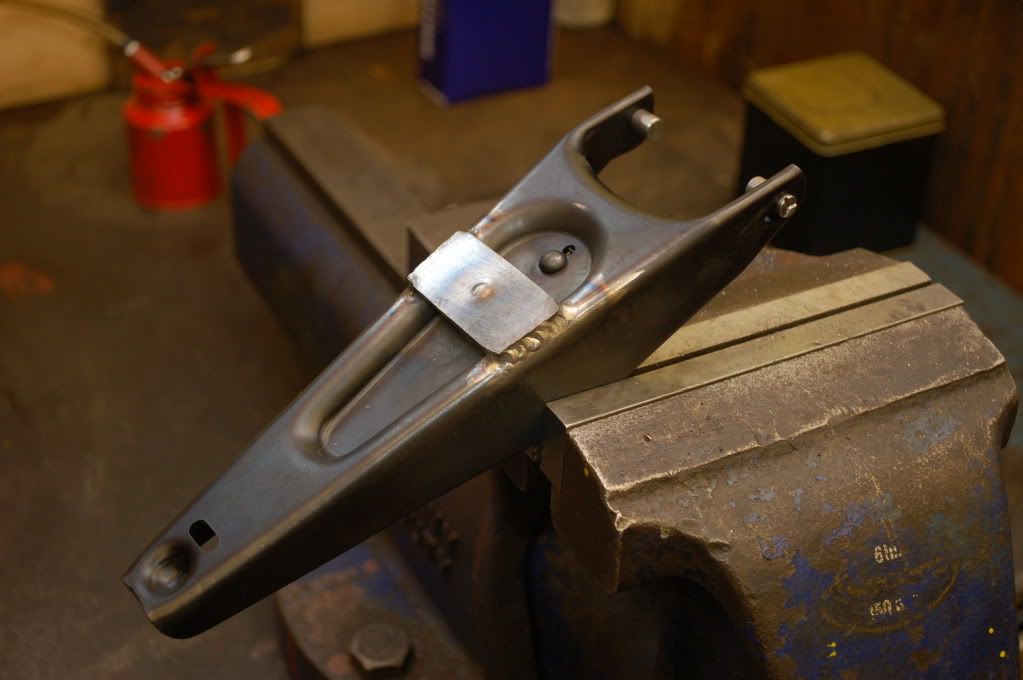
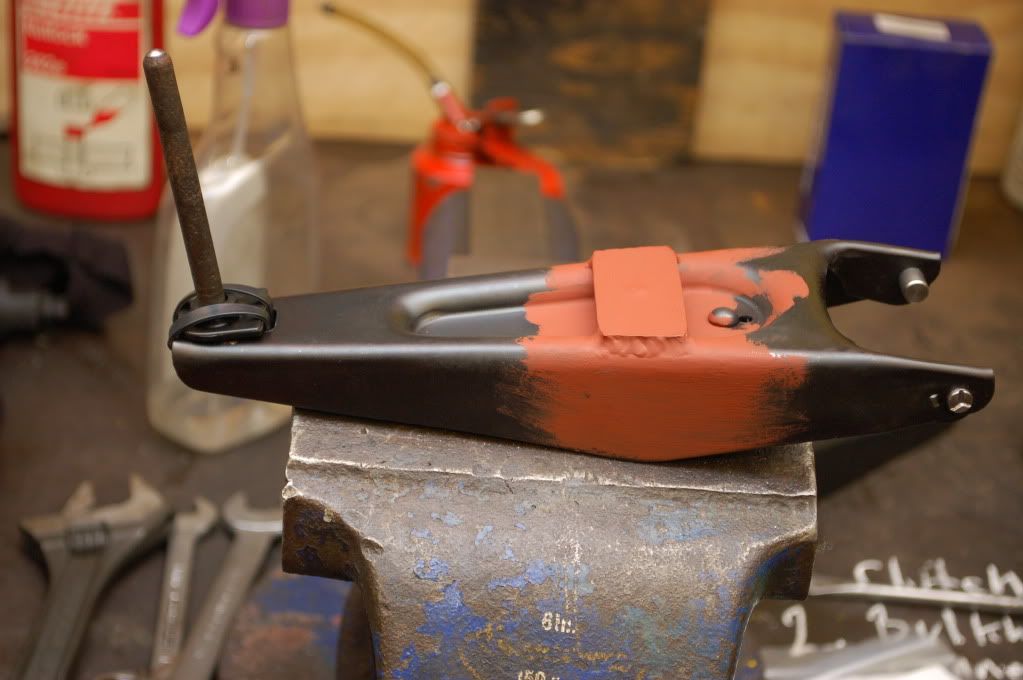
Hope you enjoyed the thread [:)]
Shaun.
</font id="Arial"></font id="size3">
http://www.flickr.com/photos/12691409@N08/
